SPH in RADIOSS
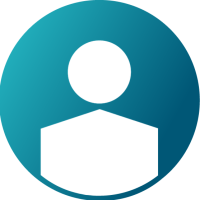

Hello guys, I need some advice:
I need to simulate the behavior of a cylinder-shaped fluid mass contained between two plates ,within a hollow cylinder (like illustrated in the figure attached). In particular, I need output data about the pressure field within the fluid due to the application of a huge force/pressure on one plate so that the whole system accelerates within the hollow cylinder at tens of thousands of g's. The other plate reacts to the motion only with its inertia, so that after a transient phase there is a steady state condition in which the distance between the two plates is fixed, for given initial data.
It's my first contact with radioss or with any explicit solvers so it's pretty hard to get what I need.
I will also attach a first model (hm file) that I built in Hypermesh. It actually runs with radioss, but with nonsense ETA if compared to the simulations time.
I also have some other question:
-where can I find a list of the control cards which are supported by RADIOSS so that I can understand how they work?
- how do I set a contact between an SPH and a 2D shell mesh? I used a type7 contact but I don't know if it is right.
If anybody could help I would be very grateful. Thanks in advance!
Answers
-
Hi,
Please download RADIOSS reference guide from http://forum.altairhyperworks.com/index.php?/topic/20652-radioss-2017-reference-manual-documents-user-guide-and-tutorials/ where you will get all the control cards. You can also check in Help.Type 7 is fine for SPH-shell elements interface. I recommend you to go through a tank drop simulation webinar where the fuel is modeled with SPH. You can access the same at https://altairuniversity.com/conceptual-design-of-a-3-wheeler-motorbike/conceptual-design-of-a-3-wheeler-motorbike-tank-drop-simulation/
After going through these start working on RADIOSS so that you will get an overall idea on the process. And do write to us if you any difficulty in between, we are happy to help.
0 -
Altair Forum User said:
Hi,
Please download RADIOSS reference guide from http://forum.altairhyperworks.com/index.php?/topic/20652-radioss-2017-reference-manual-documents-user-guide-and-tutorials/ where you will get all the control cards. You can also check in Help.Type 7 is fine for SPH-shell elements interface. I recommend you to go through a tank drop simulation webinar where the fuel is modeled with SPH. You can access the same at https://altairuniversity.com/conceptual-design-of-a-3-wheeler-motorbike/conceptual-design-of-a-3-wheeler-motorbike-tank-drop-simulation/
After going through these start working on RADIOSS so that you will get an overall idea on the process. And do write to us if you any difficulty in between, we are happy to help.
Wow, thank you very much! It was very helpful! I will try to rebuild the model correctly.
I was wondering ... I need to model the inertia of the plates and its effect on the gas compression. So if I model the lateral surface of the cylinder as a rigid wall, with the gas within that rigid wall, I still have to model the plates so that they interact with the gas due to their inertia.
So if I model the plates as shells and I assign a material property to them so that they have a given mass, will they react with inertial effects if I impose an acceleration on the whole system?
The reference frame is not an inertial frame, but it is moving with the plate which puts in motion the gas and the other plate. I hope I have been clear.
Thanks again!
0 -
You will find the new model attached. Any hint on how to solve the kinematic condition incompatibility showed by the warnings?
In addition, I would appreciate a comment on the model... am I going in the right direction?
0 -
Hi,
Incompatible kinematic conditions are an undesired warning in a model and need to find out where the nodes are over constrained or where the constraints are violating the loads applied.
As nodal constraints are based on kinematic conditions applied on nodal DOF, therefore it is not allowed to apply two nodal constraints to the same set of nodes. True incompatible kinematic conditions can generate local instability. You can check the model for any true incompatible kinematic conditions.
Model file is not shared in the above post. Please share the same (_0000.rad) so that we can review.
0 -
Altair Forum User said:
Model file is not shared in the above post. Please share the same (_0000.rad) so that we can review.
I'm sorry, I edited the last post with the correct files, it was my mistake.
BTW , I updated the model but the ETAs still are nonsense. Please check the model and let me know what is the problem, in your opinion. Thanks so much for your help.
0 -
Hi,
Just reviewed your model.
