DYREL CARD and MODEL VALIDATION
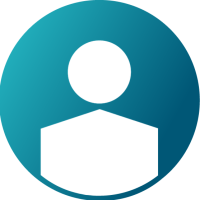
Good evening,
I am making a Formula SAE impact attenuator simulation. It is make with carbon fiber prepreg. For the model we are using material LAW 25 (CRASURV) and property 17 (stack).
To calibrate material parameters and boundary conditions we are simulating an small plate. During the impact we obserb a shock wave that brakes the plate wherever and not row by row.
We are trying to include something to damp or relax the material avoiding the shock wave. However, when we use the control cad /DYREL the model stops and kinectic energy evolve to cero. Parameters used on /DYREL are relaxation factor = 1 (default) and period (6e-5). We obtain period following indications of this text (https://insider.altairhyperworks.com/wp-content/uploads/2012/01/DynamicRelaxation_1201.docx). Where is our mistake? What can we try to solve it?
Moreover, we create a model to compare with a test made in our center 2 years ago. Real part have a maximum of 10 plies. To obtain the same results on our hypermesh model we have to use more than 70 plies. We have asked Altair Spain and they don't see any mistake on the model (Attached you can find the model) and recomend us to ask on the forum. Real test results were positive and the impact attenuator resist impact and there was 16 cm without brake. On the model the impact totaly brakes and can't stop the 300 Kg rigid body used to simulate the car.
Thank you for your help
Answers
-
Hi,
1. Deformation modes can be influenced by other parameters such as shell property. Dynamic relaxation is used to obtain a static result, so IMHO it is not appropriate to artificially dampen impact simulation.
2. The same problem was already opened, unfortunately without a solution:
https://community.altair.com/community?id=community_question&sys_id=7a868c3a1b2bd0908017dc61ec4bcb57One of the reasons could be that in the model you have shared, all the plies have the same orientation leading to increased crack propagation. Review/edit ply orientation in Aerospace user profile using Aerospace>display>orientation review>ply directions.
Attached is the modified model, where contacts, properties and plies were edited, however the attenuator still fails to absorb all of kinetic energy.
0