Drop Test - High Contact Energy - High Energy Error - Unrealistic Deformation - RADIOSS
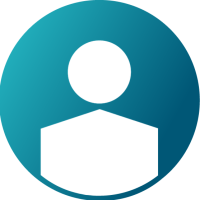
I am performing battery pack drop test in Radioss. In the results it is showing-
1. High contact energy, about 15% of total energy. How can I reduce it? (TYPE2, TYPE7 and TYPE24 contacts are used in the model)
2. Energy error is 15%. How to reduce energy error? (Hourglass energy is almost negligible as compared to total energy)
3. Unrealistic deformation at the corner on which the battery pack falls on the ground. Why it is happening and how to correct/avoid it?
Thank You.
P.S.: Please find the images attached.
Answers
-
Hi Neeraj,
Contact energy depends on type and stiffness of contacts you use. You can check the values that you have specified.
Regarding the next question, it is hard to say without taking a look at the model. It would be easy to find something looking at it.0 -
Ram Dhiwakar,
TYPE2, TYPE7 and TYPE24 contacts are used in the model.
0 -
Neeraj Kumar said:
Ram Dhiwakar,
TYPE2, TYPE7 and TYPE24 contacts are used in the model.
For penalty contacts (TYPE 7, TYPE 24) your high energy may be due to stiffness of contact definition (either too high or too low), you should use a 'physical' property for your ground plane even if it is then rigidised, as the physical props are used in contact stiffness calculation (e.g. steel mat props and a gauge of e.g. 1mm, not super stiff and super thick)
If you can't share the model, can you share at least your contact cards? And unit system and modulus/gauge of components in contact, we can comment on if there is anything we would do differently?
0 -
Paul Sharp_21301 said:
For penalty contacts (TYPE 7, TYPE 24) your high energy may be due to stiffness of contact definition (either too high or too low), you should use a 'physical' property for your ground plane even if it is then rigidised, as the physical props are used in contact stiffness calculation (e.g. steel mat props and a gauge of e.g. 1mm, not super stiff and super thick)
If you can't share the model, can you share at least your contact cards? And unit system and modulus/gauge of components in contact, we can comment on if there is anything we would do differently?
Paul Sharp,
1. I have attached screenshots of TYPE7 and TYPE24 contacts.
2. For ground, I created a planar shell mesh and fixed each node of it. I have attached picture of the properties of the ground.
3. Units: Tonnes for Mass and MPa for stress.
0 -
Neeraj Kumar said:
Paul Sharp,
1. I have attached screenshots of TYPE7 and TYPE24 contacts.
2. For ground, I created a planar shell mesh and fixed each node of it. I have attached picture of the properties of the ground.
3. Units: Tonnes for Mass and MPa for stress.
Hi, I don't see any new attachments?
For Ground, it is better to create an '/RBODY' with all nodes of the ground plane as secondary and an independent main node, then constrain the main node of that RBODY (this removes the calculation cost of the ground from the model).
0 -
Paul Sharp_21301 said:
Hi, I don't see any new attachments?
For Ground, it is better to create an '/RBODY' with all nodes of the ground plane as secondary and an independent main node, then constrain the main node of that RBODY (this removes the calculation cost of the ground from the model).
Paul Sharp,
Now I added the pics to the Question's attachments.
Please check if you can find them.
0 -
Neeraj Kumar said:
Paul Sharp,
Now I added the pics to the Question's attachments.
Please check if you can find them.
You don't say what you are using the T7 and T24 for exactly? If they are both between object and ground, you only need one of them.
My recommendations below
Not sure why you have the small Ipen_Max set on the type 25?
For both T7 and T24, you should set istf=4 (this will use your battery stiffness as the base of the contact stiffness calculation, default would be to use the main side of the contact (which I am assuming is the ground)
For Type 7, you should set the params as I have shown here, if the energy is still too high you can try modifying the 'stmin' value up down (maybe add stmax)
Igap uses auto calculated thickness (half your ground plane in this case probably), at default it is using full thickness of your ground plane.
