How to get the reaction forces in bearings in MotionView/MotionSolve?
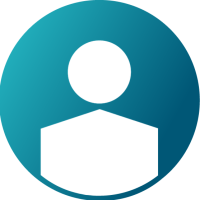
Hello there,
I am trying to analyze a certain problem with regard to bearings. The situation is this. I have a transmission which is powered by an induction motor. The known values are the Power, RPM, gear specifications, and the specifications of bearings.
I wanted to get the reaction force of the bearings with the given inputs above. I tried so many times but the results of my analyses are far from what I expected. (Tried to manually compute it)
BTW here are some information about my set up
I have a total of 6 bodies involved in the analysis
2 gear shafts (driven and driver gears)
4bearings (2 bearings for each gear shaft)
Joints
All bearings are revolute to the ground body
Gear shafts are fixed to the gears
Motion
I input a motion to the driver gear base on the rpm of the motor
Forces
I applied rotational force to the driven gear as torque and made it negative (this acts as the force resisting the rotation of the driver gear) i used the toruqe equivalent to the power of the motor.
Contact
Applied Contact between gears
Ouput
Requested force output on the bodies (4 outputs for each bearing body)
I Hope you can help me with this. Thank you and God Bless
Answers
-
Hello,
Based on the title of your post, your question could be interpreted in one of two ways - either you are not able to find the correct output request for your results, OR, you have the correct output requests, but the forces seem incorrect.
First, you should be able to plot the reaction forces in the bearings by creating Output Requests for the joints of interest (Output Request --> Entity --> Joint). Second, it is difficult to say without seeing your exact setup, but you need to be certain you do not have redundant constraints that could be producing erroneous force results. For example, if you have a gear shaft with three or four revolute joints connecting it to ground/housing, these joints will be redundant with one another. Chances are that when you go to pot results, you will only see reactions on one or two. If you feel this is causing an issues for you, you can create "Compliant" revolute joints (bushings) and assign high stiffness and damping to each direction for the joint, except the direction you need the rotational DOF for. With bushings you can model indeterminant systems in rigid body analysis. Another option is to use primitive joints rather than all revolute, but this will only work for a two-bearing setup. Another option to getting around redundant constraints is to use contact (i.e. shaft and bearing race). However, this should be done as a last resort, as contact simulations can add extra solve time.
I hope this gives you some direction to the answer you need. If not, maybe supply an image for further clarification.
Cheers,
Scott Z
1 -
Scott Ziemba_21777 said:
Hello,
Based on the title of your post, your question could be interpreted in one of two ways - either you are not able to find the correct output request for your results, OR, you have the correct output requests, but the forces seem incorrect.
First, you should be able to plot the reaction forces in the bearings by creating Output Requests for the joints of interest (Output Request --> Entity --> Joint). Second, it is difficult to say without seeing your exact setup, but you need to be certain you do not have redundant constraints that could be producing erroneous force results. For example, if you have a gear shaft with three or four revolute joints connecting it to ground/housing, these joints will be redundant with one another. Chances are that when you go to pot results, you will only see reactions on one or two. If you feel this is causing an issues for you, you can create "Compliant" revolute joints (bushings) and assign high stiffness and damping to each direction for the joint, except the direction you need the rotational DOF for. With bushings you can model indeterminant systems in rigid body analysis. Another option is to use primitive joints rather than all revolute, but this will only work for a two-bearing setup. Another option to getting around redundant constraints is to use contact (i.e. shaft and bearing race). However, this should be done as a last resort, as contact simulations can add extra solve time.
I hope this gives you some direction to the answer you need. If not, maybe supply an image for further clarification.
Cheers,
Scott Z
... Also, in some situations it is possible to use primitive joint types (in-line, in-plane, etc.) in combinations such that the proper DOF of the system are represented, but without the redundancies.
Refer to the MotionSolve Help documentation for more information on redundant constraints.
Scott Z
0 -
Hello Im here again to provide additional information.
So, I guess youre right about those things. Im really thankful about the insights. But im still a bit confused since im new to this software and the required knowledge especially in programming/syntax is a bit overwhelming for me. ( My knowledge is lacking in that area.)
