Modelling Rigid bodies in Optistruct
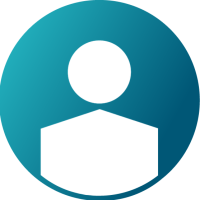
Hi,
I know this question has been asked before, but there is still something I think I am doing incorrectly.
In Optistruct I have a deformable metal sheet that moves through forming rolls, which I want to model as rigid bodies (see picture attached).
Right now I do it the following way: I import the outer contour of the forming roll, mesh it (creating component 1), create an RBE2 (as a new component 2) and constrain every node of the forming roll. As an independent node for the RBE2, I choose the node in the middle of the forming roll, which I constrain with an spc in every direction.
The model still wants me to assign a material and property to the elements I created during the meshing (component 1). I give it a material with an extremely high E-modul, although that shouldn´t matter with RBE2 in place. I use a shell property with thickness 1e-6, because I already have the outer contour and don´t want any thickness on top.
This does work, but it feels wrong. Especially during post processing, there are still stresses calculated at dependent nodes of the rbe2 or at least it looks like it, which would increase computational time by a lot (see picture 2). Anyone knows what I did wrong? Any help to model this more efficiently is appreciated. Thank you in advance.
Best Answer
-
You should use RBODY rather than RBE2, and use 'physical' properties for thickness and material (you should get better contact behaviour then too), if you need to have no 'thickness' on the RBODY part , you can set this in the contact with CLEARANCE, see the 3 point bend example in help 3 point bend with RBODY
1
Answers
-
You should use RBODY rather than RBE2, and use 'physical' properties for thickness and material (you should get better contact behaviour then too), if you need to have no 'thickness' on the RBODY part , you can set this in the contact with CLEARANCE, see the 3 point bend example in help 3 point bend with RBODY
1 -
Thank you for your help. With RBODY it works, so there are no stresses calculated for the forming rolls besides the stresses at the reference node. The simulation time is significantly reduced due to this.
Regarding contact, I will try out your suggestions. Right now, I am manually defining SRCHDIS to compensate for the small shell thickness I defined.
0