Gapmin is needed to stop the main thickness overriding the calc.
Iform changes to a more efficient friction calculation (should increase timestep/reduce added mass)
Inacti = 6 removes initial penetrations if there are any (you shouldn't have any ideally!) by locally resetting contact thickness
1 -
Paul Sharp_21301 said:
You don't say what you are using the T7 and T24 for exactly? If they are both between object and ground, you only need one of them.
My recommendations below
Not sure why you have the small Ipen_Max set on the type 25?
For both T7 and T24, you should set istf=4 (this will use your battery stiffness as the base of the contact stiffness calculation, default would be to use the main side of the contact (which I am assuming is the ground)
For Type 7, you should set the params as I have shown here, if the energy is still too high you can try modifying the 'stmin' value up down (maybe add stmax)
Igap uses auto calculated thickness (half your ground plane in this case probably), at default it is using full thickness of your ground plane.
Gapmin is needed to stop the main thickness overriding the calc.
Iform changes to a more efficient friction calculation (should increase timestep/reduce added mass)
Inacti = 6 removes initial penetrations if there are any (you shouldn't have any ideally!) by locally resetting contact thickness
Paul Sharp,
I will implement the changes you suggested and will check the results.
Thanks for your help.
0 -
Paul Sharp_21301 said:
You don't say what you are using the T7 and T24 for exactly? If they are both between object and ground, you only need one of them.
My recommendations below
Not sure why you have the small Ipen_Max set on the type 25?
For both T7 and T24, you should set istf=4 (this will use your battery stiffness as the base of the contact stiffness calculation, default would be to use the main side of the contact (which I am assuming is the ground)
For Type 7, you should set the params as I have shown here, if the energy is still too high you can try modifying the 'stmin' value up down (maybe add stmax)
Igap uses auto calculated thickness (half your ground plane in this case probably), at default it is using full thickness of your ground plane.
Gapmin is needed to stop the main thickness overriding the calc.
Iform changes to a more efficient friction calculation (should increase timestep/reduce added mass)
Inacti = 6 removes initial penetrations if there are any (you shouldn't have any ideally!) by locally resetting contact thickness
Paul Sharp,
I implemented the changes in Contacts, as you suggested. Those changes are working.
Then I deleted the shell mesh which I used for creating wall, and created /RWALL/PLANE. But after doing that, I am facing following issues-
1. Unrealistic deformation at the corner, on which the casing of the battery pack falls on the ground. Why it is happening and how to correct it?
2. The total energy and total translational energy are decreasing with time, but the energy error is +ve, the energy error should be -ve?
I am attaching the model file, it contains only casing and the rigid wall. Please have a look at it.
0 -
Neeraj Kumar said:
Paul Sharp,
I implemented the changes in Contacts, as you suggested. Those changes are working.
Then I deleted the shell mesh which I used for creating wall, and created /RWALL/PLANE. But after doing that, I am facing following issues-
1. Unrealistic deformation at the corner, on which the casing of the battery pack falls on the ground. Why it is happening and how to correct it?
2. The total energy and total translational energy are decreasing with time, but the energy error is +ve, the energy error should be -ve?
I am attaching the model file, it contains only casing and the rigid wall. Please have a look at it.
The deformation is visually unrealistic, but the material is doing what is being asked of it. You have set EPSmax of 0.1 and SigMax of 250 on the material. On the stress strain curve, Stress of 250MPa only corresponds to approx 0.045 plastic strain though.
The Impact is easily enough to reach the 250MPa stress limit in the corner elements by the Animation state at 3e-4s.
What happens in LAW2, is that you follow the stress strain curve until you reach one of those 2 max values (in this case the Stress of 250MPa is hit first). From that point on, Stress no longer increases in the element (it is perfectly plastic, offering no more resistance to deformation), at some point a little later the strain limit is also reached (of 0.1) and at that point the stress in the element is set to 0.
So, looking at this snapshot of your model at 3e-4 we can see that, in the corner elements, that already happened, they reached 250MPa quickly, then 0.1 strain, then were reset to 0MPa stress, the elements a little further up aren't far behind, they are nearing 250MPa already too.