Im really eager to learn this software more so I wont hold back in asking questions. I hope you can provide me some answers and i will be extremely grateful.
So my set up is like this.OBJECTIVE: I want to get the reaction forces on each bearing once this is RUN.
SITUATIONMESH
Meshed it with Hypermesh (3D mesh Trias, Tetra)
I Didnt add any prop or materials. I just used the import tool and set the density to 7.36e-6? As far as i remember.
JOINTS:- I created a revolute joint between all the bearings and the GROUND body
- I Fixed the bearings to their respective shafts
- The gears are also fixed to their respective shaft
- Revolute joint between the shaft and the ground body
MOTION
- I added a motion to the ground-shaft Joint (the shaft of driver gear) equivalent to 900rpm in radians
FORCE
- Since i want to get the reaction force, I added a negative(-) rotational force that is placed in the Gear (driven gear)(yellowgreen).
- "Is that the correct way to set-up this? or is there a correct/another way?
- the force i applied is in Tz (-1e5)
CONTACT
- I added contact between the gears. I tried to remove the contact but once its run, in the result, the driver gear will not rotate with the motion of the driver gear.
OUTPUTS
- Tried several times.
- I tried Force Request and i select the BODY of each bearing
- I also tried FORCE request and i select the joints between the bearings and the ground body
RESULTS
- These are the summary of the results that i end up to
- I always get super high numbers like, way more than what i manually computed.
- I also get zero values for the request
ADDITIONAL INQUIRIES
Is there a way to simplify my set up? I know that this set-up is a mess (overconstrained and many more) But im really stuck in this. Been solving this for months and browsing the internet for answers. Cant find the same set-up/scenario with this one.
- How to use the GEARS function in the toolbar? I just think that it will be useful for this.
- Im really sorry, i tried studying the free e-books regarding motionsolve but the examples are mostly kinematic analysis.
Thank you for your consideration and Kindness. MAY GOD BLESS THIS COMMUNITY. Thanks!
0 -
Scott Ziemba_21777 said:
Hello,
Based on the title of your post, your question could be interpreted in one of two ways - either you are not able to find the correct output request for your results, OR, you have the correct output requests, but the forces seem incorrect.
First, you should be able to plot the reaction forces in the bearings by creating Output Requests for the joints of interest (Output Request --> Entity --> Joint). Second, it is difficult to say without seeing your exact setup, but you need to be certain you do not have redundant constraints that could be producing erroneous force results. For example, if you have a gear shaft with three or four revolute joints connecting it to ground/housing, these joints will be redundant with one another. Chances are that when you go to pot results, you will only see reactions on one or two. If you feel this is causing an issues for you, you can create "Compliant" revolute joints (bushings) and assign high stiffness and damping to each direction for the joint, except the direction you need the rotational DOF for. With bushings you can model indeterminant systems in rigid body analysis. Another option is to use primitive joints rather than all revolute, but this will only work for a two-bearing setup. Another option to getting around redundant constraints is to use contact (i.e. shaft and bearing race). However, this should be done as a last resort, as contact simulations can add extra solve time.
I hope this gives you some direction to the answer you need. If not, maybe supply an image for further clarification.
Cheers,
Scott Z
Hello Im here again to provide additional information.
So, I guess youre right about those things. Im really thankful about the insights. But im still a bit confused since im new to this software and the required knowledge especially in programming/syntax is a bit overwhelming for me. ( My knowledge is lacking in that area.)
Im really eager to learn this software more so I wont hold back in asking questions. I hope you can provide me some answers and i will be extremely grateful.
So my set up is like this.OBJECTIVE: I want to get the reaction forces on each bearing once this is RUN.
SITUATIONMESH
Meshed it with Hypermesh (3D mesh Trias, Tetra)
I Didnt add any prop or materials. I just used the import tool and set the density to 7.36e-6? As far as i remember.
JOINTS:- I created a revolute joint between all the bearings and the GROUND body
- I Fixed the bearings to their respective shafts
- The gears are also fixed to their respective shaft
- Revolute joint between the shaft and the ground body
MOTION
- I added a motion to the ground-shaft Joint (the shaft of driver gear) equivalent to 900rpm in radians
FORCE
- Since i want to get the reaction force, I added a negative(-) rotational force that is placed in the Gear (driven gear)(yellowgreen).
