Back Flow Conditions in Outlet
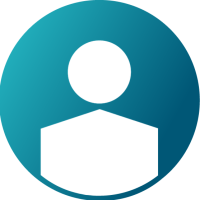
Hello experts. I'm getting "inflow at outflow boundary" and I believe that's the reason my surface outputs aren't very stable. So I'm trying to use backflow conditions. Please enlighten me about the turbulence an temperature back flow type so that I can get an idea about which one will be more relevant to my problem.
I have attached my geometry picture, input & log files for you reference. Thank you.
Best Answer
-
If you request nodal residual output, you can review isosurfaces of the absolute value of the residuals. This will give you an indication of where temperature and eddy viscosity are having trouble converging. (Though the temperature plots seem to be fairly stable already - maybe even from time step 25 or so.) Could be you need more mesh in some places.
1
Answers
-
I typically recommend starting with exiting-area-average for both temperature and turbulence quantities.
These are used to specify conditions on the flow entering at the outflow BC.
1 -
acupro_21778 said:
I typically recommend starting with exiting-area-average for both temperature and turbulence quantities.
These are used to specify conditions on the flow entering at the outflow BC.
After specifying Back flow Conditions I'm still getting reverse flow warning. And my stability in surfaces aren't very good too. Is this solution acceptable or should I run few more iterations. Kindly seeking your advice. Thankyou.
0 -
Jagan_21383 said:
After specifying Back flow Conditions I'm still getting reverse flow warning. And my stability in surfaces aren't very good too. Is this solution acceptable or should I run few more iterations. Kindly seeking your advice. Thankyou.
Yes - you'll still get the warning. But now you are setting conditions on flow entering that boundary.
There can be many things that reduce convergence - mesh resolution, boundary conditions, steady vs transient, etc.
I would probably extend the domain past the current outlet, with a contraction to reduce the final/eventual outflow/exit area. The thought here is to reduce the likelihood of flow entering from the outflow, and remove that from the possible reasons for slow convergence.
It may very well be a transient rather than steady flow.
1 -
acupro_21778 said:
Yes - you'll still get the warning. But now you are setting conditions on flow entering that boundary.
There can be many things that reduce convergence - mesh resolution, boundary conditions, steady vs transient, etc.
I would probably extend the domain past the current outlet, with a contraction to reduce the final/eventual outflow/exit area. The thought here is to reduce the likelihood of flow entering from the outflow, and remove that from the possible reasons for slow convergence.
It may very well be a transient rather than steady flow.
I have changed few BCs and re ran the model. And these are the residuals and surface statistics.
Kindly seeking your opinion about this. Thank you.
0 -
The Log file still shows the solution ratio to be quite high - above 0.1. This means the solution is still changing quite a lot from time step to time step. It could be related to still having entering flow at the outlet, or that the flow is inherently transient. Have you tried adding additional length with a contraction to the outlet? (See the attachment - outflow would be at the top in the image)
The temperature solution is struggling to converge also - hitting the maximum 1000 linear solver iterations each time step. Though the convergence is not horrible. Do you have at least three elements across the solids? Mayb
0 -
acupro_21778 said:
The Log file still shows the solution ratio to be quite high - above 0.1. This means the solution is still changing quite a lot from time step to time step. It could be related to still having entering flow at the outlet, or that the flow is inherently transient. Have you tried adding additional length with a contraction to the outlet? (See the attachment - outflow would be at the top in the image)
The temperature solution is struggling to converge also - hitting the maximum 1000 linear solver iterations each time step. Though the convergence is not horrible. Do you have at least three elements across the solids? Mayb
Across the slot insulation which is 0.4mm thick I have 3 nodes. These are my results with contracting outlet.
Thank you.
0 -
If you request nodal residual output, you can review isosurfaces of the absolute value of the residuals. This will give you an indication of where temperature and eddy viscosity are having trouble converging. (Though the temperature plots seem to be fairly stable already - maybe even from time step 25 or so.) Could be you need more mesh in some places.
1