What is the difference between layer based and ply based modelling composite in Radioss?
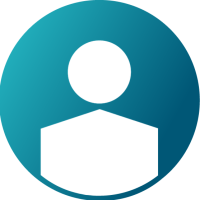
I am confused and cannot get the answer from manual about what is the difference between layer based and ply based modelling composite, what is proper for my work. I am doing a simulation about drop weight impact test with composite plate (G400) which have 14 plies and each ply have material orientation as following. [0/90]6 and continue with [45/-45]8
Thank you in advance.
Best Answer
-
Hi, the various composite property definitions available increase in complexity and functionality through Type 10 - Type 11 layer based to Type 17/19, Type 51/19 ply based. What you need to use depends on how complex your part is (though there can be other benefits to using the ply based modeling too, even if you don't 'need' to).
From your description of your plate model, Type 10 (SH_COMP) or Type 11 (SH_SANDW) layer based definitions should be sufficient.
Basically, If all of your plies use the exact same material (except for orientation), are the same thickness and cover the whole of a component, then SH_COMP (Type 10) is the easiest one to define, you can tell it your total laminate thickness, number of plies and their orientations and you are done.
SH_SANDW (Type 11) additionally to the above, allows you to define different thicknesses for the different plies and also, the material definiton for the plies moves to the PROP card, this allows you to use different variations of a given material law (all have to be the same 'type' e.g. LAW25, but you could use different LAW25 definitions in different plies).
Both Type10 and Type11 are 'layer based', effectively, this means they are defined in a similar way to a metallic component, you have a PART, that your component belongs to, that references a Property and Material(s), the part is uniform in thickness and layup.
The key difference between 'layer based' and 'ply based' is that with 'ply based', the set up is more like reality if you have 1 or more plies that are not 'full body' i.e. they don't cover the whole part.
In ply based modelling, the laminate stack (all the plies in order, with their materials, orientations, and thicknesses) is defined separately to the shape of those plies. In cases where ply shapes vary, this allows the user to define a single /PART with composite properties for the component, even if the plies do not all cover the whole component (and thickness varies across it) rather than having to break the component into multiple parts, each with a different ply combination.
You can think of Type 17 and 19 in combination as being the 'ply based' version of Type 11, the limitations on material commonality etc are the same, it is just adding the ability to define ply shapes independently of the PART card.
With Type 51 and 19, the set up is much the same as with Type 17 but you can further define number of integration points per ply (all above have 1 per ply), and you can mix material laws (e.g. use LAW 25 and LAW 36 in a laminate).
For any given laminate, if it is able to be described using Type10, then all the other set ups with increased complexity, should give the same results as type 10 if the definition is done correctly.
Hope this helps,
Paul
2
Answers
-
Hi, the various composite property definitions available increase in complexity and functionality through Type 10 - Type 11 layer based to Type 17/19, Type 51/19 ply based. What you need to use depends on how complex your part is (though there can be other benefits to using the ply based modeling too, even if you don't 'need' to).
From your description of your plate model, Type 10 (SH_COMP) or Type 11 (SH_SANDW) layer based definitions should be sufficient.
Basically, If all of your plies use the exact same material (except for orientation), are the same thickness and cover the whole of a component, then SH_COMP (Type 10) is the easiest one to define, you can tell it your total laminate thickness, number of plies and their orientations and you are done.
SH_SANDW (Type 11) additionally to the above, allows you to define different thicknesses for the different plies and also, the material definiton for the plies moves to the PROP card, this allows you to use different variations of a given material law (all have to be the same 'type' e.g. LAW25, but you could use different LAW25 definitions in different plies).
Both Type10 and Type11 are 'layer based', effectively, this means they are defined in a similar way to a metallic component, you have a PART, that your component belongs to, that references a Property and Material(s), the part is uniform in thickness and layup.
The key difference between 'layer based' and 'ply based' is that with 'ply based', the set up is more like reality if you have 1 or more plies that are not 'full body' i.e. they don't cover the whole part.
In ply based modelling, the laminate stack (all the plies in order, with their materials, orientations, and thicknesses) is defined separately to the shape of those plies. In cases where ply shapes vary, this allows the user to define a single /PART with composite properties for the component, even if the plies do not all cover the whole component (and thickness varies across it) rather than having to break the component into multiple parts, each with a different ply combination.
You can think of Type 17 and 19 in combination as being the 'ply based' version of Type 11, the limitations on material commonality etc are the same, it is just adding the ability to define ply shapes independently of the PART card.
With Type 51 and 19, the set up is much the same as with Type 17 but you can further define number of integration points per ply (all above have 1 per ply), and you can mix material laws (e.g. use LAW 25 and LAW 36 in a laminate).
For any given laminate, if it is able to be described using Type10, then all the other set ups with increased complexity, should give the same results as type 10 if the definition is done correctly.
Hope this helps,
Paul
2 -
Thank you so much. This one really help me.
0 -
No Problem, thanks. Have a great holidays.
1