Contact analysis of a composite laminate
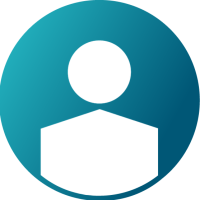
Dear All,
I am trying to simulate a compression test of a composite ring. With NLQS analysis, the solution goes pretty good and somehow accurate, but with this type of analysis, I can't get the CSTRAI and CSTRESS and failure criteria (not supported using NLOUT).
I tried with NLGEOM(implicit) analysis and is working but the results are not the expected ones (Although I can obtain the composite analysis that I wanted). I realize that there are some penetrations in the model that I thought was not there since I choose a z0 option = TOP. It could be possible, that the solver uses the real midsurface of the laminate and so he can detect some penetrations and affecting my simulation? See the attached pictures
Pic 1. Z0 = TOP
<?xml version="1.0" encoding="UTF-8"?>
Pic2. Z0 = real (midsurface of laminate)
<?xml version="1.0" encoding="UTF-8"?>
Not sure if I consider the midsurface of the laminate (and leave the half thickness between the end surface of thickness and the blue plate) the results will not be correct ones.
Thank you for your time
Answers
-
Hi,
Altair Forum User said:It could be possible, that the solver uses the real midsurface of the laminate and so he can detect some penetrations and affecting my simulation? See the attached pictures
Looks like this is what is happening in your case. Can you try to model with RADIOSS where you have control over contacts?
CSTRESS and CSTRAIN will be available through NLOUT from version 2019.
0 -
Dear Prakash,
Thanks for your fast reply.
I loaded the .rad file to double check about this error and is what we were thinking.
I am trying to model it with radioss but I have not that much experience with radioss control cards.
Do you know of any tutorial that can be useful for this application? Is this the correct procedure for considering a future analysis of first ply failure of my composite?
Thank you in advance
0 -
I will check if there are any relavent examples or tutorials available and share the same.
Regarding failure, First ply failure.. it is assumed that laminate is failed with the first ply fails. There are pros and cons for the same. I would suggest you do some research regarding other failure methods like Hashin, etc...
0 -
Dear @Prakash Pagadala
Thanks for your suggestions for my analysis. I have been trying to model it directly from radioss but not completely sure about some aspects.
I have some doubts regarding the material orientation definition. Is not possible to assign a cylindrical system to my elements? Are cylindrical systems supported in radioss for a NLGEOM analysis?
Is there a way to consider the external surface of the thickness of the laminate as the contact surface? When I run the simulation of a compression test, if the midsurface of the laminate is not closely in contact with the compression plates, it is detected as an impact (and is something I would like to avoid). Maybe is an option that I am not activating.
thank you for your help
0 -
Altair Forum User said:
I have some doubts regarding the material orientation definition. Is not possible to assign a cylindrical system to my elements? Are cylindrical systems supported in radioss for a NLGEOM analysis?
You can use cylindrical systems.
Altair Forum User said:Is there a way to consider the external surface of the thickness of the laminate as the contact surface? When I run the simulation of a compression test, if the midsurface of the laminate is not closely in contact with the compression plates, it is detected as an impact (and is something I would like to avoid). Maybe is an option that I am not activating.
I will check if there is a way to do this.
0