Rotor mechanical set - how to define position at time t=0s
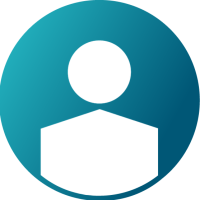
Hello,
I am following one of the example inside flux called: brushless IPM motor - thermal analysis.
Inside case 1 of the example, the mechanical set of the rotor has to be set. The instruction (p. 59 chapter 4.1.7) tells me to set the position of the rotor at time t=0s to 7.5 deg.
The number 7.5 deg seems very odd to me. Why is it not set to 0 deg? How can I calculate this position for any other motor then?
What's even more interesting is that all steps from this example are already done for this model. I am just following the tutorial and trying to see if I have to do something manually with the help of the tutorial. Somehow the position for the rotor at t=0s is already set to 0 deg. And the instruction tells me to put the position to 7.5 deg even though the model is already set to 0deg. Is this a mistake inside the tutorial?
Here are some characteristics of the motor:
Motor ratings This motor with the following data:
Max bus voltage: 500 V
Peak torque: 400 Nm
Max speed: 6000 rpm
Peak power rating: 50 kW at 1200-1500 rpm
is designed for a hybrid electric vehicle.
Motor main
characteristics
Other characteristics of the studied motor are presented below:
48 stator slots
3 phase wye connected stator winding
4 pole pairs of the magnetic field
NdFeB magnets
Lamination type M270-35A
Outer diameter: 242 mm
Stack length: 75 mm
The tutorial is attached to this post.
Best Answer
-
Hello Melih,
The rotor position at "startup" in the magnetic model depends on the BEMF analysis and 7.5° is the zero crossing point of the phase one voltage [see the example "Brushless IPM motor (embedded magnes)" page 71 Overview document - Motor Performance at constant speed]; therefore, it is necessary to align the rotor position to control the gamma angle.
This is normally done by FluxMotor, and there is a macro in Flux to help the user, but it is sufficient to do a BEMF analysis to find it.
However, if you take the losses from the FluxMotor model, you don't need to consider the position in the thermal models because the temperatures are not related to the position in Flux.
Best regards,
Letizia
1
Answers
-
Hello Melih,
The rotor position at "startup" in the magnetic model depends on the BEMF analysis and 7.5° is the zero crossing point of the phase one voltage [see the example "Brushless IPM motor (embedded magnes)" page 71 Overview document - Motor Performance at constant speed]; therefore, it is necessary to align the rotor position to control the gamma angle.
This is normally done by FluxMotor, and there is a macro in Flux to help the user, but it is sufficient to do a BEMF analysis to find it.
However, if you take the losses from the FluxMotor model, you don't need to consider the position in the thermal models because the temperatures are not related to the position in Flux.
Best regards,
Letizia
1 -
Letizia Ferrara_21767 said:
Hello Melih,
The rotor position at "startup" in the magnetic model depends on the BEMF analysis and 7.5° is the zero crossing point of the phase one voltage [see the example "Brushless IPM motor (embedded magnes)" page 71 Overview document - Motor Performance at constant speed]; therefore, it is necessary to align the rotor position to control the gamma angle.
This is normally done by FluxMotor, and there is a macro in Flux to help the user, but it is sufficient to do a BEMF analysis to find it.
However, if you take the losses from the FluxMotor model, you don't need to consider the position in the thermal models because the temperatures are not related to the position in Flux.
Best regards,
Letizia
Hello Letizia,
thank you for your response. I found the example and I also read the more detailed pdf in the folder. And I also noticed that an exported Flux2D model from FluxMotor has this value already inside the mechanical set of the rotor.
Could you help me maybe with another question regarding the solving scenario from the same original tutorial (thermal analysis) ?
I noticed that the solving scenario is controlled over time. It starts from 0 seconds until 0.0135 seconds. In the beginning of the tutorial, the author stated that the electrical period for this machine is T=0.1025 seconds. In some other videos; I have seen that the higher limit for the solving scenario is always a little higher that the electrical period. Why is that the case? Could you tell me how I should decide the lower and higher limit for a given machine?
0 -
Melih Ayyildiz_22506 said:
Hello Letizia,
thank you for your response. I found the example and I also read the more detailed pdf in the folder. And I also noticed that an exported Flux2D model from FluxMotor has this value already inside the mechanical set of the rotor.
Could you help me maybe with another question regarding the solving scenario from the same original tutorial (thermal analysis) ?
I noticed that the solving scenario is controlled over time. It starts from 0 seconds until 0.0135 seconds. In the beginning of the tutorial, the author stated that the electrical period for this machine is T=0.1025 seconds. In some other videos; I have seen that the higher limit for the solving scenario is always a little higher that the electrical period. Why is that the case? Could you tell me how I should decide the lower and higher limit for a given machine?
Hello Melih,
With current generators in the circuit as phase source, you can consider an electric period plus 2 points at the startup (to discard), just to avoid the influence of the initialization type of the model. Using the angle in the solving scenario is easily to set the scenario and evaluate mesh and step of the scenario that are related as you know.
Best regards,
Letizia
0