Change of material and influence on stress calculation in analysis
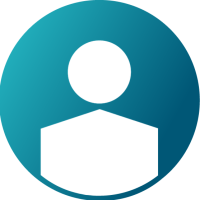
Hello,
I compared maximum stress of my model in a linear static analysis with different materials. I went from steel to 7075 aluminum (lower youngs modulus and higher cross contraction number). The rest of my model including the load cases stayed the same and i expected the stress to be higher in the case of aluminum because of its lower youngs modulus. But the exact opposite was the case. How can this be explained?
I did some research and found this quote in a PDF from altair (https://www.altairuniversity.com/wp-content/uploads/2014/02/postproc.pdf) : 'Changing the material will not require rerunning the analysis for stress (in case of linear static analysis) and a decision could be taken just by comparing the maximum stress value with the yield / ultimate strength of the material'
So i get different stresses in a linear static analysis with different materials, but this quote says an analysis rerun is not required. I am confused.
I highly appreciate if anyone has an explanation for this.
Thank you very much,
Johannes
Answers
-
Altair Forum User said:
Hello,
I compared maximum stress of my model in a linear static analysis with different materials. I went from steel to 7075 aluminum (lower youngs modulus and higher cross contraction number). The rest of my model including the load cases stayed the same and i expected the stress to be higher in the case of aluminum because of its lower youngs modulus. But the exact opposite was the case. How can this be explained?
I did some research and found this quote in a PDF from altair (https://www.altairuniversity.com/wp-content/uploads/2014/02/postproc.pdf) : 'Changing the material will not require rerunning the analysis for stress (in case of linear static analysis) and a decision could be taken just by comparing the maximum stress value with the yield / ultimate strength of the material'
So i get different stresses in a linear static analysis with different materials, but this quote says an analysis rerun is not required. I am confused.I highly appreciate if anyone has an explanation for this.
Thank you very much,
Johannes
Hi Johannes,
Normally, you have to find the same stresses with two difference materials if you are running a linear static analysis.
Can you please share your fem model ?
Cheers,
0 -
Altair Forum User said:
So i get different stresses in a linear static analysis with different materials, but this quote says an analysis rerun is not required. I am confused.
That's totally true. In the linear static analysis, we have to get the same results.
Please find attached a simple model, you can check it by running 2 simulations : the first one using steel and the second one using alum.
Cheers,
0 -
Thanks for the reply! As i went deeper in the analysis and compared the distribution of the stress between steel and aluminum i saw that they are nearly identical. The elements which show different maximum stress are only a few and they are located in areas where contacts are defined. May be this has an influence on the problem?
I attached my fem model, it is a little bit larger.
Thank you very much for your help!
0 -
Altair Forum User said:
contacts are defined.
Yeah, it could be. You deal with a non linear problem that involves contact.
I saw your *fem file. I'm wondering why you use linear static ?
0 -
I don't think I understand what you mean. I chose linear static load steps, because there are no dynamic forces in my model. Does the implementation of contacts mean my problem is automatically non linear? I only used those contacts to define the behaviour between different parts in my model.
Or is there a different reason for your observation that my problem is non linear?
Thank you very much
0 -
Altair Forum User said:
Does the implementation of contacts mean my problem is automatically non linear?
Yes. The contact problem involves non linearities in the variational formulation. So you need Newton scheme to solve and compute the contact pressure and hence the contact stress.
Altair Forum User said:Or is there a different reason for your observation that my problem is non linear?
I said that because you defined the contact which makes the problem non linear.
Altair Forum User said:Thank you very much
You welcome mate
/emoticons/default_wink.png' srcset='/emoticons/wink@2x.png 2x' title=';)' width='20' />
0 -
Do you know a source by chance, that explains why the analysis of different material models does not differ in a linear-static problem?
I also couldn't find information about the contact problem in context linear analysis.
0 -
Altair Forum User said:
that explains why the analysis of different material models does not differ in a linear-static problem?
It's simple. In linear static analysis, the principle of overlapping (superposition) remains valid.
In the end you are trying to solve K*U = F
with :
K : stiffness matrix that involves materials coefficients, geometry ...
U : Displacements
F : Forces
So when you change the materials, directly you change the matrix K ....
In the non-linear problem, it's a bit complicated.
For more informations, you can read some books of the Finite Element Method (Zenkewich books ...)
0 -
Altair Forum User said:
explains why the analysis of different material models does not differ in a linear-static problem?
If you don't understand what Farouk Maaboudallah explained above, then I can explain in a simple way:
You have a rod with cross section area A=10, and you pull it with force = 1000 then stress is S=F/A = 100
That means stress in linear static only depends on external forces (applied forces, constraints) and size of structure, regardless its material
0