Meshing surface with many holes
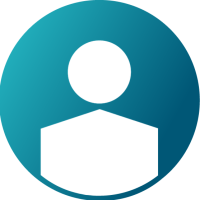
Hi.
I facing problem with meshing surface with many small holes (from stl file - attachment)
Short version:
How to create correct mesh on such stl ?
Long version:
This is a cross section of 3D specimen I will analyse later.
Problem to solve:
Create a mesh with good QI and as small as possible amount of nodes.
Tested ideas:
A. Create a sketch with project or intersect - not possible even to zoom in (very slow software response) due to many geometric elements.
B. Automesh - not acceptable even with small element size.
C. Many others (split, imprint etc, element -> create element)
Problem here is amount of small holes - 720. Not possible to do this manually.
Idea for now.
Create a 16 nodes on each hole edge
Create a line for later each hole split for 4 groups (of 4 nodes each) for good node distribution. I also considering offsetting the edges for proper nodes distribution close to edges but this will increase amount of nodes.
Mesh automatically or semi automatically.
I tried to extract nodes of edge lines and hole edges (it is easy to select all hole edges by once)
Nodes are nicely distributed
But stuck here with meshing.
Tried 2d - spline on nodes
But with node list and Window select always one node can not be selected (why ?)
Creating 2d - spline takes about 30 minutes with unknown result. (mostly failed to create)
Creating splits using lines divides lines not equally:
MK
Answers
-
The STL is very messy, lots of overlapping segments and 0 length segments on edges of holes and part, your best bet may be recreating the surface, or if you have a way to get the geometry in e.g. STEP or Iges it would work better probably.
1 -
Paul thank you for your answer.
I can create better stl - I have very dense data from CT scan.
But the point here is just to preserve edges and mesh rest of it.
I think I go one step further.
I created many lines and used split by line(s):
And use them to mesh 2d with very small 0.05 and then go with node density to 4.
And rebuild the mesh with "only failed"
Effect is below (meshed for only inner part ):
This mesh looks probably good.
But.
How to automatize the process of lines creation ?
How to decrease amount of nodes in other way than Interactive mode during 2d mesh, and criteria editor ?
0 -
Marcin Kneć_21510 said:
Paul thank you for your answer.
I can create better stl - I have very dense data from CT scan.
But the point here is just to preserve edges and mesh rest of it.
I think I go one step further.
I created many lines and used split by line(s):
And use them to mesh 2d with very small 0.05 and then go with node density to 4.
And rebuild the mesh with "only failed"
Effect is below (meshed for only inner part ):
This mesh looks probably good.
But.
How to automatize the process of lines creation ?
How to decrease amount of nodes in other way than Interactive mode during 2d mesh, and criteria editor ?
I'm not sure how you can automate that, it may be scriptable in some way based on nodes at the hole centres? I'm not a scripter, but I have seen similar tasks automated. For the hole mesh size/node count. You should be able to create mesh controls for the free edges separate to the surface.
1 -
Than you all for your answers.
Finally I think mesh is acceptable.
For now the workflow is:
1. Generate section surface of stl (Mshmixer with preserve boundaries)
2. Create surface in HW using 2D -> Spline -> (with 'line' and 'surface only' without keep tangency and without keep lines endpoints .. )
3. Import stl to Inventor (to keep coordinate system location) and create sketch with lines thru the middles of holes (Inventor or any other CAD software has possibility to copy elements in many ways. )
4. Export it as .x_b file
5. Import .x_b file into HW (check proper unit system) and do Geometry Split by lines (about 5 minutes)
6. Create Geometry Extract point (change to nodes) and put number of 4 for all selected lines (lines imported from .x_b file was hidden) - here I got Yellow nodes visible above - with nice distribution.
7. Imprint nodes into the surface created in p.2. (about 5 minutes )
8. Mesh it with proper params and criteria. and Rebuild the mesh
I'm sure there is better (shorter ?) way to obtain a good mesh for this kind of structure (organic CT scan)
But for now steps are repeatable for other types of "holes" specimens.
( I think it may be also possible only with option in Parameter Editor -> Holes 2D -> Circle -> Treatment Washer - I follow the great manual from YT:
https://www.youtube.com/watch?v=l-Vc0VsUw9U - but with no success here).
Conclusions.
Amount of elements is too high and calculation using 3D mesh seem to be to painful for my computer:) but with 2D amount it should be an easy task for non-linear analysis.
MK
1