Analys of cover detaching with optistruct
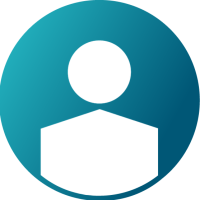

Hi
i'm trying to simulate an packaging consiting of two parts, the bottom and the cover. The cover is fixed with one plane on the upper side of a lipsurface on the top of the bottom an on the buttomside of the lipsurface. (See figute below) . The aim is to look when the cover ist detaching from the rest.
My problem is i don`t know how two simulat that problem. every time i am running the imulation there is no convergence
I created the cover and the bottom and also the contac surfaces and interface with overlap.
After i Created the pcont card, material, conprm, constrains, an the NLParam and forces
THe LoadCase is non linear static analyse.
The problem is there are no results running that simulation.
can you tell me where is my problem?
<?xml version="1.0" encoding="UTF-8"?>
Answers
-
could you share us out file of the run?
0 -
-
I suggest you to solve this problem with OptiStuct NLSTAT loadcase and not with NLGEOM.
Please add PARAM,LGDISP,1 to the deck to activate large displacement formulation ( Similar to NLGEOM) and re-run the job with NLSTAT loadcase ( Just update the load case type to Non-linear Quasi-Static)
For me it is running.
0 -
i tried it and this is the output of the solver
*** OptiStruct defaults set from:
install config file: C:\Program Files\Altair\14.0\/hwsolvers/optistruct.cfg.
NOTE # 9199
MSGLMT=STRICT is active, all messages will be printed.
You can suppress some less important warning messages by use of
MSGLMT=BRIEF or UNREF (in config file or in the input data).1 PARAM(s) were set:
LGDISP,1*** WARNING 1932: PCONT ID 3 is not referenced.
*** INFORMATION # 1579
for material id = 1 referenced from property id = 1.
MATS1 referred to from MID3 will be ignored - plasticity is
supported for membrane and bending deformation, but not for transverse shear.*** INFORMATION # 1579
for material id = 1 referenced from property id = 2.
MATS1 referred to from MID3 will be ignored - plasticity is
supported for membrane and bending deformation, but not for transverse shear.*** INFORMATION # 4736
The realization of node-to-surface contact at large displacements is not
exactly the same as in small displacement (NLSTAT) analysis. No internal
CGAP/CGAPG elements are created in the large displacement case.The amount of memory allocated for the run is 791 MB.
This run will use out of core processing in the solver.************************************************************************
OPTIMIZATION FILE AND PARAMETER INFORMATION :
---------------------------------------------
FEM model file :
C:/Users/Benjamin/Desktop/WP1/Hypermesh_works/neue_ideenlstat2.fem
Output files prefix :
C:/Users/Benjamin/Desktop/WP1/Hypermesh_works/neue_ideenlstat2
************************************************************************************************************************************************
FINITE ELEMENT MODEL DATA INFORMATION :
---------------------------------------
Total # of Grids (Structural) : 23268
Total # of Elements Excluding Contact: 22375
Total # of N2S Contact Elements : 861 (no internally created CGAPG)
Total # of Degrees of Freedom : 131952
(Structural)
Total # of Non-zero Stiffness Terms : 3635232Element Type Information
------------------------
CQUAD4 Elements : 22112
CTRIA3 Elements : 263
Load and Boundary Information
-----------------------------
FORCE Sets : 1
SPC Sets : 1
Material and Property Information
---------------------------------
PSHELL Cards : 2
PSHELLX Cards : 2
PCONT Cards : 1
MAT1 Cards : 1
MATS1 Cards : 1
************************************************************************************************************************************************
OPTIMIZATION PROBLEM PARAMETERS :
---------------------------------
NO DESIGN MATERIAL OR DESIGN VARIABLES FOUND : ANALYSIS ONLY
------------------------
Static Subcase Summary :
------------------------
---------- -------- --------
Subcase ID SPC ID FORCE ID
---------- -------- --------
2 1 4
---------- -------- --------
Run Type : Analysis Only (No design elements)
Run at location : C:/Users/Benjamin/Desktop/WP1/Hypermesh_works/
Scratch file directory : C:/Users/Benjamin/Desktop/WP1/Hypermesh_works/
Free space: 834.044 GB
Number of CPU processors : 1
************************************************************************************************************************************************
MEMORY ESTIMATION INFORMATION :
-------------------------------
Solver Type is: Sparse-Matrix Solver
Direct MethodCurrent Memory (RAM) : 791 MB
Estimated Minimum Memory (RAM) for Out of Core Solution : 709 MB
Recommended Memory (RAM) for Out of Core Solution : 791 MB
Recommended Memory (RAM) for In-Core Solution : 1010 MBDISK SPACE ESTIMATION INFORMATION :
-----------------------------------
Estimated Disk Space for Output Data Files : 16 MB
Estimated Scratch Disk Space for In-Core Solution : 78 MB
Estimated Scratch Disk Space for Out of Core Solution : 479 MB
************************************************************************
BEGINNING ANALYSIS SOLUTION ....
