how to creat cohesive element with optistruct
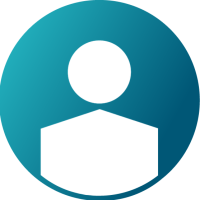
Hi, there is a question I would like to ask the teachers, recently learn to use optistruct for composite material optimization design, encountered some unsolvable problems, I want to use the cohesive element to simulate the cementation damage between the composite layers, but there is no cohesive material in the hypermesh. There is no such material property, no damage evolution rule and damage criterion of the cohesive element. There is a cohesive element in the hypermesh-abaqus interface, but I don't know how to call it in the optistruct. So,is there any methods to solve this ,could you give me a reply .best wishes.
Answers
-
Hi @Amasker
Please check RADIOSS instead of OptiStruct. You can use cohesive elements (PROP/CONNECT with MAT/CONNECT or MAT83)
0 -
Altair Forum User said:
Hi @Amasker
Please check RADIOSS instead of OptiStruct. You can use cohesive elements (PROP/CONNECT with MAT/CONNECT or MAT83)
Thank you for your reply,I am a newbie, recently working on the optimization of composite materials, a layer of composite material with a layer of steel, and the layers are bonded with cohesive elements. I don't know much about RADIOSS. I am not sure if RADIOSS can be optimized like OPTISTRUCT? Could you give me some RADIOSS tutorial on composite material optimization design? Thank you .
0 -
Hi Amasker,
maybe you can use the SB allowable inter-laminar shear stress (shear stress in the bonding material) in the PCOMP, PCOMPG or PCOMPP cards. The interlaminar shear stress is probably different for matrix and the cohesive bond- so it might not be appropriate in case you have more than one successive fabric ply.Optimization can also be done in Radioss, but it is not as user-friendly as Optistruct (no GUI) and it has some limitation. Please refer to the Design Optimization chapter and tutorial RD-E: 5101 Thickness Optimization for B-Pillar in Radioss help.
0 -
Hi Ivan,Thanks for your reply。
You are right, I tried to use RADIOSS to do some optimization design, found that it is difficult to operate, It is not convenient as OPTISTRUCT, and I am not sure whether RADIOSS can do the optimization design of composite materials like OPTISTRUCT?
There is another question. Do you think that SB allowable inter-laminar shear stress should only be applied between composite layers, between PLY and PLY? It is possible that I did not express clearly. I want to design a composite board and a steel plate, composite plate and steel plate are bonded with COHESIVE element, temporarily do not consider the interlaminar shear stress between composite ply layers. Could you give some good suggestions?
0 -
Hi,
from Radioss help:
Composite Topology and Free-size Optimization
For composite structures, topology and free-size optimization are defined through the DTPL and DSIZE Bulk Data Entries, respectively.
Both are supported in the HyperMesh Optimization panel. Features available include: minimum member size control, symmetry, pattern grouping and pattern repetition.
Topology and free-size methods target a system level composite design where laminate family definition is the objective. Therefore, the PCOMP model should not reflect a detailed stacking of plies of the same orientation. For example, even though 10 layers of 0 degree graphite cloth might be separated in the stacking of the final structure, the modeling for a concept study using topology and free-size should group them together in one ply in the PCOMP, so that the optimal total thickness distribution of a 0 degree ply is optimized throughout the structure.
Involving both topology and free-size in the same optimization problem is not recommended, since the penalization on topology components creates a bias that could lead to sub-optimal solutions.
Note: Prior to OptiStruct 8.0, composite topology optimization was based on the notion that the homogenized properties of an element remain unchanged. This construct does not allow the freedom for material redefinition. However, if this is indeed a preferred assumption, the HOMO option can be set on the MAT line of the DTPL card. Otherwise, an individual ply-based formulation (discussed above) will be the default option.
Involving both topology and free-size in the same optimization problem is not recommended, since the penalization on topology components creates a bias that could lead to sub-optimal solutions.Note: Prior to OptiStruct 8.0, composite topology optimization was based on the notion that the homogenized properties of an element remain unchanged. This construct does not allow the freedom for material redefinition. However, if this is indeed a preferred assumption, the HOMO option can be set on the MAT line of the DTPL card. Otherwise, an individual ply-based formulation (discussed above) will be the default option.6Maybe you could model bonding with springs?0 -
Altair Forum User said:
Hi,
from Radioss help:
Maybe you could model bonding with springs?But that will only help in assememnt and may not help in damage failure propagation, etc...
0 -
Altair Forum User said:
Hi,
from Radioss help:
Maybe you could model bonding with springs?Thanks, @Ivan,,It's helpful for me.
The latest RADIOSSS version is very different from the previous version. Recently, it is mainly to optimization. RADIOSS will learn slowly later, thank you.
Can I ask another question? About Tailor Rolled Blank (TRB) When I was designing the sub-region size of the steel plate, I started thinking about the transition zone, so that the optimization result was wrong, but now I don't know how to create the transition zone. Can you give me some advice? Thank you.
