Parameters for type 14 (solid) property? [SOLVED]
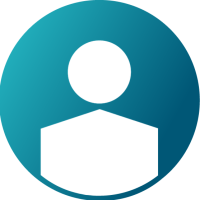

After reading the reference guide, I don't understand the parameters for the property 14:
1. Isolid - What is this for??
2. Ismstr - What is the purpose? We already define linear or non-linear in material, so why this option? What does value 4 'full geometric nonlinearities' do?
3. Istrain - What does 'strain post-processing' mean? Does this affect result values or is this just for animation purposes?
Answers
-
Refer below video from Radioss ebook.Isolid is for fromulation
Refer after 2mint for I solid & 6mint for Ismstr.
0 -
I could not understand much from the video, so I will ask questions specifically for my case:
1. What is the difference between value 1, 4 and 10 for Ismstr :
= 1: small strain from time=0
= 4: full geometric nonlinearities (/DT/BRICK/CST
has no effect)
=10: Lagrange type total strain (see Comment 20)What is the purpose of this parameter? We already define linear or non-linear in material, so why this option? What does value 4 'full geometric nonlinearities' do?
2. Istrain - What does 'strain post-processing' mean? Does this affect result values or is this just for animation purposes?
Please try to answer specifically instead of directing to some generalised video, it would save a lot of time for both of us.
0 -
Isolid is to define different solid element and hourglass formulations. The various element formulations are explained in detail In the video link provided by Rahul.
Ismstr (Strain formulation flag) has a major influence in the simulation. Usually for problems involving large deformations, a large strain formulation would be used. In RADIOSS this is the default setting, but it is also possible to use a small strain formulation. This formulation is not very accurate for large deformations, but it is more robust and enables the time step to not decrease too much. Indeed, large deformation/rotation problems may lead to mesh distortion which causes the time step to drop drastically; computation may even stop due to a negative volume. The small strain formulation overcomes all this by assuming a constant volume, consequently the time step becomes constant, and even if the mesh is completely distorted, computation will not be stopped due to the negative volume. It is also possible to switch from a large strain formulation to a small strain formulation in order to prevent a negative volume and to maintain a good time step using the /DT/BRICK/CST option in the engine file having a critical time step.The option /DT/BRICK/CST is only active if the brick elements have the flag Ismstr=2. When Ismstr is 4, ie full geometric non linearity , time step imposed using /DT/BRICK/CST will not have any effect on the simulation. Small strain formulation is activated from time t=0, if Ismstr =1. It may be used for a faster analysis, but the accuracy of results is not ensured. The flag Ismstr =10 is only compatible with some material laws using total strain
formulation (example, Laws 38, 42, 69 and 82). The Left Cauchy-Green strain is used forLaws 38, 42, 69 and 82.For detailed Ismstr - element formulation compatibility you can refer the material library available in help menu.
Istrain does not affect any result values. The strain tensor is not computed by default. By setting flag Istrain (flag to compute strains for post-processing) to 1 the user will get strain tensor output.
0 -
Thanks for the detailed reply George! I guess I will stick to large deformation option for my drop test. I am not getting any negative volume and the computation time is also fine with me.
Altair Forum User said:the user will get strain tensor output.
Is it possible to view this strain tensor with HyperView? I am viewing the plastic strain already, and from what you said, I don't think that that result is getting modified by this parameter.
0 -
-
Hi all,
I have ran an RADIOSS impact analysis. Where i am facing issue that elements are deforming severely where ever it contacts. I not sure this is due to contact issue or section properties of the solids. Please help with this.
Contact type = 7
section properties : P14 solid
All are brick mesh and the dm/m is less only
0 -
Hi,
The property card seems fine.
In the interface card try with Istf=4, Igap=2 options. Also check the material parameters and ensure they are correct.
From the time history file (T01) please plot the internal energy, kinetic energy, contact energy and hourglass energy curves in HyperGraph, take a snapshot and upload the same.
0 -
Hi George,
Please find the attached image of energy curves.I think material properties are perfect since i haev converted it from the Ls dyna model which was successful run. I have used MATLAW 36.
0 -
Hi,
Contact energy seems to be high in this model.
You can check for any penetrations/intersections in the model. The material parameters is another chance which can cause high contact energy.
0 -
Hi ,
There is no intersection in the model. And a slight penetration is there about 0.09mm and for that i have used the Inaction = 6.
0 -
Hi,
Can you please share the model file through the secure dropbox?.
0 -
Hi George,
Sorry. Unfortunately i can't share the model due to privacy.
0 -
Hi,
How did you create the Type 7 interface?. Did you create contact surfaces and recalled in the interface or selected as components?.
Can you share the material parameters?.
0 -
Hi,
I have selected the contact by components not by the contact surfaces. Please see the attached image for the same.
0 -
Hi,
Use Igap=2, and provide a Stmin of 1000 N/mm so that it will avoid too soft contact.
0 -
Hi,
I feel that there is issue in Section properties definition. Is there anyone has faced the same issue before ? element deforming severely(no Hourglass) without any error notification.
0 -
What may be the reason for below shown behavior ? It is due to contact or brick elements section parameters issue?
0