Temperature residual convergence issues in helical liquid cooling Jacket
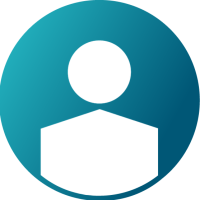
Hello experts,
I'm trying to model liquid cooling of PMSM motor. My energy residual goes flat around 0.02 after 5 to10 iterations and nothing changes afterwards for 100 time steps. Same trend could be seen is surface outputs (temperature) which gets stabilizes after 10 iterations.
I tried refining the mesh based on temperature nodal residual output (Hyperview), but still no improvement in residuals.
Geometry:
Mesh:
Nodal Residual Output:
Answers
-
You'll want to look at contours of the absolute value of the temperature residuals - then see where those are highest. (The residuals can be either + or - , so you want to look at absolute value.)
You may try refining the outer volume a bit and/or adding boundary layers to the gray volume as well - from the boundary between blue and gray.
Can you attach the Log file? Sometimes the high aspect ratio geometry - long path from inlet to outlet - can lead to an overly stiff matrix, and slow the information propagation.
0 -
acupro_21778 said:
You'll want to look at contours of the absolute value of the temperature residuals - then see where those are highest. (The residuals can be either + or - , so you want to look at absolute value.)
You may try refining the outer volume a bit and/or adding boundary layers to the gray volume as well - from the boundary between blue and gray.
Can you attach the Log file? Sometimes the high aspect ratio geometry - long path from inlet to outlet - can lead to an overly stiff matrix, and slow the information propagation.
Hi, thanks for your response.
Here is the contour.
I'll aim for better aspect ratios and apply boundary layer to the solid if that is what you meant. I have attached the log files for your reference. Thanks again.0 -
Jagan_21383 said:
Hi, thanks for your response.
Here is the contour.
I'll aim for better aspect ratios and apply boundary layer to the solid if that is what you meant. I have attached the log files for your reference. Thanks again.I referred to aspect ratio in relation to the geometry itself - not the individual mesh elements. The flow path has a high aspect ratio - a very long tube with a small 'diameter'. This is also apparent in the Log files where the CGP Iterations in the flow and temperature solvers are consistently hitting the default maximum of 1000. If you go into the Physics/Setup panel from the Flow ribbon, then Advanced Controls, you can try enabling 'Modify Flow Stagger Settings' and 'Modify Temperature Stagger Settings' and increase the Maximum Linear Solver Iterations to 3000 or even 5000. This will allow more passes each time step to improve the inner convergence of the equations - to overcome the high aspect ratio flow path. Typically you'll see more iterations in the first several time steps, thus longer runtime also, but then the iterations should reduce over time.
With the absolute value of the residuals - you want to focus on the larger values to see where those occur - paying attention to both the solid and fluid volumes. You could create isosurfaces of the absolute value and focus on the higher values for that isosurface.
The reverse flow at the outlet could also be causing issues. You may see improved performance by extending a 'tube' or 'duct' from the current outlet - moving the eventual outlet farther away from that bend just before the current outlet. That bend will cause some vortex structures which apparently pass through the current outlet. Moving the outlet farther away will keep the vortex within the domain rather than passing through the outlet.
1 -
acupro_21778 said:
I referred to aspect ratio in relation to the geometry itself - not the individual mesh elements. The flow path has a high aspect ratio - a very long tube with a small 'diameter'. This is also apparent in the Log files where the CGP Iterations in the flow and temperature solvers are consistently hitting the default maximum of 1000. If you go into the Physics/Setup panel from the Flow ribbon, then Advanced Controls, you can try enabling 'Modify Flow Stagger Settings' and 'Modify Temperature Stagger Settings' and increase the Maximum Linear Solver Iterations to 3000 or even 5000. This will allow more passes each time step to improve the inner convergence of the equations - to overcome the high aspect ratio flow path. Typically you'll see more iterations in the first several time steps, thus longer runtime also, but then the iterations should reduce over time.
With the absolute value of the residuals - you want to focus on the larger values to see where those occur - paying attention to both the solid and fluid volumes. You could create isosurfaces of the absolute value and focus on the higher values for that isosurface.
The reverse flow at the outlet could also be causing issues. You may see improved performance by extending a 'tube' or 'duct' from the current outlet - moving the eventual outlet farther away from that bend just before the current outlet. That bend will cause some vortex structures which apparently pass through the current outlet. Moving the outlet farther away will keep the vortex within the domain rather than passing through the outlet.
Understood, Thank you for your suggestions. I'll incorporate them.
Also the no of Kyrlov vectors for temperature stagger is 40 by default. What does stagger iterations mean, non linear?0 -
Jagan_21383 said:
Understood, Thank you for your suggestions. I'll incorporate them.
Also the no of Kyrlov vectors for temperature stagger is 40 by default. What does stagger iterations mean, non linear?When doing a transient run, we want a converged solution every time step. In order to get that we allow for multiple passes through the solved equations (or staggers) - and that is typically referred to as stagger iterations. In steady-state, we don't need convergence every time step, so we just do one stagger iteration each time step. Either way there are multiple linear solver iterations for each equation/stagger solved.
