Topic: 2D vs, 3D - Elements
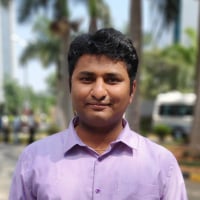

Hey,
I'm currently modelling a cfrp-object. According to a VDI-paper, you have to use 3D-elements for a realistic result and at least 2 elements in thickness direction.
But normally, you can use 2D-elements for some cfrp-objects.
Are shear forces transmitted realistic with 2D-elements?
Regards,
Dome
Answers
-
If you look into the composite Tutorials you will find many examples where composites are modeled as shells with a thickness as a parameter.
This in mind, you can be sure that shear forces are transmitted through shell elements and don't have to worry about it.
The 3D / 2D question is highly related in what you are interested. If you want to look at deformations and forces which are normal to shell elements you will have bad luck as a 2D Element does not allow displacements into the third dimension (at least I read so).
Maybe you find your answer on the tutorials (e.g. the bike frame or the carbon skateboard, available here in the traning center)
Good luck with that.
0 -
DomeGoes,All
This is a good discussion, some suggestions/questions
Which solver do you intend to use? Some Solvers allow composite definition with only 2d elements like in Optistruct
I see that, 2D elements can be used to calculate shear forces for out of plane bending, and in-plane activity, perhaps you can calculate the shear forces in your model and then see the results first hand
please share such results in the forum
In optistruct you can request out the shear forces using the FORCE/ELFORCE using format opti, the resulting .force file will have the shear force details
Also how are you modelling the composite? will it have many plies? you will be using the pcomp card for the 2d element properties in that case in Optistruct, (here you may want to set the lam option to blank so transverse shear stiffness is calculated , see pcomp card lam options for more information on shear forces and shear stress calculations for composites)
0 -
Hey everybody,
thanks a lot for all your answers!
I intend to use OptiStruct as a solver and the composite will have 3 layers (in CAD), each with +-45° plies (in HyperMesh), between them an adhesive layer.
What do others think?See attached file for a better understanding. Yes, I know, I'm a blessed painter
0 -
Do you intend to mesh in a CAD environment?
You sure will have to deal with contacts regarding the insert. For that consider on the analysis page:
Contactsurfs for the definition of your faces
Interfaces for pairing master and slave0