- "Is that the correct way to set-up this? or is there a correct/another way?
- the force i applied is in Tz (-1e5)
CONTACT
- I added contact between the gears. I tried to remove the contact but once its run, in the result, the driver gear will not rotate with the motion of the driver gear.
OUTPUTS
- Tried several times.
- I tried Force Request and i select the BODY of each bearing
- I also tried FORCE request and i select the joints between the bearings and the ground body
RESULTS
- These are the summary of the results that i end up to
- I always get super high numbers like, way more than what i manually computed.
- I also get zero values for the request
ADDITIONAL INQUIRIES
Is there a way to simplify my set up? I know that this set-up is a mess (overconstrained and many more) But im really stuck in this. Been solving this for months and browsing the internet for answers. Cant find the same set-up/scenario with this one.
- How to use the GEARS function in the toolbar? I just think that it will be useful for this.
- Im really sorry, i tried studying the free e-books regarding motionsolve but the examples are mostly kinematic analysis.
Thank you for your consideration and Kindness. MAY GOD BLESS THIS COMMUNITY. Thanks!
0 -
Hello,
Thank you for the extra detail. It might be beneficial for you to create a support ticket for this problem. That way you can send a model to us and we can review. Being able to see the model and navigate its setup will be important to giving you the correct answer.
Your model does not look too complex so hopefully it should be a quick and easy answer.
Thank you,
Scott Ziemba
1 -
Hello again,
Attached is an image of a similar model (gears attached to ground with joints) where I've used three different setups to model the joints - Rigid, Compliant and Primitive joints. Again, I suggest you refer to the MotionSolve Help documentation to learn more about the theory of redundant constraints and their implications. However, for illustrative purposes, I ran three models using each method. You can see in the Rigid model that the force vectors are skewed and also not equally projecting from each joint. For the compliant and primitive models, the load vectors are equal in length and the same in direction. These can also be plotted instead, but as I mentioned - just for illustrative purposes. In all, in the Rigid model, not all loads on each joint are being calculated (or properly calculated) due to DOF redundancies.
If you choose to use Compliant joints, here is what you need to do:
- If they were created with the "Complaint" option activated, then the joint can be toggled between complaint and rigid. Otherwise, you may need to recreate each joint and check the Complaint option when creating them. After changing to compliant, set the non-moveable DOF to the following linear and rotational stiffness/damping values (assuming MMKS units here):
- K(lin) 5000
- C(lin) 250
- K(rot) 1e10
- C(rot) 5e8
These values were taken from the defaults assigned by Inspire Motion. For example, a revolute joint will have stiffness and damping defined for each direction (total 5) except the rotational DOF.
If you choose to use primitive joints, here is what you need to do:
- Use primitive joints for the one shaft-two bearing problem. Any more bearings than 2 and primitives will not work, you will have to use complaint. For one joint, instead of a revolute, use a ball joint. For the other, use an in-line primitive. Together, these two joints only remove a total of 5 DOF, leaving the (1) rotational DOF - the gear shaft axis.
In your specific problem, I see you have shafts also included. Are they necessary to the problem or can they be replaced with the joint from MotionView? Shafts should only be included when considering, for example, mass of the shaft, OR slop/clearance between shaft and hole (would need Contact for this). Keep it simple as possible. IF these are not necessary, it can help simplify the problem - Crawl, Walk, Run.
Scott Z
1 -
... a few other answers to your questions that I forgot to address...
You only need to provide a mesh if you are implementing a flex body in your simulation. Otherwise, a mesh is not needed, as the geometry will be handled automatically, and the the solver will auto-mesh the parts defined in the "Contact" when that time becomes necessary (at solve).
Check the mass of your parts using Tools --> CG Inertia Summary. This can help you see that your density assignments from import are correct.
The way in which you applied the torsional resistance should be fine. You can also use , for example, a damper.
