Singularities at connection point between two welded components connected with spring (CBUSH) welds
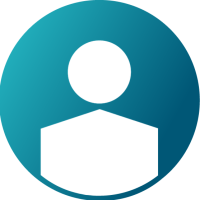
Hello all,
I am modeling a space frame structure made of welded rectangular tubes. I was advised to use CBUSH for welding connections and to use a K line 1-6= 1000000. The mesh is of the highest quality since these tubes are simple and the connectors are realized successfully. The model is constrained with SPCs webed at several nodes. The deformation animation looks realistic, but when we look at the stresses they are very high. What I do is I try to refine the mesh to see if these high stresses will converge. With finer mesh the stresses at the connection points do not converge and I am having trouble to assess the severity of the stresses at these points. I guess in reality that stress concentration at welds should appear, but in the model they are not converging to a final value with finer mesh. Other weld connection techniques are simply not practical and I am not sure why are they in existence, since the quad elements or penta-MiG weld elements are of bad quality or simply don't realize successfully. Any idea why are these singularities appearing at the CBUSH connections and how to go about this?
Best regards,
Viktor Antevski
Answers
-
These singularities are exactly the same principle as your other topic. If you distribute loads/constraints/connections into a single rigid point, it will likely causa singularities in your connected region.
https://community.altair.com/community?id=community_question&sys_id=8017326197757954e3b0361e6253af7a
to avoid that, you could use a different setup, using for example, the 'sealing' connector, which is essentially RBE3+CBSH+RBE3. This owuld better distribute the loads though your model, avoiding 'pin' effect.
Are you modelling spot welds? or seam welds?
For seam welds there are a few studies on how to retrieve more accurate hot spot stresses at the weld.
https://www.sciencedirect.com/science/article/pii/S2092678216302497
0