Problem with Non-linear Direct Transient Analysis of thin metal sheet
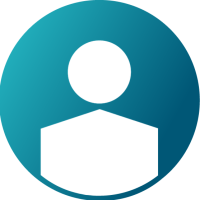
Hi folks,
I am currently trying to analyze a non-linear transient problem (see attached input file). First of all, a short description of what I am trying to accomplish. I want to simulate a thin sheet of metal (property PSHELL T=0.4) that shall be rotated 180° about x-axis at one end (node 585). This bending motion shall be achieved through a torque load which is applied at node 585. The value of this torque load (0.7363 Nm) was calculated in advance by using the same model but instead of a torque load an enfoced displacement (DOF4=3.142) was applied at node 585 and the resulting SPCF at that node was determined. The model for determining the SPCF has the same load curve (TABLED1) as the attached model but terminates at 1s (only ramp-up of load). The other end of the sheet (nodes 1-11) is constrained at every DOF.
The torque load shall follow the load curve TABLED1 which defines a ramp-up of the torque load (0-1s), then a sharp ramp-down of the load (1.0-1.1s) and finally no load at all so that the metal sheet is allowed to oscillate until it regains its initial undeformed state.
The model - as mentioned earlier - shall be subject to a non-linear direct transient analysis. Therefore, NLPARM and NLADAPT cards are defined. And this is where I have some complications in the model. I have run the model multiple times first using default values and then trying to adjust the values to reach convergence. When using default values on NLPARM card (and leaving NLADAPT out of the analysis all together) the time increments become very small (ca. 1e-5) and the solution takes hours. When applying NLADAPT with values for DTMIN and DTMAX the solver fails to reach convergence. This for example is the case, when you run the attached input file. It errors out because the minimum increment size is reached. Could somebody give me a tip as to why my model won't converge? Further, I read in different forum posts and OptiStruct help material that for most problems NLPARM default values will work fine. If this is so, why won't they work for my problem?
In addition, I have tried different load curves for the attached analysis problem. Initially, I modelled only the ramp-up of the torque load (0-1s). The solution took some time and used very small increments but it came to a realistic result. Then I defined a load curve where the load is ramped-up and then held at the maximum level for an additional second (1-2s). Here the ramp-up worked out fine but then, during the holding of the torque level, the metal sheet bounced around and oscillated. Why is this so, can somebody give me clue? Shouldn't the metal sheet stay in the same bent position when maximum torque load is applied? With the current load curve (see attached input file) the ramp-up of the load (0-1s) seems to be no problem. But the sharp ramp-down of the load (1.0-1.1s) seems to cause trouble for the solver.
So, after this long description I hope some of you are still reading. In summary, when trying to simulate the bending and release of a thin metal sheet (non-linear direct transient analysis) I have problems achieving convergence. What could cause these convergence issues? How do I define the NLPARM and NLADAPT cards so that convergence can be achieved in a sufficient and acceptable time frame?
I would be really grateful if somebody with some experience with these kind of problems could have a look at my input file and make some suggestions as to what I am doing wrong or what I could change in the input data.
Cheers,
cfuser
PS: the system of units is N, m, s
Answers
-
Hi,
the loading function should be smooth with the implicit method; slope instantly turning from positive into negative is causing convergence difficulties.
Using PARAM>EXPERTNL>YES will hyperwork
/emoticons/default_cool.png' title='B)' />
0 -
Hey Hyperman,
first of all, thank you for your quick reply. If I understand correctly (and after looking at your edited version of my input file) you only added PARAM, EXPERTNL, YES. Is that correct? I ran your edited version, but it errors out at the same increment und load step as my unedited input file. Did you run your input file with the added PARAM? If so, did the solver manage to run the analysis with out errors?
0 -
Hi,
glad to help.
I only added EXPERTNL and it completed without errors in ten minutes- it would solve faster if DTMAX on NLADAPT was not used. I have no explanation why it failed on your end. Which version are you using? I am using version 2019.1 and ran with solver run options: -len 120000 -nt 4
0 -
Hi Hyperman,
I am using Altiar HyperWorks 2017.2 Student Edition. Do you think it could be a HyperWorks Version issue?
I ran with solver run options: -nt 4. Thank you, by the way, for your shared files. Really helping me out here
/emoticons/default_smile.png' srcset='/emoticons/smile@2x.png 2x' title=':)' width='20' />
PS: I had a look at the h3d-file in HyperView. I'm glad that the you were able to solve this analysis setup, but I find the oscillation after unloading of the metal sheet quite extreme. In comparable models (same parameters for damping etc.) I observed considerably smaller oscillations. I checked some possible error sources e.g. the display settings concerning the deformation shape. But they are all set to reasonable values. Have you got any tips?
0 -
Hi,
hopefully, someone from Altair support will look into the issue.
the unit system is N, m, s and the plate dimensions are 0.05x0.26. In the description above you mentioned the shell thickness is T=0.4 (meters?) but in the model the shell thickness is 0.0004 (0.4mm) resulting in the warning message reported in the out file:
*** WARNING # 1265
PSHELL 1 has bending properties defined
and thickness T = 0.0004, which is less than or equal to 0.001.
This can lead to matrix singularities, causing message 153.
If this property is intended to define a membrane, please leave
MID2 and MID3 blank on the PSHELL data, or use PARAM,SHL2MEM.While I'm not sure if this might be causing unexpected oscillations, it should at least be checked. Unfortunately, I have no experience with comparable models to give useful tips.
0 -
Hi,
the shell thickness is supposed to be this thin (0.0004m). And yes, the unit system is N, m, s. I am aware of the warning (thanks for pointing it out anyways). As it does not effect similar analysis I have run with same shell thickness, I don't suppose this will be the source of the oscillations.
Cheers
/emoticons/default_smile.png' srcset='/emoticons/smile@2x.png 2x' title=':)' width='20' />
0