************************************************************************
ANALYSIS RESULTS :
------------------ITERATION 0
Starting load increment 1 Current increment 0.1
Nonlinear iteration summary for Subcase 2
Subcase 2 Load step: 0.1000
--------------------------------------------------------------------------------
Nonlinear Error Measures Gap and Contact Element Status Maximum
Iter Avg. U EUI EPI EWI Open Closed Stick Slip Frozen Plststrn
--------------------------------------------------------------------------------
1 6.99E+07 1.01E+00 2.26E-05 2.26E-05 626 235 0 0 0 0.00E+00Adjusting load increment 1 (correction #1), Current increment 0.025
Nonlinear iteration summary for Subcase 2
Subcase 2 Load step: 0.0250
--------------------------------------------------------------------------------
Nonlinear Error Measures Gap and Contact Element Status Maximum
Iter Avg. U EUI EPI EWI Open Closed Stick Slip Frozen Plststrn
--------------------------------------------------------------------------------
1 1.75E+07 1.01E+00 2.26E-05 2.26E-05 626 235 0 0 0 0.00E+00Adjusting load increment 1 (correction #2), Current increment 0.00625
Nonlinear iteration summary for Subcase 2
Subcase 2 Load step: 0.0063
--------------------------------------------------------------------------------
Nonlinear Error Measures Gap and Contact Element Status Maximum
Iter Avg. U EUI EPI EWI Open Closed Stick Slip Frozen Plststrn
--------------------------------------------------------------------------------
1 4.37E+06 1.01E+00 2.25E-05 2.25E-05 626 235 0 0 0 0.00E+00Adjusting load increment 1 (correction #3), Current increment 0.001563
Nonlinear iteration summary for Subcase 2
Subcase 2 Load step: 0.0016
--------------------------------------------------------------------------------
Nonlinear Error Measures Gap and Contact Element Status Maximum
Iter Avg. U EUI EPI EWI Open Closed Stick Slip Frozen Plststrn
--------------------------------------------------------------------------------
1 1.09E+06 1.01E+00 2.24E-05 2.24E-05 626 235 0 0 0 0.00E+00Adjusting load increment 1 (correction #4), Current increment 0.0003906
Nonlinear iteration summary for Subcase 2
Subcase 2 Load step: 0.0004
--------------------------------------------------------------------------------
Nonlinear Error Measures Gap and Contact Element Status Maximum
Iter Avg. U EUI EPI EWI Open Closed Stick Slip Frozen Plststrn
--------------------------------------------------------------------------------
1 2.73E+05 1.01E+00 2.21E-05 2.21E-05 629 232 0 0 0 0.00E+00Adjusting load increment 1 (correction #5), Current increment 9.766e-005
Nonlinear iteration summary for Subcase 2
Subcase 2 Load step: 0.0001
--------------------------------------------------------------------------------
Nonlinear Error Measures Gap and Contact Element Status Maximum
Iter Avg. U EUI EPI EWI Open Closed Stick Slip Frozen Plststrn
--------------------------------------------------------------------------------
1 6.82E+04 1.01E+00 1.50E+04 1.50E+04 641 220 0 0 0 2.38E+11*** ERROR # 4965 ***
Maximum number of time increment cutbacks reached,
analysis aborted.*** Nonlinear solution failed to converge for Subcase 2 ***
Non-convergent nonlinear iterations - no solution saved.
(Scratch disk space usage for starting iteration = 279 MB)
(Running out-of-core solution)
Volume = 1.27078E+004 Mass = 1.15323E-002
Subcase Compliance Epsilon
2 0.000000E+00
Note : Epsilon = Residual Strain Energy Ratio.
