Why are displacement and stress dependent on mesh size in optistruct?
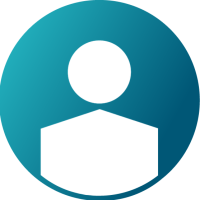
Greetings fellow forum users,
I am working on a static linear analysis of a steel space frame welded structure. I am using tria3 and quad4 for the steel profiles and CBUSH with K1-6 line=1000000. Common FEA wisdom proposes to try different mesh sizes until the results converge towards a final value. Doing smaller mesh sizes models only increased the stresses (this happens at CBUSH weld lines and at sharp corners) and doesn't converge in a reasonably small size mesh. Also, the results are simply not backed by practice and by field measurements!
I made a small test, pictures in attachment, of a plate constrained in the 4 corners with SPC (1-6) and added a force in an arbitrary position. Since stress is a derived value of strain and displacement in this situation is the sum of all strains, I am focusing on the displacements or the compliance in the .out file. So what I get is that with finer mesh I get bigger displacement.
With this I conclude that it is not the common conception that the area of the element is in question, that smaller A gives bigger stress, meaning the error is in the stress calculation, but that the compliance of the stiffness matrix is changed, I see this in the out. file and this totally freaks me out! As far as I get, stress in this situation is out of plane and that may not be compatible with tria3 and quad4 so I tried the other way, in-plane bending, the convergence of displacement/stress still doesn't occur.
Does someone understand why is this the case?
Thank you,
Viktor
Answers
-
With the constraints and load application being at a single point the stress will go to infinity since the load is staying the same but it is applied over a smaller and smaller area.
Look at how quickly the stress goes down. If the stress immediately drops in the second row of elements then the stress concentration is because of the singularity of load application (or constraint).
You could use an RBE3 to spread out the load and constrain more points to get a more realistic representation. Sharp corners are the same since they are concentrating the load on a single point.
0 -
you're seeing stress singularities. This article discuss about this. It is a common issue with FE in general, not only in OS.
https://enterfea.com/stress-singularity-an-honest-discussion/
And naturally, the displacements are also affected by the mesh refinement.
As your mesh is finer you add more DOFs to your model, and it also becomes more flexible.
It is expected to have this. If you try running a simple cantilever beam, using large elements and then start refining the mesh, you will see this kind of behavior.
Another article covering mesh size:
https://enterfea.com/correct-mesh-size-quick-guide/
so, to summarize, ideally you would need a convergence study for both stress and stiffness.
But for singularities, you need to know that refining is not going to solve the issue, and it will actually make it worse.
0 -
And naturally, the displacements are also affected by the mesh refinement.
As your mesh is finer you add more DOFs to your model, and it also becomes more flexible.
It is expected to have this. If you try running a simple cantilever beam, using large elements and then start refining the mesh, you will see this kind of behavior.
Makes sense, going finer affects the hotspots most I agree, but also the nominal stresses throughout the plate are affected since the model has lower stiffness globally. Refining makes the stiffness lower and lower.
So I tried to further constrain the plate, so that both sides are now constrained in a line, not a corner. The result converges this time, from stress of 520 at 10mm mesh to 630 at 0.5mm mesh and also the displacements.
Is it safe to say that the model should be also sufficiently constrained in order to converge to a final result at a definite mesh size? That leaves me with a conclusion that our space frame model is not sufficiently constrained although we are modeling it as it is suspended in nature. These hotspots arise in the CBUSH welds as I've said. So, any suggestions?
Thanks a lot Koga and Buchanan0 -
Viktor Antevski said:
And naturally, the displacements are also affected by the mesh refinement.
As your mesh is finer you add more DOFs to your model, and it also becomes more flexible.
It is expected to have this. If you try running a simple cantilever beam, using large elements and then start refining the mesh, you will see this kind of behavior.
Makes sense, going finer affects the hotspots most I agree, but also the nominal stresses throughout the plate are affected since the model has lower stiffness globally. Refining makes the stiffness lower and lower.
So I tried to further constrain the plate, so that both sides are now constrained in a line, not a corner. The result converges this time, from stress of 520 at 10mm mesh to 630 at 0.5mm mesh and also the displacements.
Is it safe to say that the model should be also sufficiently constrained in order to converge to a final result at a definite mesh size? That leaves me with a conclusion that our space frame model is not sufficiently constrained although we are modeling it as it is suspended in nature. These hotspots arise in the CBUSH welds as I've said. So, any suggestions?
Thanks a lot Koga and Buchananadding a constraint in a single node, or applying a force in a single node, will likely create singularities as well.
i like the analogy to the 'bed of nails trick'.
If you distribute your mass over 1 single nail, you would get hurt, as the pressure concentrates in a single point.
Now if you lie over a bed of nails, then the pressure distributes a lot better.
It is a similar principle. If you apply a point load, your model would likely present high stress around this node.
This is shown in the first link I've sent previuosly.
0