Anything you see in these elements beyond this point (the excessive deformation etc), is pretty meaningless, you can ignore them (and the messy animation) as they are effectively 'no longer there' since they have 0 stiffness and no stress. So, though you see a messy animation, those elements don't really exist any more in a structural sense.
A typical approach to get a better physical and visual outcome is to add a failure card to erode the elements when they reach the criteria required. In the attached model I added a /FAIL/BIQUAD to erode the elements once they reach given strains at different stress triaxiality states, I chose values to get element erosion close to the 250MPa stress limit (the values are very much off the top of my head and arbitrary (don't use this for your 'real' runs!).
What you get then is that when the elements 'Fail' they are eroded (removed from the display) so you get a hole!
Regarding the energy error, External Work is accounted for in the global energy balance, and though your TTE is decreasing, you have negative External Work of a little more than that drop, so the total energy balance is slightly positive. It is well within reasonable bounds though, overall error is very low, in my model with failure, the overall balance is slightly negative.
One final point, the part you have sent looks like it is made of sheet metal (being only around 1.2mm thick?) Why haven't you meshed it as a shell part? Using 1 under integrated tetra element through thickness of a part like this is neither efficient or very accurate. I also attached a version with shell representation (same material and failure characteristics as the tetras, 1.2mm gauge) Your original model took 23 minutes to run on my laptop, the shell version takes 17 seconds! Overall energy balance is similar (actually a little better) than the tetra run.
1 -
Paul Sharp_21301 said:
The deformation is visually unrealistic, but the material is doing what is being asked of it. You have set EPSmax of 0.1 and SigMax of 250 on the material. On the stress strain curve, Stress of 250MPa only corresponds to approx 0.045 plastic strain though.
The Impact is easily enough to reach the 250MPa stress limit in the corner elements by the Animation state at 3e-4s.
What happens in LAW2, is that you follow the stress strain curve until you reach one of those 2 max values (in this case the Stress of 250MPa is hit first). From that point on, Stress no longer increases in the element (it is perfectly plastic, offering no more resistance to deformation), at some point a little later the strain limit is also reached (of 0.1) and at that point the stress in the element is set to 0.
So, looking at this snapshot of your model at 3e-4 we can see that, in the corner elements, that already happened, they reached 250MPa quickly, then 0.1 strain, then were reset to 0MPa stress, the elements a little further up aren't far behind, they are nearing 250MPa already too.
Anything you see in these elements beyond this point (the excessive deformation etc), is pretty meaningless, you can ignore them (and the messy animation) as they are effectively 'no longer there' since they have 0 stiffness and no stress. So, though you see a messy animation, those elements don't really exist any more in a structural sense.
A typical approach to get a better physical and visual outcome is to add a failure card to erode the elements when they reach the criteria required. In the attached model I added a /FAIL/BIQUAD to erode the elements once they reach given strains at different stress triaxiality states, I chose values to get element erosion close to the 250MPa stress limit (the values are very much off the top of my head and arbitrary (don't use this for your 'real' runs!).
What you get then is that when the elements 'Fail' they are eroded (removed from the display) so you get a hole!
Regarding the energy error, External Work is accounted for in the global energy balance, and though your TTE is decreasing, you have negative External Work of a little more than that drop, so the total energy balance is slightly positive. It is well within reasonable bounds though, overall error is very low, in my model with failure, the overall balance is slightly negative.
One final point, the part you have sent looks like it is made of sheet metal (being only around 1.2mm thick?) Why haven't you meshed it as a shell part? Using 1 under integrated tetra element through thickness of a part like this is neither efficient or very accurate. I also attached a version with shell representation (same material and failure characteristics as the tetras, 1.2mm gauge) Your original model took 23 minutes to run on my laptop, the shell version takes 17 seconds! Overall energy balance is similar (actually a little better) than the tetra run.
Paul Sharp,
I will implement the /FAIL/BIQUAD and Shell mesh in the model.
Thanks for your help. You explained things in detail.
0