Possibility of inaccurate Archard Wear result
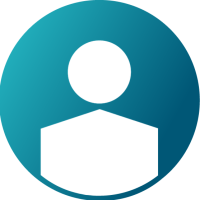
Hello,
I have a problem in EDEM-Acusolve coupling where we use archard wear model to investigate the wear rate of the model implies an inaccurate result. As can be seen below, using the formula of H=W/A where W is wear and A is contact area, I've plotted the graph for the respective speed of 0.5 m/s, 1.5 m/s and 2.5 m/s. The wear volume of the model is higher at 0.5 m/s, the lowest speed compared to 2.5 m/s. To fix this, should I use a smaller scale of mesh when meshing?
Answers
-
Hi Danish,
Could you describe the simulation case? Higher velocity doesn't always have to mean higher wear, for example a higher fluid velocity could be lifting the particles away from the geometry walls meaning less interactions and slower velocities could mean more sliding along the walls rather than been transported via the fluid.I would always recommend having a consistent mesh on the EDEM geometry if considering wear, however if the mesh is the same in all cases this shouldn't impact the results.
Is the measure of wear in this case the sum of all the wear values on the geometry?
RegardsStephen
0 -
Stephen Cole_21117 said:
Hi Danish,
Could you describe the simulation case? Higher velocity doesn't always have to mean higher wear, for example a higher fluid velocity could be lifting the particles away from the geometry walls meaning less interactions and slower velocities could mean more sliding along the walls rather than been transported via the fluid.I would always recommend having a consistent mesh on the EDEM geometry if considering wear, however if the mesh is the same in all cases this shouldn't impact the results.
Is the measure of wear in this case the sum of all the wear values on the geometry?
RegardsStephen
Hi,
The simulation im doing right now is investigating the wear characteristics of a two-phase inline separator. The working principle is similar to that of a hydrocyclone where after the particles are carried through the Internal Swirl Element, particles are pushed towards the wall. The goal is to see the wears happening in the inline separator after a span of 1 second as the simulation is taking too long. I am testing this with wear constant of 1e-12 and at 2% volume fraction (40 000) particles per second running at 3 different speeds as displayed in the graph.
The meshes are constant in all cases as I am using the same solver deck exported from acusolve for the coupling simulation with only changing the speed at the flow inlet for each case.
The values in the graph is from the maximum value from all the geometries in the case in the span of 1 second. I've read from articles that by increasing the velocity at which the particles are entering the inlet, the wear rate would also increase which is the reason why I am confused.
Would changing the meshe value to a smaller value give a different result? Hoping to hear from you soon.
0 -
Danish Imran said:
Hi,
The simulation im doing right now is investigating the wear characteristics of a two-phase inline separator. The working principle is similar to that of a hydrocyclone where after the particles are carried through the Internal Swirl Element, particles are pushed towards the wall. The goal is to see the wears happening in the inline separator after a span of 1 second as the simulation is taking too long. I am testing this with wear constant of 1e-12 and at 2% volume fraction (40 000) particles per second running at 3 different speeds as displayed in the graph.
The meshes are constant in all cases as I am using the same solver deck exported from acusolve for the coupling simulation with only changing the speed at the flow inlet for each case.
The values in the graph is from the maximum value from all the geometries in the case in the span of 1 second. I've read from articles that by increasing the velocity at which the particles are entering the inlet, the wear rate would also increase which is the reason why I am confused.
Would changing the meshe value to a smaller value give a different result? Hoping to hear from you soon.
Hi Danish,
In EDEM the mesh change should only give a greater or lesser distribution of results. If you had 1 large mesh cell vs 2 smaller ones the total wear in the simulation should be the same however the large mesh cell would show twice the amount of wear if it had twice the area.Depending on the case typically I'd look at total wear rather than maximum wear as total would be the sum of the values on all the mesh cells rather than the maximum individual value out of the mesh cells. Also just to note the value of 0.35 meters of wear is exessive, this may be that the wear constant is too large.
RegardsStephen
0