Query about OptiStruct Topology Optimization
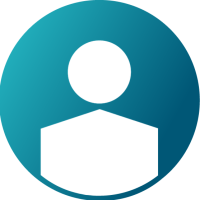

Hello,
can you tell me? I am not getting the complete result of my topology optimization. I wanna do topology optimization of the differential case of differential gear box. My FEA analysis is fine but optimization results are showing only in blue and red region form in element density. and how to compare of our final result from our original model that how much material we can or did remove from the model?
Answers
-
Hi,
Please share a picture of the results and also the topology setup.
0 -
Hi Prakash, These are my results one is element density and others are stress results. I used two responses Vol and disp, and objective is to minimize the vol and constraint is disp. upperbound limit is 0.5.
0 -
Hi,
I do see some intermediate contour between 1 and 0.3 in element density results.
Try to play with ISO contour value.
0 -
dear bro, these are ISO-contour values I've shown you.
0 -
Waqas,
Does your optimization setup include any manufacturing constraints, minimum and maximum member size values, etc...?
What ISO value are you looking at?
0 -
no. i don't have any manufacturing constraint. i wanna do topology optimization and remove material from my model but actually i don't understand how to get optimal results.
0 -
Waqas,
Just check the results, If the analysis ends without violation of constraints and respects all the constraints and objectives then your model is optimized.
For instance, in your case the constraint is 0.5units of displacement. If your model satisfies this constraint and material is removed as you wanted, then your model is optimized.
0 -
ok. thanks, i have shown in picture one which i shared to you element density. In this picture just only blue and red region are showing so how can i remove material from this result.? and whats the units and meaning of element density in hyperWorks.
0 -
I can see some material is removed from the model. You can still increase the ISO value to see how the model show up after removing further material.
I suggest you to add manufacturing constraints to your model to get meaningful results.
0 -
i don't have any idea about manufacturing const. can you tell me about this option in optstruct, how to apply mfg const?
0 -
i've shown again this picture, can you tell is it right?, anything wrong with this results, only blue and red region are showing, why others color are not showing?
0 -
Manufacturing constarints are available to enhance the design optimization. You can include minimum and maximum member size to improve manufacturability of the component as very thin members may not sustain. So in order to avoid such, you need to include manufacturing constraints.
You can specify draw direction for casting products for example. There are few other manufacturing constraints available. Please go through OptiStruct user guide to know more.
0 -
Altair Forum User said:
i've shown again this picture, can you tell is it right?, anything wrong with this results, only blue and red region are showing, why others color are not showing?
Other intermediate element densities maybe hidden inside the compnent. changing the ISO value can reveal the intermediate densities.
0 -
thanks my friend. I'll try
0 -
dear friend, what is the difference between in result type, element density result and strain energy result?
0 -
Hi Prakash, Theses are my results, actually, problem is that material is removing only from the surface. This is the topology optimization. You know in topology optimization material is not removing from this way. I used in design variable , select the design region and the select PSOLID type, in the resp, two response, one is volume and 2nd is static displacement. obj is mini of vol. and dconstraint is displacement used upper bound limit is 0.5. can you tell whats i am doing worng in analysis?
Thanks.
0 -
Altair Forum User said:
This is the topology optimization. You know in topology optimization material is not removing from this way.
The amount of material and where the material is removed is dependent on load path and the optimization parameters.
0 -
you mean my results are fine? There is no problem in the final results?
0 -
You need to check whether the objective is achieved and the constraints are satisfied or not.
/emoticons/default_smile.png' srcset='/emoticons/smile@2x.png 2x' title=':)' width='20'>
0 -
Altair Forum User said:
You need to check whether the objective is achieved and the constraints are satisfied or not.
/emoticons/default_smile.png' srcset='/emoticons/smile@2x.png 2x' title=':)' width='20' />
i am confused about my actual result. i don't know how to verify my result. i think according to my study material is removed like this through topology optimization<?xml version="1.0" encoding="UTF-8"?>
i am showing a picture.
0 -
Altair Forum User said:
You need to check whether the objective is achieved and the constraints are satisfied or not.
/emoticons/default_smile.png' srcset='/emoticons/smile@2x.png 2x' title=':)' width='20' />
i am confused about my actual result. i don't know how to verify my result. i think according to my study material is removed like this through topology optimization<?xml version="1.0" encoding="UTF-8"?>
i am showing a picture.
0 -
my optimization constraint is static disp. uper bound limit is 0.5. so how to verify my results in element density results? dear i want to send you PM kindly on your message privacy. thanks.
0 -
You can do a re-analysis on the optimized model using OSSmooth module in HyperMesh.
Here is a doc which tells on how to do a reanalysis: http://www.altairuniversity.com/wp-content/uploads/2015/06/1075.pdf
0 -
Altair Forum User said:
You can do a re-analysis on the optimized model using OSSmooth module in HyperMesh.
Here is a doc which tells on how to do a reanalysis: http://www.altairuniversity.com/wp-content/uploads/2015/06/1075.pdf
0 -
Altair Forum User said:
dear bro, if you don't mind can you give me your contact no or id?
Hi Waqas,
We prefer discussing on forum instead of having a personal meeting.
0 -
Altair Forum User said:
Hi Waqas,
We prefer discussing on forum instead of having a personal meeting.
ok bro. no problem.
Thanks.
0 -
Altair Forum User said:
Hi Waqas,
We prefer discussing on forum instead of having a personal meeting.
Hi Prakash,
Can you tell me? one thing is there any possibility in topology optimization, The material is removed only from the surface. due to removing material from the surface there is no change is design.
Thanks.
0 -
Altair Forum User said:
You need to check whether the objective is achieved and the constraints are satisfied or not.
/emoticons/default_smile.png' srcset='/emoticons/smile@2x.png 2x' title=':)' width='20' />
my constraints are not satisfying. I used dconstraint static disp 0.5. In the result at final iteration disp is 98.can you tell what i am doing wrong?
0 -
0
-
Altair Forum User said:
i've sent. kindly check it.
0