Optistruct explicit vs. Radioss
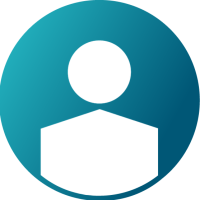
Hello everyone,
I plan to perform helmet crash tests in the next few months to analyse the protective inserts on the inside with expected accelerations of 100-250G. As of version 2020, there seems to be a dynamic explicit option available in Optistruct. Is it comparable to Radioss in terms of precision/fidelity ? Is there any major upside to Radioss that would justify learning the software from scratch or can I stick to Optistruct? I have zero experience with Radioss, it would therefore be pretty time-consuming to get into it. Any opinion is welcome.
Answers
-
OS Explicit was first released in the latest releases, with a few basic features that allows common explicit use cases to be run in general, with the advantage of using the same model as implicit. Please take a look at the documentation in 2020.1 version to see coverage.
Depending on what you need in your model OS Explicit can be enough, including contacts and basic materials.
But if more advanced features are needed, you might need to go to RADIOSS. Also RADIOSS has many years of development ongoing and its performance and scalability are best-in-class. also if you need to include failure models, and more advanced parameters, you might also want to go to RADIOSS.
You can use the internal converters in HM to move from OS model to RADIOSS, but for sure, you will need some extra care when going to explicit.
0 -
Hello Adriano, thanks for the info. I'll probably go with the OS to Radioss converter, then.
0 -
Ingeniorator said:
Hello Adriano, thanks for the info. I'll probably go with the OS to Radioss converter, then.
can you share some pictures of what are your trying to accomplish?
And waht is the hardware and licenses that you have available? RADIOSS scales very well using more CPU core's.
0 -
Adriano Koga_20259 said:
can you share some pictures of what are your trying to accomplish?
And waht is the hardware and licenses that you have available? RADIOSS scales very well using more CPU core's.
The goal is to achieve higher energy absorption (and therefore lower brain/head accelerations) capabilities compared to currently available bicycle helmets using additive manufacturing techniques and novel lattice structures specifically adapted to the use case. We have established a generalized workflow and want to expand its application to other domains. The first use case was a metal bicycle crank arm as proof of concept, where we aimed for maximum stiffness to weight ratio combining the lattice creation tool, Optistruct and Hyperstudy. I have no pictures at my disposal since the project hasn't started yet, but I'm gathering info and I hope my explanation is sufficient for giving a frame of reference.
I have a workstation at my disposal with two 16-core Intel processors at 2.3GHz base clock, 256GB RAM, a Quadro RTX 4000 and 2TB NVME SSDs. We also have access to the complete Hyperworks suite through a research/academic license. If necessary, there might be access to a cluster.
0 -
Ingeniorator said:
The goal is to achieve higher energy absorption (and therefore lower brain/head accelerations) capabilities compared to currently available bicycle helmets using additive manufacturing techniques and novel lattice structures specifically adapted to the use case. We have established a generalized workflow and want to expand its application to other domains. The first use case was a metal bicycle crank arm as proof of concept, where we aimed for maximum stiffness to weight ratio combining the lattice creation tool, Optistruct and Hyperstudy. I have no pictures at my disposal since the project hasn't started yet, but I'm gathering info and I hope my explanation is sufficient for giving a frame of reference.
I have a workstation at my disposal with two 16-core Intel processors at 2.3GHz base clock, 256GB RAM, a Quadro RTX 4000 and 2TB NVME SSDs. We also have access to the complete Hyperworks suite through a research/academic license. If necessary, there might be access to a cluster.
Nice. You have a good machine available and also a cluster, so scalability can work pretty well.
For lattive structures, you might also want to try MultiScale Designer, as you could create these unit lattice cells and calculate their properties and then use them in your model in a much faster approach, with no need of having your full model created using lattices.
This paper used this approach.
0 -
Adriano Koga_20259 said:
Nice. You have a good machine available and also a cluster, so scalability can work pretty well.
For lattive structures, you might also want to try MultiScale Designer, as you could create these unit lattice cells and calculate their properties and then use them in your model in a much faster approach, with no need of having your full model created using lattices.
This paper used this approach.
That is of course a viable approach worth considering. However, I anticipate there to be significant plastic strain and probably self-contact, depending on the lattice structure also twisting and other phenomena. Can this be modeled by a homogenization approach?
0