Composite Results under Pressure Loading
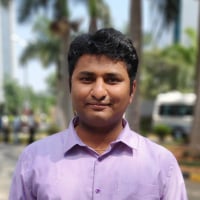

Hi,
I have simulated a Composite Bar under tension and pressure loading. By manual calculation I would expect a stress of approx. 320 MPa and the same stress for tension and pressure loading.
The FE-Simulation shows as a result:
Tension Load: P1 (major principal) = 290 MPa, Composite Failure Index = 0,19
Pressure Load: P1 (major principal) = 5 MPa, Composite Failure Index = 0,15
Do you know why the pressure stress is so much lower compared to the tension stress? I would even expect a higher Failure Index under pressure load, as the bar will probably fail earlier in this load case? Can you please give som advice?
Answers
-
Hello,
Please be aware that pressure stresses do have minus sign while tension stresses have a positive sign. So in your pressure load case you need to:
- look at the MINOR PRINCIPAL STRESS (P3) instead of Major Principal stress to account for the negative sign
- It is also necessary not to look at the 'Max' layer but either at the 'Min' layer or even better to directly look at the 0° layer.When looking at the correct values (choose the above settings in the HyperView Contour Menu -> see attached picture), you will receive P3 = 290 MPa in the 0° layer and thus have the correct pressure stress.
For the failure index: I am not sure if your chosen failure index will account for failure in a pressure load case (e.g. due to buckling or due to delamination). You might need to study the chosen index and check how pressure / tension stresses will be used within this criteria.
If the criteria does not predict failure for pressure, you might need to choose another sort of analysis, depending on the failure mode you are expecting (e.g. performing a buckling analysis).Here are the chosen settings for the above analysis.
P1 is the Maximum of major principal stress or can be the maximum of the tensile stress.
where P3 is the minimum of minor principal stress or the maximum compressive stress.
Reference Guide > Bulk Data Format > Output Data > Results Output:
0