How to be sure that the optimized composite layup drap well on the part
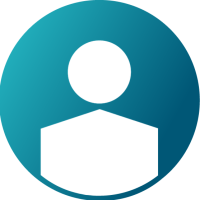
Hi
My question is that when i finally get the optimized results from optistruct for a composite laminate, How can i make sure that the physical ply draping on the manufactured part will be fine as well?
Is there a tool that can take care of draping so that the final ply outcome take into account that as well and thus the part can be manufactured without wondering if draping issues occurred during product manufacturing?
Thanks
Answers
-
Hi,
there are two options to check layup draping:
-Use the Drape Estimator to generate, directly into HyperMesh, draping angles and thickness variations resulting from the manufacturing process of fibers associated with plies in a composite laminate. You can use the drape data generated by this tool, based on inverse mapping, to improve the accuracy of parts modeled with composite materials. The Drape Estimator is available in the LS-DYNA, Nastran, OptiStruct and RADIOSS user profiles.
Drape Estimator - Altair University
-perform composite forming simulation with Hypererform (see HF-3090: Composite Forming Simulation)
0 -
Thanks Ivan for the info, I have seen the video. From the video it seems like that once the layups are optimized (for my problem), we can run the Drape Estimator to see the changes in thickness and orientations. But then does it means that the ply orientations will change as well? like in above video, both 0 and 90 degree ply orientations changed after running draping estimator. So can one simply export this model and feed to machine where the composite will be manufactured with modified orientations coming from drape estimator?
I want to know how does this draping info feed to the machine ?
Thanks
0 -
Have you done optimization in three phases? Freesize ,size and ply stacking optimization
0 -
Drape Estimator will modify element level orientations and thicknesses with Drape tables for each ply. Ply level orientations and thicknesses will not change.
Drape estimator simulates the effects of manufacturing process. Therefore I would use it before optimization.
0 -
Altair Forum User said:
Have you done optimization in three phases? Freesize ,size and ply stacking optimization
I am not sure when to use Drap estimator? before optimization or after?
0 -
Altair Forum User said:
Drape Estimator will modify element level orientations and thicknesses with Drape tables for each ply. Ply level orientations and thicknesses will not change.
Drape estimator simulates the effects of manufacturing process. Therefore I would use it before optimization.
So if i use Drape Estimator first and than optimization would the final optimized part comply with the manufacturing and take into account the draping effects?
0 -
Manufacturing compliance can be checked by reviewing orientation and thickness change output by the tool. Draping effects will be included during optimization.
0 -
Thanks, I will do some examples and return back if there are more questions.
0