Hyperworks CFD high pressure air flow in small air flow area
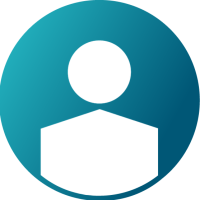
Hi experts,
I would like to ask for your help. I take part in a project, where we want to calculate a flow area outlet veloctity. There are two inlets ( i put 6bar stagnatious pressure) and two outlets with the basic outlet condition. I use default wall setting, S.A. turbulence model and incompressible air flow. Solver controls is originals. The outlet and inlet also 4.8 mm diameter so my average mesh size was 0.5mm and also add the ssme surface mesh control. My problem is that I don't know what the default wall condition do, or what condition should i use ( plastic component in real life). Also use pre-compute flow and turbulence, but the iterations was really slow and I don't think was enough accurate. Also If I check the result near the flow area boundaries the velocitiy is dropping down very much.
Could you chechk the results if you see any deviation, and give me some recomendations how can i do it better?
Answers
-
I would recommend splitting the inlets and outlets into separate boundary sets - for example Inlet_1, Inlet_2 and Outlet_1, Outlet_2.
Do you know the flow rate - or only the pressures? If you know the flow rate (mass flow rate, volume flow rate, or average velocity) that will be a more robust boundary condition.
The mesh still appears to be fairly coarse, particularly from the contours on the 6bar_outlet_velocity image. Do you also have boundary layer meshing? There will be a velocity profile, as the velocity will be zero at the wall, then increase into the interior.
Is the pressure difference really 6bar at the inlet and 0bar at the outlet? You're getting resultant velocity with maximum close to 1000 m/s. If that really is the case, you'll need to run with a variable density model - and probably the compressible solver as Mach 1 is in the 340 m/s range at one atmosphere - which means a lot more mesh refinement and probably transient as well.
Do you expect transonic/supersonic flow here?
1 -
The only demand what I get from our spec is a supply pressure - flow rate chart at the outlet diameters. From this chart the minimum velocity is 461 m/s at 6bar supply pressure. So yeah the velocity definitely needs to be more than Mach 1.
I tried to use boundary layer but only the inlet and outlet tube surface, but it resulted high aspect ratio elements, but didn't see difference between the b.l and without b.l meshing simulations, should I apply boundary layer every boundary surface because the inside volume is not too simple (attached pictures), and also I use 0,5mm element size average.
What density model do you recommend, and where can I find some examples or help for transient simulations? Also I have limitation in calculation power( attached config). Is there any option for a quick consultation?
0 -
Barnabas Retter said:
The only demand what I get from our spec is a supply pressure - flow rate chart at the outlet diameters. From this chart the minimum velocity is 461 m/s at 6bar supply pressure. So yeah the velocity definitely needs to be more than Mach 1.
I tried to use boundary layer but only the inlet and outlet tube surface, but it resulted high aspect ratio elements, but didn't see difference between the b.l and without b.l meshing simulations, should I apply boundary layer every boundary surface because the inside volume is not too simple (attached pictures), and also I use 0,5mm element size average.
What density model do you recommend, and where can I find some examples or help for transient simulations? Also I have limitation in calculation power( attached config). Is there any option for a quick consultation?
This is the relevant tutorial - although it seems to ignore wall effects:
Generally you would use boundary layer meshing to capture near-wall velocity profiles from all the wall boundaries.
You'll also need to use ideal gas to incorporate thermal effects.
My guess is you'll fairly rapidly discover this is not practical to solve on your current hardware. The model size (mesh count) will get quite large, and with transient will take a very long time to solve.
0