How do i know which MAT in optistruct to define my material property?
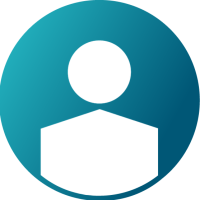
How do i know which MAT is proper in optistruct to define my material property?
My material property that I want to define is G400. The property is following;
And also for core material in sandwich structure such as H100, which MAT in optistruct that I should use to define it
This is my first time question in this community, so if I did something wrong, Sorry.
Best Answer
-
Paphatsorn said:
To Gildas,
I would like to interrupt and ask you for more information. I have to use the G400 and H100 foam in my class project. But the simulation that I have to do are drop weight impact test and low energy impact of sandwich structures which is dynamic simulation not quasi-static. So the program that I have to use is Radioss, couldn’t be Optistruct ,right. and I would like to know which MAT that I need to use to define G400 and H100 foam in Radioss solver how can I classify the material in Radioss. Is Radioss can use and be proper in this kind of simulation because the program that I can is limited in Hyperworks package maybe only 2 Optistruct and radioss.
Paphatsorn
Hello Paphatsorn,
The solver you can use will depend on the type of phenomenon you are trying to simulate/observe.
OptiStruct is not limited to quasi-static and does allow to perform dynamic analysis, either in implicit or explicit. In case of impact and drop-tests, explicit analysis is prefered.
However OptiStruct will not allow you to observe damages on your composite material (at least not with out-of-shelf materials).
So if you want to see the dynamic behavior of your assembly after an impact/drop test without considering material damage/breaking, OptiStruct can be used.
If on the opposite your objective is to consider the composite/sandwich behavior including damage and failure, then indeed you should prefer using Radioss.
If you decide to go to radioss, I would recommand you ask your question about materials to be used on the Radioss forum.
Gildas0
Answers
-
Hello Paphatsorn,
To know what material you need to create, you must first :
- Class your material into 1 of the 3 following category: isotropic, orthotropic, anisotropic
- Identify if the material will be applied to 2D or 3D elements.
Your first material is orthotropic, meaning you cannot caracterise it with 2 values between E,nu,G.
In your case you have E1=E2 but the data do not verify the isotropic condition E=2(1+nu)G.
So you need to define an orthotropic material.
I guess you want to use this material in a laminate for 2D modelling (if not, you are missing some data for 3D modelling).
--> This material must be defined as a MAT8 in OptiStruct.
Your second material is isotropic material (you only get E and G for any direction).
--> For isotropic material, you need to create a MAT1 material in OptiStruct.
Remark : On those classical linear materials, you cannot define a different modulus in tension and in compression. I would recommand you use the smallest value as a common compression/tension modulus.
I would suggest you look at the OptiStruct help manual at pages for MAT1 and MAT8, you will find information helping you identify where to use the different data you have.
Gildas1 -
Gildas GUILLY_21156 said:
Hello Paphatsorn,
To know what material you need to create, you must first :
- Class your material into 1 of the 3 following category: isotropic, orthotropic, anisotropic
- Identify if the material will be applied to 2D or 3D elements.
Your first material is orthotropic, meaning you cannot caracterise it with 2 values between E,nu,G.
In your case you have E1=E2 but the data do not verify the isotropic condition E=2(1+nu)G.
So you need to define an orthotropic material.
I guess you want to use this material in a laminate for 2D modelling (if not, you are missing some data for 3D modelling).
--> This material must be defined as a MAT8 in OptiStruct.
Your second material is isotropic material (you only get E and G for any direction).
--> For isotropic material, you need to create a MAT1 material in OptiStruct.
Remark : On those classical linear materials, you cannot define a different modulus in tension and in compression. I would recommand you use the smallest value as a common compression/tension modulus.
I would suggest you look at the OptiStruct help manual at pages for MAT1 and MAT8, you will find information helping you identify where to use the different data you have.
GildasThank you so much, Sir. I really appreciate it. I use the whole day to find the information about it. And what you guess is right. I am using this material for 2D modelling.
0 -
Gildas GUILLY_21156 said:
Hello Paphatsorn,
To know what material you need to create, you must first :
- Class your material into 1 of the 3 following category: isotropic, orthotropic, anisotropic
- Identify if the material will be applied to 2D or 3D elements.
Your first material is orthotropic, meaning you cannot caracterise it with 2 values between E,nu,G.
In your case you have E1=E2 but the data do not verify the isotropic condition E=2(1+nu)G.
So you need to define an orthotropic material.
I guess you want to use this material in a laminate for 2D modelling (if not, you are missing some data for 3D modelling).
--> This material must be defined as a MAT8 in OptiStruct.
Your second material is isotropic material (you only get E and G for any direction).
--> For isotropic material, you need to create a MAT1 material in OptiStruct.
Remark : On those classical linear materials, you cannot define a different modulus in tension and in compression. I would recommand you use the smallest value as a common compression/tension modulus.
I would suggest you look at the OptiStruct help manual at pages for MAT1 and MAT8, you will find information helping you identify where to use the different data you have.
GildasTo Gildas,
I would like to interrupt and ask you for more information. I have to use the G400 and H100 foam in my class project. But the simulation that I have to do are drop weight impact test and low energy impact of sandwich structures which is dynamic simulation not quasi-static. So the program that I have to use is Radioss, couldn’t be Optistruct ,right. and I would like to know which MAT that I need to use to define G400 and H100 foam in Radioss solver how can I classify the material in Radioss. Is Radioss can use and be proper in this kind of simulation because the program that I can is limited in Hyperworks package maybe only 2 Optistruct and radioss.
Paphatsorn
0 -
Paphatsorn said:
To Gildas,
I would like to interrupt and ask you for more information. I have to use the G400 and H100 foam in my class project. But the simulation that I have to do are drop weight impact test and low energy impact of sandwich structures which is dynamic simulation not quasi-static. So the program that I have to use is Radioss, couldn’t be Optistruct ,right. and I would like to know which MAT that I need to use to define G400 and H100 foam in Radioss solver how can I classify the material in Radioss. Is Radioss can use and be proper in this kind of simulation because the program that I can is limited in Hyperworks package maybe only 2 Optistruct and radioss.
Paphatsorn
Hello Paphatsorn,
The solver you can use will depend on the type of phenomenon you are trying to simulate/observe.
OptiStruct is not limited to quasi-static and does allow to perform dynamic analysis, either in implicit or explicit. In case of impact and drop-tests, explicit analysis is prefered.
However OptiStruct will not allow you to observe damages on your composite material (at least not with out-of-shelf materials).
So if you want to see the dynamic behavior of your assembly after an impact/drop test without considering material damage/breaking, OptiStruct can be used.
If on the opposite your objective is to consider the composite/sandwich behavior including damage and failure, then indeed you should prefer using Radioss.
If you decide to go to radioss, I would recommand you ask your question about materials to be used on the Radioss forum.
Gildas0