Contact Energy too high
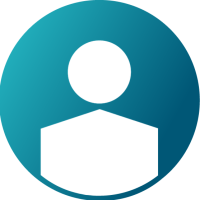
Hello all,
I am trying to run a pole impact simulation for a side sill. The following are the plots i got for the diff global variables. However, the contact energy seems to be too high, and the kinetic energy even after impact has a very high value. What could be the reason for this? I have used TYPE 7 contact for the self contact of the sill, and also for the contact between the rigid pole and the side sill.
Answers
-
Hi,
this is odd and it hard to comment without seeing the model.
The following contact settings are recommended for type 7:
Istf=4
Igap=2
Fscale_Gap=0.8
INACTI=6
Gap_min=1mm
Fric = 0.1
Iform=2
If you aren't able to share the model, check again this topic:
https://community.altair.com/community?id=community_question&sys_id=3966ccf61b2bd0908017dc61ec4bcbecTry to set up pole contact with rigid wall>cylinder and self-contact only on the side sill.
0 -
Hi Ivan,
I managed to figure out why the contact energy was that high. It was a modeling mistake. However, the Kinetic energy after impact still seems to be very high. I have used the suggested parameters for the contact ( self contact ). My component does not seem to absorb much energy. What could be the error? Unfortunately , I will not be able to share the model.
0 -
Hi,
If your part should be absorbing more energy then I would suggest you check material input parameters or thickness for mistakes. Is the model mass correct? Is the initial energy in the system correct?
Also, run the model checks in HyperMesh or HyperCrash to look for errors.
You can plot other energies, such as global contact, hourglass, TTE, total transnational energy, external work.
If you add all your parts to the time history output (/TH/PART) you can check each parts energy to look for strange results.
How are you modeling your pole? Using /RWALL or with a mesh and /RBODY?
Thanks,
Andy
0 -
HI Andy,
I have used MAT/LAW2. Since it is as side impact analysis, I presume the kinetic energy would come down after impact. I have plotted other energies, all of it are negligible or zero. I am using a meshed cylinder with /RBODY. I have also tried it with the /RWALL option, and the values seem to be the same. What are the friction parameters that are recommended? And also how do I define the inertia? Just to clarify, it is a single component test.
Thanks,
Vishruth
0 -
Hi Vishruth,
The initial kinetic energy has to get absorbed by the material deforming plastically. In your LAW2 material are your yield stress and plastic hardening parameters correct?
You can define inertia of the pole in the /RBODY. By default, the /RBODY uses the inertia of the slave nodes of the mesh that are part of the /RBODY so it is important to specify a material and thickness to the mesh. For /RBODY any mass and inertia values are added to the values from the mesh slave nodes. Or if using /RWALL you can specify the mass directly.
Thanks,
Andy
0