How to plot Load versus Deflection for a 3 Point Bending Test with RADIOSS ?
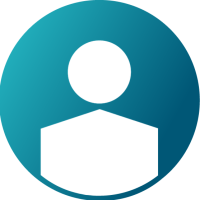
Hello everybody,
I am an engineering student and I take part to the Formula Student project. My objective is to do a 3 points bending tests on a steel tube. So I used the RADIOSS solver to do this. However I am a little bit lost because it is not the same options as Optistruct. Anyway, I was able to realize my test.
However, now I would like to plot the force versus displacement on a graph but I don't know how to do it because when I want to create a graph it doesn't suggest to display the force but only ( velocity , displacement , von mises etc).
Could you please help me and tell me how to do it?
Thank you for your time and attention,
Sincerely,
Best Answer
-
Hi,
the procedure to define output response and post-process the load-displacement results is attached.
1
Answers
-
Hi,
the procedure to define output response and post-process the load-displacement results is attached.
1 -
Simon Križnik said:
Hi,
the procedure to define output response and post-process the load-displacement results is attached.
Hi Simon,
Thank you very much for your help and this detailed video tutorial. Thanks to you, I'm making a big step in my project.
Thanks again,
Jocelyn
0 -
Hi @Simon Križnik ,
I really liked your help last time and I hope you will be able to help me again like last time with the video. I have now started to perform a 3 point bending test on a composite panel. I am using for materials the M25_COMPSH Card Image for both carbon ply and Nomex because I want to do everything in shell for now. I didn't know what else to use for honeycomb.
For the properties, I tried with P11_SH_SAND; P17_STACK; p22_TSH_COMP but I still don't know what I should really use and I don't know what I need to do with Ishell, Ismstr, Ish3n, Idrill etc etc.
For the contacts I tried with type 7 and type 2 and my simulation still doesn't start. Could you help me?
(Don't worry about the values in M25 =1, I am waiting for the missing values)
Thank you for the time you will take to answer me and see you soon.
Jocelyn0 -
There are issues in the model:
-the "solid" component does not have material or property assigned. Set card image to none to avoid error
-the /PROP/TYPE17 (STACK) allows only one integration point for each ply, which may not capture bending stiffness correctly. Instead, use /PROP/TYPE51 with STACK card image for laminate and P_19_PLY card image for plies. For more details refer to Radioss ebook, where I have added composite modeling content.https://altairuniversity.com/free-ebooks/free-ebook-crash-analysis-with-radioss-a-study-guide/
-the type 2 (tied) contact is not appropriate for this simulation. A type 7 general contact interface should be used instead. Also, master and slave sides should be swapped (master should be stiffer, coarse mesh).
-the loading function should ramp up over at least 0.3s to get a quasi-static solutionhttps://www.youtube.com/watch?v=OVBu6zma4ac
https://www.youtube.com/watch?v=te6mvXF_TjU
-the loading fixture shell elements should be meshed with smaller elements for smoother contact pressure distribution. The small element length will not penalize computational efficiency, because they are made rigid by a rigid body.
-when the shell element size is small compared to thickness it loses validity. When h/L is large, shear deformation is at its maximum importance and the user should use solid elements. When h/L is small, transverse shear deformation is not important and thin shell elements are the most effective choice.Because of this, the plate should be modeled with solid elements.
-due to loading, geometry and boundary conditions being symmetric I would recommend using half or quarter symmetry to improve computational efficiency. This will also constrain the specimen in unwanted DOFs. Check Symmetry chapter:https://altairuniversity.com/wp-content/uploads/2014/02/Load.pdf
-check unit consistency: in the BEGIN_CARD you have declared kg, m, s. The density of composite material is not consistent with the density of steel material.
https://www.altairuniversity.com/wp-content/uploads/2012/04/Student_Guide_55-57.pdf
-Ishell, Ismstr, Ish3n, Idrill etc detailed explanations can be found in the Radioss ebook or help documentation. The most important being Ishell/Isolid formulation which can result in hour glassing. Hourglass modes are element distortions that have zero strain energy. Hourglassing may easily lead to excessive distortions To control hourglass assign Ishell-24 and N-5 for shell elements. And for solids use Isolid-14. For explicit structural analysis Ishell=24 formulation (QEPH shells) is recommended, due to balanced accuracy vs. speed. QEPH shells are more accurate for elastic or elasto-plastic loads, whatever the loading type - quasi-static or dynamic. Fully integrated 12 QBAT shells eliminate hourglassing, but are slower to compute. For composites, fully integrated elements are recommended because QEPH 24 is based on isotropic assumption.
2 -
Hi @Simon Križnik ,
I want to thank you very much for your answers. I learn a lot of things. You gave me a lot of really interesting informations to reach my goal. So I made my model again.
However, in order to find a coherent laminate more quickly, I wanted to use only 2D. My idea was to use 3 surfaces (1 for the upper layers, 1 for the honeycomb and one for the lower layers). Then when I will see that I find something good, I wanted to do the same way as you said, that means the honeycomb in 3D. Is that possible?
However, the Analysis still doesn't start. Can you help me again?
PS: I am working with Radioss 2019 and I can't open your Radioss 2020 ☹Thank you very much
Jocelyn
0