(not available for LGDISP and linear gap / fast contact)
************************************************************************ANALYSIS COMPLETED.
*** SOME ERRORS WERE REPORTED DURING THE RUN,
*** PLEASE VERIFY RESULTS AS THEY MAY BE INVALID.************************************************************************
RESOURCE USAGE INFORMATION
--------------------------
MAXIMUM MEMORY USED 791 MB
MAXIMUM DISK SPACE USED 292 MB
************************************************************************
************************************************************************
COMPUTE TIME INFORMATION
------------------------
EXECUTION STARTED Mon Jul 18 11:51:57 2016
EXECUTION COMPLETED Mon Jul 18 11:52:55 2016
ELAPSED TIME 00:00:57
CPU TIME 00:00:49
***************************************************************************** END OF REPORT *****
For Useful OptiStruct Tips and Tricks, go to the URL:
http://www.altairhyperworks.com/tips.aspx
*************************************************************************** SOME ERRORS WERE REPORTED DURING THE RUN,
*** PLEASE VERIFY RESULTS AS THEY MAY BE INVALID.
*************************************************************************** PROGRAM STOPPED: FATAL ERROR(s) ENCOUNTERED.
==== End of solver screen output ====
==== Job completed ====0 -
what material you are using? Enter yield strength of material in Limit1 of MATS1 card.
0 -
你的模型有以下几个问题:
1、最大的问题:模型中 网格有好几个地方是没有连接起来的。 检查自由边可以检查到该问题。
2、你定义的接触有问题,接触法向 与单元的法向 没有匹配起来。
建议将 壳单元 直接定义成接触体
3、你最好先把接触问题 调整好了之后,你在设置其他的非线性问题。--------------
Your model has following problems:
1, the largest problem: Free edges.Mesh of several places were not connected in the model. Check the 'free edges' to check this problem.
2, the contact problem: the normal of the contactsur did not match the element,and the normal in the interface(group) were reversed.
It is recommended to define the 'elem entity' directly.
3, you'd better solve the contact problem firstly,and then, set other non-linear problems.0 -
Hi,
i am getting the below error while running NLSTAT with LGDISP option
Maximum number of time increment cutbacks reached,
analysis aborted.Model is running successfully with Linear Static. Any suggestions?
Regards,
Kandiyal
0 -
Hi,
Can you share the entire .out file, please?
0 -
Hi ,
I am getting same error which is :
Altair Forum User said:Maximum number of time increment cutbacks reached,
analysis aborted.I have applied enforced displacement to the part. But problem is that contact is not working. I have tried also in linear static analysis but again contact is not working although I set search distance to 2 mm. ( Mesh size is 0.4 mm)
Can you look my analysis model ?
0 -
Hi @Tevfik Uzun
I can see the model takes up to 60% load. Can you check if there is any element distortion from non-converged result file?
Can you add NLADAPT with NCUTS to increase the cutbacks?
If this still did not help, can use S2S contact with continuous sliding (CONSLI) in contacts?
0 -
Altair Forum User said:
I suggest you to solve this problem with OptiStuct NLSTAT loadcase and not with NLGEOM.
Please add PARAM,LGDISP,1 to the deck to activate large displacement formulation ( Similar to NLGEOM) and re-run the job with NLSTAT loadcase ( Just update the load case type to Non-linear Quasi-Static)
For me it is running.
Sorry, but have to reopen this post.
Iḿ doing a non linear quasi static analysis with mats1 materials and everything is without errors.
I used nlstat for small displacement, but i am not shure if i should use LGDISP. So i want to test it. Is it enough to add PARAM,LGDISP,1 or do i need something else?
Or should i also add NLPARMX also? The optistruct reference guide is not that clear in this case and it is recommended to use NLGEOM (Radioss??).
0 -
To run large displacement analysis with OptiStruct version2017.2.4 or higher version use of PARAM,LGDISP,1 is enough.
0 -
-
Please share the out file of the run?Use first order element to avoid element distortion.
0 -
Altair Forum User said:
Please share the out file of the run?Use first order element to avoid element distortion.
I had to cut it a little bit, because of confidential data.
I had a look at the elements, they should all be first order.
0 -
Can you please increase the NCUTS as 10 in NLADAPT card and run again.
0 -
Hi Rahul,
I am also facing the same issue and updated your suggestions such as PARAM,LGDISP,1 & N CUT Options
But didn't get resolved.
Regards,
Arul
0