Unable to generate Spot weld connection between Solid elements
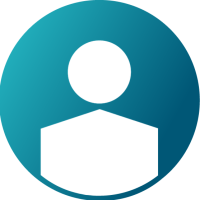

Hello Everyone,
I am trying to establish spot weld between Solid Hexa8N elements. I have tried to use 'plot', 'Type 2 spring' and 'HC Hexa' type. But in all the cases I am having following issues:
1) Type (Plot): Simulation ran but solid elements were not connected
2) Type [Spring (Type 2)]: Solver not able to identify the surface to create a spring elements.
3) Type HC Hexa: Contact interface defined by solver itself is not correct.
Apart from aforementioned problem I also want to give the max tensile strength of spot weld as as 40% of base material.
Thanks in advance.
Nitin Jain
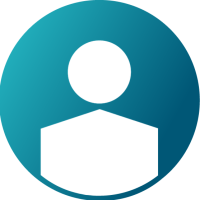

Hello @Pranav Hari,
I have uploaded the file on the shared link.
But I have deleted some parts and Boundary conditions.
Please assign boundary condition as per your convenience.
Regards
Nitin Jain
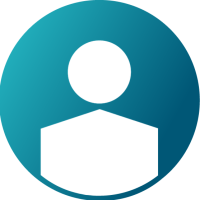
Hi Nitin Jain
The recommended element types in Radioss for spot weld creation are shell element.
Surface 1 and 2 for each solid spotweld should always connect with a shell element. If one surface of one solid spotweld is not connected with a shell element, then the stiffness will not be computed correctly and an error may occur
|
Since you are having solid elements you have to create a shell coat and then connect using spots.
There are three different ways of modeling spotweld:
• | Node Connect |
• | Spring (/PROP/TYPE13) Connect |
• | Solid Connect |
When you create a spot weld using type 2 spring, by default you will get the (TYPE13 spring property + TYPE2 contact).
In your case since you have to define max tensile strength of spot weld as 40% of the base material, then I recommend you use the solid connect method.
Here you can specify separate failure criteria.
This is explained in detail in the Radioss help documentation. Please have a look
Also, have a look at the Radioss example on solid spot weld creation.
<?xml version="1.0" encoding="UTF-8"?>
I have shared the 2 example deck files, which is modeled using default spring contact and also solid connect. Check that too.
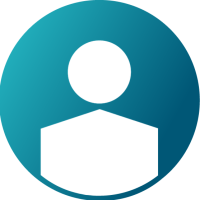
Since you are having solid elements you have to create a shell coat and then connect using spots.
Contact surfaces can also be used.
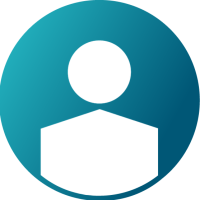

Thanks @Pranav Hari and @Ivan,
I think making surface and then spot weld is time consuming process.
Moreover I request you to please teach me, if I connect the extracted surface with connector: then solids will be connected as well or it will connect only extracted surfaces.
Right now, I am trying to make the Seam weld connections (Hexa Tapered T type) but I am getting the distorted elements:
<?xml version="1.0" encoding="UTF-8"?>
I am avoiding edge nodes for better results. But still some elements are not as desired.
Regards
Nitin Jain
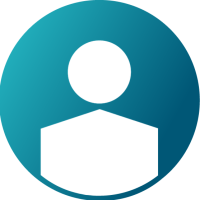

Hello everyone,
Does someone know how to solve the above mentioned problem??
Thanks in advance.
Regards
Nitin Jain
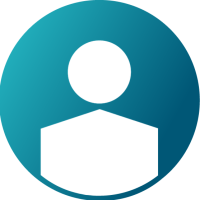
hi you
i had refered the document, so i never make stiffness of spring, because the result also flying
pelase show me
thanks
Hi
Can you please share your model.
You can use the secure drop box link https://ftin.india.altair.com:8443/filedrop/~Ma3TaE