RADIOSS - how to set up a model to perform multiple subsequent drop tests
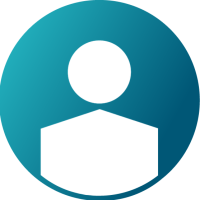
Hello,
I am writing to ask for information on how to properly set up a model for multiple subsequent
drop tests with stress and deformation recovery from the previous load case.
The final aim is to evaluate the ultimate damage and residual functionality (after 2+ drop tests) of the good being virtually tested.
To make myself clear: imagine having a toaster, which dropped from a certain height (hence the initial condition is v_0=sqrt(2*g*height)).
After the contact with the ground and the subsequent residual deformations in the structure, it is in my interest to understand if
there is any function already available in RADIOSS to map the deformations and stresses from this load case to the subsequent one, in which I am re-lifting the toaster, spatially rotating it and making it drop again.
I know that LS-Dyna has already received updates which implemented the mixed Eulerian-Lagrangian formulation + stress re-mapping, but I am wondering if the same could be done in RADIOSS too. And, if that's the case, is there any official guide publicly made available?
Thanks for any help or advince provied, it would be highly appreciated.
Kind regards,
Andrea Corazza
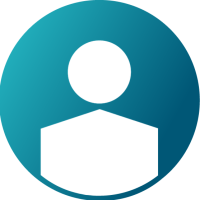
Hi Adriano,
thanks a lot for your quick and kind reply.
I will look into it then.
I'll take the chance to ask two more info regarding the proper documentation
I can refer to related to the followings:
1. Crack propagation/adhesive de-bonding via element death or VCCT in Radioss
2. I assume that /STATE cards will enable me to take into account also pre-stressed wrapping films (thermo-retracting films) when modelling goods packing, I am right?
Thanks again for your time and kindness
Kind regards,
Andrea Corazza
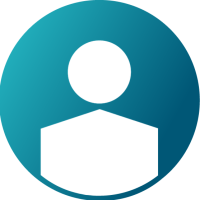

Hi Adriano,
thanks a lot for your quick and kind reply.
I will look into it then.
I'll take the chance to ask two more info regarding the proper documentation
I can refer to related to the followings:
1. Crack propagation/adhesive de-bonding via element death or VCCT in Radioss2. I assume that /STATE cards will enable me to take into account also pre-stressed wrapping films (thermo-retracting films) when modelling goods packing, I am right?
Thanks again for your time and kindnessKind regards,
Andrea Corazza
For adhesive modelling, with failure, look at cohesive elements (/PROP/CONNECT, /MAT/CONNECT, /FAIL/CONNECT)
For pre stressing film wrap, rather than /INISHE (from a /STATE output) I would look at using /EREF or /XREF reference states
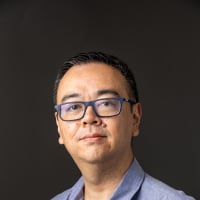

In Radioss you can request to save the /STATE cards, which store the last stress/strain from your initial model, and use them as a initial state for the next simulation.
This is used, for example, in multi-stage forming simulations.
/STATE can store plastic strains, thickness, stresses...
Please take a look at Radioss documentation for further details.
In Radioss you can request to save the /STATE cards, which store the last stress/strain from your initial model, and use them as a initial state for the next simulation.
This is used, for example, in multi-stage forming simulations.
/STATE can store plastic strains, thickness, stresses...
Please take a look at Radioss documentation for further details.