0 -
Altair Forum User said:
But that will only help in assememnt and may not help in damage failure propagation, etc...
Thanks for your help, @Parkash Pagadala,
Could I ask another question? About Tailor Rolled Blank (TRB) When I was designing the sub-region size of the steel plate, I started thinking about the transition zone, so that the optimization result was wrong, but now I don't know how to create the transition zone. Can you give me some advice? Thank you.
0 -
Altair Forum User said:
Thanks for your help, @Parkash Pagadala,
Could I ask another question? About Tailor Rolled Blank (TRB) When I was designing the sub-region size of the steel plate, I started thinking about the transition zone, so that the optimization result was wrong, but now I don't know how to create the transition zone. Can you give me some advice? Thank you.
Can you give us some clue like an image?
0 -
Thank you,@Parkash Pagadala,
Just as the B-pillar in the first picture is divided into four regions, it is now necessary to optimize the size of the four regions according to the stress state, and optimize the thickness of the four regions separately, and set different upper and lower limits of thickness, due to the optimized phase. The thickness of the adjacent area is different, and the transition zone needs to be set so that the thickness continuously changes like the second picture. could you give me some advice?
0 -
Hi,
You can create mesh transition zones,
Please refer to this post:
https://community.altair.com/community?id=community_question&sys_id=df76083a1b2bd0908017dc61ec4bcbe6
0 -
-
Prakash Pagadala,,I may not express it clearly.
I made a simple example. The whole part uses a shell element, in which the green area is a thick area, the red area is a thin area, and the middle yellow part is a transition zone, as shown in the first image.
<?xml version="1.0" encoding="UTF-8"?>
Then the material properties are assigned to the components, and the thickness is set separately, the thickness is 2 mm, the thin zone is 1 mm, and the intermediate transition zone is 1.5 mm, as shown in the following figure.
<?xml version="1.0" encoding="UTF-8"?>
My main purpose is to do size optimization of the thick and thin areas. Since the thick and thin areas are different after thickness and the thickness is not continuous, the transition zone is set to achieve continuous thickness variation. The thickness variation is shown in the figure below.
I don't know how to set the design variables of the thickness of the thick and thin areas and the relationship with the transition zone.I don't know how to achieve the continuous thickness effect of the illustration below。
Now,Could you give some suggestion?
0 -
OK, I it is clear. Sorry for my last reply.
My initial idea is to use a move limit on Gauge panel (say 0.1 or 0.05).
Let me check if there is a better way to link the thickness of different zones.
0 -
Prakash Pagadala,I will wait your reply。
0 -
For old way doing TRB optimization was to use gauge optimization and link the DesVars via an equation and limit the thickness change with a constraint. but there of course you need to know/define the zones upfront with different properties.
Since OS14 there is another more straight forward way directly aimed to produce TRB results. There you use FreeSize optimization with linear/planar pattern grouping. planar is better choise in case of curved structure as a B-pillar is. In addition you can/should apply thickness gradient constraint in DSIZE-card, so that thickness change is limited to the value which is manufactorable with TRB. So this new way is very easy to setup, as you need only 1 property and 1 DSIZE-card.
Thanks
Kristian
0 -
I made a simple size optimization model, the following is the fem file, found that the deequation setting does not work, I can not figure out what the reason,
if it is convenient, then introduce me some tutorials or cases in this area, explore for a long time to find No reason,
please give pointers, thank you
0 -
-
I tried the previous method and quoted the Dequation. I found that only the thickness of the transition zone was obtained, but I could not get a continuous linear thickness.
By consulting other people's literature, I found that the author set the plate thickness and the transition zone coordinates into design variables. This gives a linear change in the thickness of the transition zone, but I am not sure how to set the transition zone coordinates as design variables.
In addition, regarding the second method, to be honest, I have not figured out how to set linear/planar pattern grouping up. Can you provide some information or tutorials for Method 2?
0 -
Hi @Amasker Here is a tutorial on Pattern grouping with Topology optimization, but you can extend the same to Freesize https://altairuniversity.com/wp-content/uploads/2014/01/tutorial_topology-optimization-with-pattern-grouping.pdf
0 -
Thank you very much for your tutorial and patient guidance. I tried it according to your tutorial. Some questions are not understood.
First, the pattern grouping in your tutorial is in topology optimization. Is it also applicable in free size optimization?
Secondly, I think that in the TRB transition zone, the thickness of the thin zone and the thick zone are connected, and the thickness can be changed linearly to avoid abrupt changes in the thickness of the thin zone and the thick zone after optimization, resulting in uneven distribution of stress. It is possible that I do not understand the pattern grouping corrcetly. So, I really don't know how to apply pattern grouping in the transition zone. Ideally, I want to get the shape shown below,
There is still a question. How can the thickness after optimization be more intuitive? Can I generate files in .fem format for easy viewing?
thank you.
0