Why is the displacement of my model is extremely high?
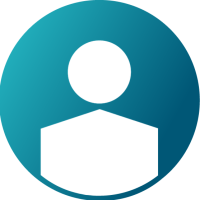
I´m applying an acceleration of 5 g on my model, which is made out of very thin CFRP layers. I´ve created middle surfaces of my model and then meshed it in 2D. The final displacement Optistruct shows me, are around 1,6E+10 mm, which is totally unrealistic. Even when I create thicker layers, the results change only incrementaly and the displacement even gets higher?! When I do the same calculations on a simplet plate, the results are also high (due to the very thin plate), but are roughly correct.
Where could be my error? Or is my model just not correct?
Answers
-
are you sure your model has the correct bounday conditions? Usually these high displacements come from models unconstrained.
Do you mind running a modal analysis, using the same SPC to check if your model is not free to move?
Also for composites you need to check proper material orientation (2D>>composites>>material orientation).
Also check if your laminate is balanced and symmetric, as if not, some out of plane effects might arise.
0 -
Are you sure that all your parts and units are correctly scaled, i.e. that you follow the same unit system like kg/mm/s? Have you checked other element orders and types?
0 -
@Adriano A. Koga I think the conditions are correct. For my SPC I`m using the edge of a ring on the bottom of the model. But here could be my error somewhere...
I did the modal analysis and it works. The model is shown below with the displacement. When I click on the "deformed" button, the blue ring (which is my SPC) stays at the same point, and the rest goes up and down. Maybe the connection between the ring and the rest of the model is incorrect?
My laminate is in 0°, 60°, -60°, -60°, 60°, 0° layers.
What do I have to look for under the material orientation?
0 -
@Ingeniorator I follow the unit system ton/mm/s as I saw it in a different post. Like in the 10th line in here.
0 -
Manuel_21421 said:
@Adriano A. Koga I think the conditions are correct. For my SPC I`m using the edge of a ring on the bottom of the model. But here could be my error somewhere...
I did the modal analysis and it works. The model is shown below with the displacement. When I click on the "deformed" button, the blue ring (which is my SPC) stays at the same point, and the rest goes up and down. Maybe the connection between the ring and the rest of the model is incorrect?
My laminate is in 0°, 60°, -60°, -60°, 60°, 0° layers.
What do I have to look for under the material orientation?
probably your connection is not properly set, as you mentioned.
Is the mesh connected? Or do you have a FREEZE/TIE contact in the junction?
0