Rigid Walls During Tank Slosh
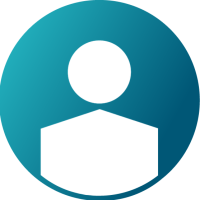
Hi all,
I am having difficulty with results interpretation when I do a tank slosh analysis. I have uploaded my files for reference. I wanted to upload the results, but they exceed the limit for size. I have pictures for reference.
In the model, I have SPH particles slamming into the sidewalls of a tank, however as you can see, there is hardly any stress in the walls. This makes no sense, and is leading me to believe there is a high rigidity from something I have done, but I just can't seem to pinpoint it. I tried running the simulation without beams, and even then, it was still very rigid, so I do not think it is a material or property issue. I also ran it with triple the initial acceleration, to almost no effect.
For symmetry, I created a wall dividing the tank in half, with very low density and yongs modulus, as I just wanted it to prevent SPH particles from flowing out, without actually changing the physics. The edges of the tank at the symmetry have the BC in the 246 directions, and should not be preventing any motion parallel to the symmetry plane.
If anyone has any ideas, please let me know.
Thanks in advance.
Answers
-
Hi,
the reason for very low stress and strain values is because the element size is too big to capture local stress distribution. In the model you shared the shell elements of tank walls are 235mm, while 5-10mm element size is recommended in a typical crashworthiness analysis. Because the whole tank is too big to be solved with such a fine mesh, I recommend you to somehow isolate the area of high stress and solve it using smaller mesh size (found through mesh convergence study).
https://enterfea.com/correct-mesh-size-quick-guide/
If you plan to do a convergence check, consider performing at least one refinement of the model after the first run. If neighboring elements display large differences in stress, the gradient was probably not captured in these areas, therefore some mesh refinement is recommended. In general, increasing the number of nodes improves the accuracy of the results. But at the same time, it increases the solution time and cost. Usual practice is to increase the number of elements and nodes in the areas of high stress (rather than reducing the global element size and remeshing the entire model) and continue until the difference between the two consecutive results is less than 5 to 10%.
I recommend you to go through free ebook Practical Aspects of Finite Element Simulation (A Study Guide) which covers 9.12 Mesh Density And Solution Convergence.
0