For what you are doing, you could use a Coupler or Contact, as opposed to a Gear constraint. A coupler allows you to relate the motions of the two joints for the two different gears. For example, a rotational velocity coupler using a 2:1 ratio of two revolute joints will cause one gear to rotate 360°/sec while the other rotates 180°/sec. You can model the loads on the joints but there will be no load transmitted through the actual gear tooth interface. Instead the loading is just scaled between two joints directly. On the other hand, a contact is geometry- based. Therefore, loads can be transmitted through the teeth like they would physically. So in all, Couplers should be used when the gear train can be represented as a black box where the user is only concerned with the output of one motion as a function of the other. On the other hand, contact can be used to understand what is happening in the black box, in addition to the output. Contact will require longer solve times, as parts get auto-meshed for the contact algorithm, and the contact solution itself will require more and longer iterations. But it really is geometry-dependent for the most part.
As mentioned previously in this post, large values and zero values on joints is an indication of an over constrained (redundant) system. Hopefully the previous replies to this one will help address that issue.
Finally, if you are not already aware, you may benefit from a reviewing a tool like Inspire Motion (installed with Inspire installer). It will allow you to build and understand these multibody setups much faster, considering the capabilities you are needing and the level of experience you have overall: https://www.youtube.com/watch?v=yYpWsDAAmAY
1 -
Scott Ziemba_21777 said:
Hello again,
Attached is an image of a similar model (gears attached to ground with joints) where I've used three different setups to model the joints - Rigid, Compliant and Primitive joints. Again, I suggest you refer to the MotionSolve Help documentation to learn more about the theory of redundant constraints and their implications. However, for illustrative purposes, I ran three models using each method. You can see in the Rigid model that the force vectors are skewed and also not equally projecting from each joint. For the compliant and primitive models, the load vectors are equal in length and the same in direction. These can also be plotted instead, but as I mentioned - just for illustrative purposes. In all, in the Rigid model, not all loads on each joint are being calculated (or properly calculated) due to DOF redundancies.
If you choose to use Compliant joints, here is what you need to do:
- If they were created with the "Complaint" option activated, then the joint can be toggled between complaint and rigid. Otherwise, you may need to recreate each joint and check the Complaint option when creating them. After changing to compliant, set the non-moveable DOF to the following linear and rotational stiffness/damping values (assuming MMKS units here):
- K(lin) 5000
- C(lin) 250
- K(rot) 1e10
- C(rot) 5e8
These values were taken from the defaults assigned by Inspire Motion. For example, a revolute joint will have stiffness and damping defined for each direction (total 5) except the rotational DOF.
If you choose to use primitive joints, here is what you need to do:
- Use primitive joints for the one shaft-two bearing problem. Any more bearings than 2 and primitives will not work, you will have to use complaint. For one joint, instead of a revolute, use a ball joint. For the other, use an in-line primitive. Together, these two joints only remove a total of 5 DOF, leaving the (1) rotational DOF - the gear shaft axis.
In your specific problem, I see you have shafts also included. Are they necessary to the problem or can they be replaced with the joint from MotionView? Shafts should only be included when considering, for example, mass of the shaft, OR slop/clearance between shaft and hole (would need Contact for this). Keep it simple as possible. IF these are not necessary, it can help simplify the problem - Crawl, Walk, Run.
Scott Z
Hello sir. This is really helpful. Thank you very much. Can I ask how do I add joints to the bearing bodies. I think that the joints overconstraining my set-up is the fact that i have to add FIXED JOINTS for the GEARS to each bearing (a total of (6*4)DOF).
0 -
Scott Ziemba_21777 said:
Hello again,
Attached is an image of a similar model (gears attached to ground with joints) where I've used three different setups to model the joints - Rigid, Compliant and Primitive joints. Again, I suggest you refer to the MotionSolve Help documentation to learn more about the theory of redundant constraints and their implications. However, for illustrative purposes, I ran three models using each method. You can see in the Rigid model that the force vectors are skewed and also not equally projecting from each joint. For the compliant and primitive models, the load vectors are equal in length and the same in direction. These can also be plotted instead, but as I mentioned - just for illustrative purposes. In all, in the Rigid model, not all loads on each joint are being calculated (or properly calculated) due to DOF redundancies.
