Defining Different Stress Constraints on Multiple Loadcase Topology Optimization
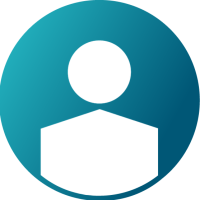
Hi everyone.. I want to perform topology optimization on a simple bracket for multiple loadcases. And I have different stress limit for each load case.. How Can I set up the optimization model for this. I tried minimize the weighted complience response by using volume fraction response with stress constraint.. But I had to determine general stress constraint for the setup.. How can I determine the stress constraint separately and minimize the mass ? Thank you.
Best Answer
-
Hi @mecjos
The general stress constraint inside topology panel is used for general purpose optimization, where a global target value is assigned to all elements in your model and all loadcases, and some averaging is applied so that the number of stress constraints is not too large.
In order to specify stress constraints you will need to create stress responses (DRESP1) and constraint them, just like the tutorial (although this is a size optimization, the process is the same).
Have in mind that with this approach you will be able to use a constraint for each loadstep and choose a particular region for calculating stress values during optimization.
This uses a more modern approach, calculating a stress norm.
It might take longer to solve your problem, depending on the number of elements/properties chosen.
OS-T: 4010 Size Optimization of a Welded Bracket
In this tutorial you will perform a size optimization on a welded bracket modeled with shell elements.
1
Answers
-
Hi @mecjos
The general stress constraint inside topology panel is used for general purpose optimization, where a global target value is assigned to all elements in your model and all loadcases, and some averaging is applied so that the number of stress constraints is not too large.
In order to specify stress constraints you will need to create stress responses (DRESP1) and constraint them, just like the tutorial (although this is a size optimization, the process is the same).
Have in mind that with this approach you will be able to use a constraint for each loadstep and choose a particular region for calculating stress values during optimization.
This uses a more modern approach, calculating a stress norm.
It might take longer to solve your problem, depending on the number of elements/properties chosen.
OS-T: 4010 Size Optimization of a Welded Bracket
In this tutorial you will perform a size optimization on a welded bracket modeled with shell elements.
1