Extracting correct Reaction Force in bolts/rivets
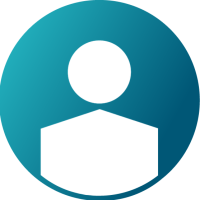
I am trying to estimate the Force it would take to break a rivet. I am applying a displacement load and am measuring the reaction force at a cross-section. However, I am getting 14.2 kN Reaction force which is very high.
The Rivet is made of steel (Tensile failure stress = 420 MPa) and it has a cross-section area = 4.58mm^2.
So, the max shear force to break the Rivet should be less than 420e6*4.58e-6 = 1.9 kN. This Rivet in reality should break under 1kN load.
I am attaching this simple example with this post. I am not sure what exactly is wrong with my setup; Or what should be the correct setup to estimate the force it would take to break the rivet.
Can you help and/or provide guidance to resolve this issue?
Answers
-
There are quite a few non physical constraints in the model, bolt is RBE3 connected at outer faces, upper is constrained to only move in X, I guess you are only looking at beam behaviour here really? Your force at the section is largely composed of tensile stiffness of the beam as it is not constrained rotationally via the RBE3 it rotates and is loaded in tension, if you couple the rotational DOF of the RBE3, then the beam is in shear and the peak force in the section is 1068N (the beam isn't eroded as plastic strain limit is not reached).
Are
0 -
Thank you Paul for the response.
How do I couple the rotational DOF of the RBE3 with the beam element? I have connected the Beam element end points to the dependent node of RBE3. Can you share the configuration?
0 -
Ashmita Tiwari said:
Thank you Paul for the response.
How do I couple the rotational DOF of the RBE3 with the beam element? I have connected the Beam element end points to the dependent node of RBE3. Can you share the configuration?
For my quick test I just set the rotations as coupled for the independent nodes, but it was just to try and load the beam in shear, I wasn't suggesting it as the solution to your problem exactly! I was Just pointing out that there are a lot of unusual boundary conditions and modelling choices in your model causing the bolt to be loaded in tension more than shear and leading to the odd deformation. This was just a quick way to load it in shear instead to show that if you did so you would get more realistic results.
It would be better to build the model a different way to load the bolt in shear instead (break the bolt into separate sections and connect it along it's length rather than just at the ends, or model the bolt as solid for example)
1d may be an over simplification. RBE3 are commonly used in linear static modelling in holes to prevent rigidising the hole and to load only 1 side. But they are less frequently used in Explicit modelling. But here, Sticking to 1d bolts, I attached a small example removing the BCS on everything except the Rbodies, adding contact between the blocks, reverting the RBE3 to uncoupled for rotations at the dependent nodes and using 3 integrated beams for the bolt instead, it gives similar results to the rough test, but now it actually fails too. It is a better way of doing it I think (I converted the model back to kg mm ms and v 2018 for you)
0