Here is a snippet from a random steady-state Log file - one pass through the staggers/equations each time step - also for a long/skinny overall flow path. Increasing the max-linear-solver-iterations mentioned earlier allows for more CGP and/or GMRES linear solver iterations. In this example - the CGP iterations in the Flow stagger indicates 1625 - instead of the default maximum of 1000.
acuSolve-impi: Time-Step= 20 ; timeInc= 1.000000e+10 ; time= 1.900000e+11
acuSolve-impi: Flow stagger "flow": FORM-LHS
acuSolve-impi: pressure res ratio = 7.265698e-05
acuSolve-impi: velocity res ratio = 9.289273e-06
acuSolve-impi: CGP No iterations = 1625
acuSolve-impi: CGP 0/1/n norms = 8.327762e-07 4.419242e-06 8.304217e-09
acuSolve-impi: CGP Iter. CPU/Elapse = 3.245160e+03 2.544308e+01
acuSolve-impi: GMRES No iterations = 356 (8.90)
acuSolve-impi: GMRES 0/1/n norms = 5.321452e-06 1.079823e-05 5.321020e-07
acuSolve-impi: GMRES Iter. CPU/Elapse = 2.219330e+03 1.739899e+01
acuSolve-impi: pressure sol ratio = 2.291379e-02
acuSolve-impi: velocity sol ratio = 3.261731e-02
acuSolve-impi: Turbulence stagger "turbulence": FORM-LHS
acuSolve-impi: eddy-visc. res ratio = 1.189178e-02
acuSolve-impi: GMRES No iterations = 130 (1.30)
acuSolve-impi: GMRES 0/1/n norms = 5.579083e-11 5.579083e-11 5.557569e-13
acuSolve-impi: GMRES Iter. CPU/Elapse = 2.593200e+02 2.033156e+00
acuSolve-impi: eddy-visc. sol ratio = 4.334661e-02
acuSolve-impi: Temperature stagger "temperature": FORM-LHS
acuSolve-impi: temperature res ratio = 1.293745e-04
acuSolve-impi: GMRES No iterations = 916 (9.16)
acuSolve-impi: GMRES 0/1/n norms = 1.584139e-06 1.584139e-06 1.580521e-09
acuSolve-impi: GMRES Iter. CPU/Elapse = 2.086150e+03 1.635673e+01
acuSolve-impi: temperature sol ratio = 4.797981e-02
acuSolve-impi: CFL timeInc = 1.158811e-07
acuSolve-impi: Step CPU/Elapse time = 8.521640e+03 6.680681e+01 Sec0 -
acupro_21778 said:
I referred to aspect ratio in relation to the geometry itself - not the individual mesh elements. The flow path has a high aspect ratio - a very long tube with a small 'diameter'. This is also apparent in the Log files where the CGP Iterations in the flow and temperature solvers are consistently hitting the default maximum of 1000. If you go into the Physics/Setup panel from the Flow ribbon, then Advanced Controls, you can try enabling 'Modify Flow Stagger Settings' and 'Modify Temperature Stagger Settings' and increase the Maximum Linear Solver Iterations to 3000 or even 5000. This will allow more passes each time step to improve the inner convergence of the equations - to overcome the high aspect ratio flow path. Typically you'll see more iterations in the first several time steps, thus longer runtime also, but then the iterations should reduce over time.
With the absolute value of the residuals - you want to focus on the larger values to see where those occur - paying attention to both the solid and fluid volumes. You could create isosurfaces of the absolute value and focus on the higher values for that isosurface.
The reverse flow at the outlet could also be causing issues. You may see improved performance by extending a 'tube' or 'duct' from the current outlet - moving the eventual outlet farther away from that bend just before the current outlet. That bend will cause some vortex structures which apparently pass through the current outlet. Moving the outlet farther away will keep the vortex within the domain rather than passing through the outlet.
Hello Acupro,
Despite modifying the Maximum Linear Solver Iterations to 3000, my residual ratio doesn't seem to be improving. Should I further increase it to 5000?0 -
Jagan_21383 said:
Hello Acupro,
Despite modifying the Maximum Linear Solver Iterations to 3000, my residual ratio doesn't seem to be improving. Should I further increase it to 5000?I do see in the Log file that the Flow stagger is still reaching the maximum 3000 linear solver iterations, and sometimes the Temperature stagger does as well. So maybe 5000 max linear solver iterations is in order for this case.
Is this latest with boundary layer elements into the solid side from the interface/contact surface as well?
In the mesh image attached earlier I see a fairly large size jump from the interior elements to the last element on the outside. Perhaps ease that jump a little - make the surface elements a bit smaller?
There will be some unsteadiness in the flow due to those sharp bends by the inlet and outlet. How does it behave/converge if you run transient?
Also - are the solutions of interest changing a lot during the simulation? Or are they quite stable?
0