If you choose to use Compliant joints, here is what you need to do:
- If they were created with the "Complaint" option activated, then the joint can be toggled between complaint and rigid. Otherwise, you may need to recreate each joint and check the Complaint option when creating them. After changing to compliant, set the non-moveable DOF to the following linear and rotational stiffness/damping values (assuming MMKS units here):
- K(lin) 5000
- C(lin) 250
- K(rot) 1e10
- C(rot) 5e8
These values were taken from the defaults assigned by Inspire Motion. For example, a revolute joint will have stiffness and damping defined for each direction (total 5) except the rotational DOF.
If you choose to use primitive joints, here is what you need to do:
- Use primitive joints for the one shaft-two bearing problem. Any more bearings than 2 and primitives will not work, you will have to use complaint. For one joint, instead of a revolute, use a ball joint. For the other, use an in-line primitive. Together, these two joints only remove a total of 5 DOF, leaving the (1) rotational DOF - the gear shaft axis.
In your specific problem, I see you have shafts also included. Are they necessary to the problem or can they be replaced with the joint from MotionView? Shafts should only be included when considering, for example, mass of the shaft, OR slop/clearance between shaft and hole (would need Contact for this). Keep it simple as possible. IF these are not necessary, it can help simplify the problem - Crawl, Walk, Run.
Scott Z
Or can I ask for the File instead so I can recreate the set-up? (ONLY IF ITS POSSIBLE, IM NOT NOT GOING TO ASK IF ITS NOT ALLOWED) thank you very much Sir and Thank you for being here. ^^
0 -
Scott Ziemba_21777 said:
Hello again,
Attached is an image of a similar model (gears attached to ground with joints) where I've used three different setups to model the joints - Rigid, Compliant and Primitive joints. Again, I suggest you refer to the MotionSolve Help documentation to learn more about the theory of redundant constraints and their implications. However, for illustrative purposes, I ran three models using each method. You can see in the Rigid model that the force vectors are skewed and also not equally projecting from each joint. For the compliant and primitive models, the load vectors are equal in length and the same in direction. These can also be plotted instead, but as I mentioned - just for illustrative purposes. In all, in the Rigid model, not all loads on each joint are being calculated (or properly calculated) due to DOF redundancies.
If you choose to use Compliant joints, here is what you need to do:
- If they were created with the "Complaint" option activated, then the joint can be toggled between complaint and rigid. Otherwise, you may need to recreate each joint and check the Complaint option when creating them. After changing to compliant, set the non-moveable DOF to the following linear and rotational stiffness/damping values (assuming MMKS units here):
- K(lin) 5000
- C(lin) 250
- K(rot) 1e10
- C(rot) 5e8
These values were taken from the defaults assigned by Inspire Motion. For example, a revolute joint will have stiffness and damping defined for each direction (total 5) except the rotational DOF.
If you choose to use primitive joints, here is what you need to do:
- Use primitive joints for the one shaft-two bearing problem. Any more bearings than 2 and primitives will not work, you will have to use complaint. For one joint, instead of a revolute, use a ball joint. For the other, use an in-line primitive. Together, these two joints only remove a total of 5 DOF, leaving the (1) rotational DOF - the gear shaft axis.
In your specific problem, I see you have shafts also included. Are they necessary to the problem or can they be replaced with the joint from MotionView? Shafts should only be included when considering, for example, mass of the shaft, OR slop/clearance between shaft and hole (would need Contact for this). Keep it simple as possible. IF these are not necessary, it can help simplify the problem - Crawl, Walk, Run.
Scott Z
Hello. I tried to interpret this the best that i can. In my two gear set-up. Added 4 revolute joints (compliant - 2 for each end). I remove the shafts and the bearing bodies. I just left the Points for each end of the gears for the placement of the joints. So there are only 2 bodies in my set-up.
I added 4 compliant joints and left the Ktz and Ctz 0. And applied the values youve given for the other DOFS.
I added Motion to one of the revolute joints Compliant but once I ran the simulation, the software says that it has an error. The Joint of the motion is not found. So i tried to make that specific joint as compliant and it ran. But the result still looks unreliable. =(
Is it possible if you can provide the Model for your analysis? If its possible, i will study your set-up in order to replicate it. I hope for your positive response. Thank you and God BLess0