crash box with imposed displacement - Why do I have a big first peak force?
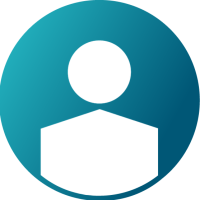
Hey Altair-community,
I am really new to Radioss and crash simulation, so there are thousands of questions but mainly the tutorials and the help of the manuals are greate. There is one question which I couldn't solve for quite some time and I did a lot of try and error simulations. Maybe you can help me!
I computed a crashbox simulation and wanted to validate my model with a given paper (https://ms.copernicus.org/articles/10/133/2019/ from where I got this picture:
I simulated the crash box of the hexagon model and actually got quite good results but have some issues with the first peak force. I thought about the material parameters which I set but I don't have more informations than there is written and ther could be some buckling errors. Otherwise I did some experiments with the contact surfaces and the BC's because I thought that there is my error. The simulations have nearly all the same results (self contact throught Type7 and different other contacts like Type7, Type10 or Type2 because the model has a hard contact -see second picture). What might be the best contact and where could be a problem?
I will add one of my simulations (which is the third graph). Eventually you got some suggestions.
Thanks a lot in advance and kind regards
Leo
Answers
-
I took a quick look at the copernicus paper. I think the principal difference may be that they are referring to 'quasi-static' tests (at 5mm/min) whereas you are impacting the crash box at 4m/s (48000x faster) so your model is an impact rather than a quasi static crush!. In their description, the box is actually 'attached' to the plates, so you could do that here too (add the end nodes to the RBODY rather than using contact). EDIT: ok, checked, yours is actually at 0.4m/s, not 4m/s, it is still 4800x too fast though
Also, I'm not sure the a,b,n you have are correct? From the paper values for Yield, UTS and EPS_UTS I think you should have a= 0.10399 b=0 .7934883876425 n=0.3689174242587, I modified the mat to that, and it actually makes the initial spike higher... and my curves below are based on that, but it is independent of the point about the loading speed.
You can apply your displacement as a sin curve so effectively giving initial velocity of 0, rather than 'hitting' the box at 0.4 m/s, in Radioss 2022 you can do this simply by setting /FUNCT_SMOOTH, if in an older version (which it looks like you are?) then you would have to define the curve manually.
Doing this alone, I get an initial peak reduced by over 50%, even though the average velocity is still 0.4m/s (4800 times 'too fast')
Hope this helps,
Paul
1 -
Hey Paul,
thanks for your fast answer and sorry for the belated reply. First of all its Radioss 2019.
For the material, I chose the parameters taken because I thought that they did not write the engineering stresses and I changed them from true stresses to engineering stresses because they did a tensile test for the material. That lowered the curve, but maybe the engineering stresses are in the paper as you thought at first sight. I'm going to change that.
"In their description, the box is actually 'attached' to the plates, so you could do that here too (add the end nodes to the RBODY rather than using contact)"
This leads to another question. I want to calculate the force-displacement curve, as shown above. And I have always calculated the force using contact or rigid wall. Is it possible to calculate it via RBODY as you wrote, and if so, how? Because I can't select the rigid as a set or as a node.
Smoothen the curve was a really good advise and it was possible to lower the peak for me too.
Then the last and for me the most important question about the crushing speed. The paper says:
"It was found that a global mesh size of 1 mm and an analysis time of 0.2 s yielded reasonable results."
So I set the simulation time to 200 ms and as a result the simulation is 4800x too fast
. But how can I change this? I'm confused by the fact that if I increase the time for the real time simulation, the total time of the simulation increases by a lot. I think there is something that I don't have in mind and belongs to the quasi static analysis.
Best regards
Leo
0 -
And there are some other questions I would like to ask concerning build up structures and connect them with contacts or converting models from Optistruct to Radioss. Can I ask them right here or should I open a new thread?
0 -
Leopold Bergk said:
Hey Paul,
thanks for your fast answer and sorry for the belated reply. First of all its Radioss 2019.
For the material, I chose the parameters taken because I thought that they did not write the engineering stresses and I changed them from true stresses to engineering stresses because they did a tensile test for the material. That lowered the curve, but maybe the engineering stresses are in the paper as you thought at first sight. I'm going to change that.
"In their description, the box is actually 'attached' to the plates, so you could do that here too (add the end nodes to the RBODY rather than using contact)"
This leads to another question. I want to calculate the force-displacement curve, as shown above. And I have always calculated the force using contact or rigid wall. Is it possible to calculate it via RBODY as you wrote, and if so, how? Because I can't select the rigid as a set or as a node.
Smoothen the curve was a really good advise and it was possible to lower the peak for me too.
Then the last and for me the most important question about the crushing speed. The paper says:
"It was found that a global mesh size of 1 mm and an analysis time of 0.2 s yielded reasonable results."
So I set the simulation time to 200 ms and as a result the simulation is 4800x too fast
. But how can I change this? I'm confused by the fact that if I increase the time for the real time simulation, the total time of the simulation increases by a lot. I think there is something that I don't have in mind and belongs to the quasi static analysis.
Best regards
Leo
For RBODY output, you can request /TH/RBODY output and it reports forces across the RBODY
this plot is of RBODY force(s) (top and bottom, the 'NULL' values) vs contact force for one of your runs:
Regarding the speed of loading, the main issue was the velocity at initial impact causing a shock that results in high initial peak force, (which the smoothing is resolving). So long as the kinematic effects are low (run remains quasi static), you can get away with running the job much faster than the physical test. I experimented with slowing the run overall down when you posted originally, and it didn't much further reduce the forces, so I think the 0.2s is 'OK' overall, you just need to avoid 'impacting' the crush tube at the high velocity initially.
Since in explicit analysis your timestep size is limited by element size and material properties, If you increase the 'real time' of the simulation, all else being equal, the simulation time will increase by the same amount, so running for 1s will take 5x as long as 200ms (since you will need to solve 5x as many timesteps). You can change this by increasing the timestep too, but only by adding artificial mass. This may also be 'acceptable' if the run remains quasi static.
1 -
Leopold Bergk said:
And there are some other questions I would like to ask concerning build up structures and connect them with contacts or converting models from Optistruct to Radioss. Can I ask them right here or should I open a new thread?
Probably better to ask a new question so it is well documented in the forum
0 -
Paul Sharp_21301 said:
For RBODY output, you can request /TH/RBODY output and it reports forces across the RBODY
this plot is of RBODY force(s) (top and bottom, the 'NULL' values) vs contact force for one of your runs:
Regarding the speed of loading, the main issue was the velocity at initial impact causing a shock that results in high initial peak force, (which the smoothing is resolving). So long as the kinematic effects are low (run remains quasi static), you can get away with running the job much faster than the physical test. I experimented with slowing the run overall down when you posted originally, and it didn't much further reduce the forces, so I think the 0.2s is 'OK' overall, you just need to avoid 'impacting' the crush tube at the high velocity initially.
Since in explicit analysis your timestep size is limited by element size and material properties, If you increase the 'real time' of the simulation, all else being equal, the simulation time will increase by the same amount, so running for 1s will take 5x as long as 200ms (since you will need to solve 5x as many timesteps). You can change this by increasing the timestep too, but only by adding artificial mass. This may also be 'acceptable' if the run remains quasi static.
Hey Paul,
"add the end nodes to the RBODY rather than using contac". So I did it with 1-D Rigid but the problem is that the structure overgoes the RBODY Element. I added a rigid wall. But as I ad a rigid wall I could also use the contact as I did. Is there a better way to just take the RBODY?
Right now I did it like this don't work as it passes by (picture).
0