Some questions regarding ESLM
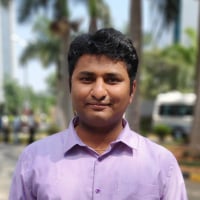

Hallo,
I am very much interested in the recently introduced equivalent static load method in Optistruct. I read in the manual that optimization of an explicit dynamic problem is possible.
I would like to optimize an explicit dynamic metal forming problem (until now calculated in Radioss) with nonlinearities in geometry, material and contact.
Using Optistruct I would like to implement a free shape optimization and allow the tool’s nodes to be moved. The optimization response should be an external calculated best fit value. And so the optimization algorithm will change the tool shape until the target performance comparison of the metal sheet is in an appropriate range.
1. Do you think that is possible?
2. Are there examples concerning metalforming/ESLM with HW?
3. Are external Responses allowed with ESLM if not are there alternatives to minimize the deviation between a deformed sheet shape and the desired final result?
Regards
Hannes
Answers
-
Dear Hannes,
This seems to be a bit tricky.
If you are using OptiStruct you may have troubles with your external responses (how do they look like, what kind of format etc.). On the other side, the free shape technology is available which is certainly quite convenient ...Alternatively, you may use HyperStudy (where you easily can reference external responses and process the demanded 'curve fitting'). The disadvantage is that you need to manually create shapes with Morphing.
Would you be interested in the latter approach?Regards
Matthias Goelke0 -
hank you for your reply,
of course using Hyperstudy would simplify the procedure. However, I think this is not suitable for my problem. I am simulating a process which couples thickness rolling and forming in one step. On the one hand my tools, the rolls, have a complicated shape which leads to a half of a rotor blade. On the other hand it would be great to have an approach which allows optimizing every structure regardless the shape. Furthermore, parameterization or defining shape variations by morphing would not be required.
Concerning the external response:
I have a CAD model of the final rotor blade shape. This will be meshed in Hypermesh. Within the simulation model I start with an undeformed metal sheet. This metal sheet is meshed with the same Element number and size. After each simulation run I have to read out the node coordinates and compare them with the reference mesh based on CAD data. This comparison could be done by Matlab for example by calculating the average node distance. Then the distance is to be minimized.So the external response is just a scalar value.
What do you think, is there a chance to realize this special kind of optimization?Regards
Hannes
0