Maximum number of time increment cutbacks reached,
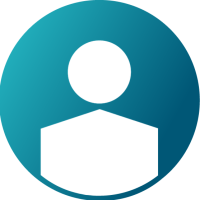
I am trying to simulate a gear assembly to analyse stress distribution around the gear teeth. It is a non-linear static with contact interaction analysis. I have used Hexmesh for the geometry. After 50% of the simulation, i am getting the error:
*** ERROR # 4965 ***
Maximum number of time increment cutbacks reached,
analysis aborted.
Could anyone please help me with this issues.
I have attached the output file and a presentation for your reference.
Find more posts tagged with
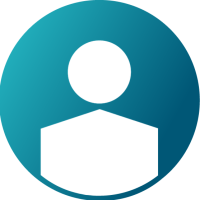
Thank you for the response Paul. I am applying rotation of 0.2rad/s. Sorry, the file size is 199 MB. Is there any other way?
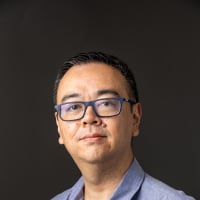

maybe you should review your contact conditions and material data.
Looks like you're getting a really large plastic strain at the interfaces. Do you have any initial penetrations in your contacts?
Just an add comment, you've mentioned 0.2rad/s, but this is a NL static analysis, so this is not exactly over time. 0.2 rad will be applied along the 100% load, and maybe this is too much.
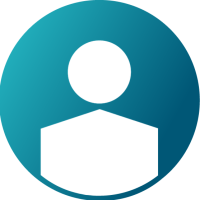
maybe you should review your contact conditions and material data.
Looks like you're getting a really large plastic strain at the interfaces. Do you have any initial penetrations in your contacts?
Just an add comment, you've mentioned 0.2rad/s, but this is a NL static analysis, so this is not exactly over time. 0.2 rad will be applied along the 100% load, and maybe this is too much.
Thank you @Adriano A. Koga for the inputs.
There is no initial penetration in the model. Maybe the rotation is to high. I will reduce it and run the simulation and let you know the results.
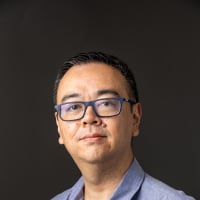

Thank you @Adriano A. Koga for the inputs.
There is no initial penetration in the model. Maybe the rotation is to high. I will reduce it and run the simulation and let you know the results.
if you're applying a 0.2 rad rotation in your model, it means ~11 degrees. If your gear assembly is locked, it looks a lot, and probably is causing this over deformation in your model, and thus element distortion.
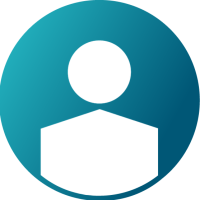
Thank you @Adriano A. Koga, your suggestions helped me a lot. I simulated the model at 0.08rad ~5° successfully. The gears almost reached break stress ;-)
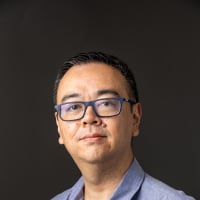

maybe you should review your contact conditions and material data.
Looks like you're getting a really large plastic strain at the interfaces. Do you have any initial penetrations in your contacts?
Just an add comment, you've mentioned 0.2rad/s, but this is a NL static analysis, so this is not exactly over time. 0.2 rad will be applied along the 100% load, and maybe this is too much.
It is difficult to know from the out and images, You should be able to see what is leading to the issue in the h3d?
Are you applying load/moment or displacement/rotation?
If you can share the model we can take a look