HyperMorph optimization runs only for one iteration
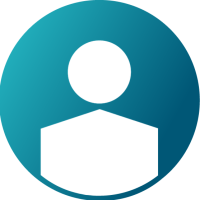
Hello,
I’ve recently been trying to learn topology optimization using HyperMorph and stumbled across the following static analysis problem. I have a simple, 2D fitting with applied loads and constrains. I would like to minimize mass by manipulating the inner and outer radii, as well as four linear dimensions while still not exceeding 600 Von Mises MPa. The solver runs for only one iteration, then stops with a comment that it has reached feasible design. The design however is nowhere near perfect – the maximum Von Mises stresses come to ~200 MPa. I’ve tried manipulating the bounds, checking for collapsed elements but thus far everything was in vain.
Below I’ve attached my model. I’d be really grateful for some hints and suggestions. Thank you.