FLD or thickness reduction?
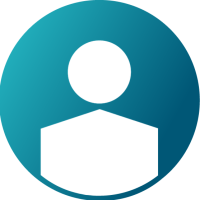
Hi all,
I was running a multi-stage forming simulation on 1mm thick 3003 aluminum sheet. In fact there are three stages on which two adjacent depressions are made. Depressions are ovals about 20mm x 16mm and are 4mm apart. During first stage minimum thickness became about 0.79mm and FLD shows forming process is safe. At second stage minimum thickness will become 0.77 and again FLD is OK, but during third stage at which minimum thickness turns to 0.75, FLD shows large areas of failure. Now I'm confused about the results. Which one is more important? Final sheet thickness or forming limit diagram? On desired part necking is not permissible but 0.75mm thickness is OK. Attached file is a sketch of the part.
I would be very grateful to hear your opinions.
Answers
-
Hi,
You can interpret the results in 2 ways.
1. if you are looking for the results from Manufacturing point of view then consider the FLD plot. If the FLD plot shows most of the component as safe with out any Red regions then you can go ahead for manufacturing.
2. For thickness results refer the % elongation value of the material. this is provided by the Material supplier after performing the tests. If the % thining shown in simulation is lower than the % elonagtion value (ex: Simulation shows 23% thining and the % elongation is 37% then its safe) of the material as provided by the supplier then you can continue else you need to re run the simulation by altering the Blank holding force and the corner and surface filet radius. thinnin gresults are important for further analysis and use cases such as Crash and Impact analysis and modal analysis etc..
Hope this helps.
0 -
Dear kpavan,
Thank you very much for your reply. Let me tell you that I have used tensile test results to define the material in simulation. I mean I have entered stress-strain data to define the material. As for max elongation, in fact it is very marginal in some regions at third forming stage (both material and simulation results are about 25%). In forming stages 1 and 2 I have used blank holder but stage three is a crash forming process. So my question is while thickness reduction from simulation is acceptable, why FLD shows failure in some regions. Are thicknesses from simulation unreal? Or do I have to define some properties of material other than stress-strain curve?
Thanks in advance
0 -
And you made me another question. Can we compare thickness reduction percentage from simulation with max permissible elongation of material? I think the latter one is from one-directional tensile test while the first in resulted from complex loading state. I mean as it is apparent from FLC, permissible major strain can be higher when there is minor strain and it seems it can be even higher than max elongation of the material. Am I right?
0 -
yes you can comapre it with max elongation of the material. The max elongation is generally derived from testing done by the material supplier. if your % thinning is less than the max elongation results from material testing, the component is safe. as mentioned for manufacturing FLD plot is relevant. However for crash analysis %thinning or thickness results are important.
0