Normally for models with SPH the time step will be less and so it will take more time to run. In the 'fabric' interface there are many penetrations and I recommend you to clear those penetrations. The below link shows clearing penetrations in interface.
Instead of Type 1 interface you can try with Type 7 for other two interfaces.
Please use these recommended parameters for those two Type 7 interfaces:
Istf=4
Igap=2
Fscale_Gap=0.8
INACTI=6
Gap_min=
Fric = 0.1
Iform=2.
0 -
Altair Forum User said:
Hi,
Just reviewed your model.
Normally for models with SPH the time step will be less and so it will take more time to run. In the 'fabric' interface there are many penetrations and I recommend you to clear those penetrations. The below link shows clearing penetrations in interface.
Instead of Type 1 interface you can try with Type 7 for other two interfaces.
Please use these recommended parameters for those two Type 7 interfaces:
Istf=4
Igap=2
Fscale_Gap=0.8
INACTI=6
Gap_min=
Fric = 0.1
Iform=2.
Hi, thank you for your reply. I fixed the issues with the penetrations and changed the type 1 to type 7. Still have 3 warnings about initial penetrations in each contact group but the penetration check doesn't find anything. This time, the run doesn't start anymore due to this warnings.
You'll find the new model attached, please let me know I can I solve this problem.
I already tried changing INACTI from 6 to 3, which should help to avoid initial penetrations, but it actually don't!
Thanks again, and have a nice day!
0 -
Hi,
Which unit system you are following in the model?.
0 -
m, Kg, s, N, Pa, ecc...
0 -
Hi,
I tried running the files and it ran even though it has shown some warnings.
I strongly recommend you to recheck the material parameters, ie the unit consistency in the model. It seems like there is some error in the units of material parameters which results i high run time.
The normal unit consistency followed is attached along. Please go through it and recheck the parameters.
0 -
Altair Forum User said:
Hi,
I tried running the files and it ran even though it has shown some warnings.
I strongly recommend you to recheck the material parameters, ie the unit consistency in the model. It seems like there is some error in the units of material parameters which results i high run time.
The normal unit consistency followed is attached along. Please go through it and recheck the parameters.
Yes, actually I made a mistake with fabric datas. Thanks for your help.
Now I have modified the model deleting the fabric and adding a cylindrical pipe as wall... I launched succesfully the simulation and now I'm waiting for the results. I'll let you know how it goes!
I have another 'off-topic' question :
I need to apply a pressure which has a 3D gaussian distribution (so I need to apply an equation function of space variables x,y,z) ; I am almost sure that RADIOSS only handles equations variable in time. Is there a way to apply a pressure with that kind of distribution in space but constant in time? (just like optistruct equations)
Thanks again for your help!
Greetings.
0 -
Hi,
RADIOSS only takes a time function for pressure load, and I don't think we have an option to apply pressure as an equation.
0 -
Hi, ok thanks!
I had the results but they are useless. I applied an acceleration of 20000g's but nothing moves. What am I doing wrong?
I'm sorry for this questions but I need to bring out some reasonable result ASAP and it is my first approach with radioss. I will have the chance to follow altair's RADIOSS course in a month but I need something sooner.
I'm attaching the results along with the new model file.
I set a simulation time of 0.001 s because it was the only way to have a 'reasonable' computation time (1.5days!!!). I think that now the model has the right measure units, but I can't understand why the computational cost is that high.
Note that in the model file the simulation time is 0.0001 s because I updated it this morning , but the h3d file refers to the simulation with 0.001 s .
Again, thanks for helping!
0 -
Hi,
I checked your model. It seems like you didn't select any node or node group for defining the load.
While defining the loads select the nodes on to which the loads are applied.
0 -
Altair Forum User said:
Hi,
I checked your model. It seems like you didn't select any node or node group for defining the load.
While defining the loads select the nodes on to which the loads are applied.
I thought it was unnecessary because I selected the nodes when I defined the BCs , but now I noticed the other field. I am now running again the simulation. Any other tips on how to reduce the computational cost?
Thanks again, I appreciate your dedication.
Have a nice day!
0 -
Hi,
You can try running with an imposed time step using /DT/NODA/CST keyword. WIth this option you can make the run faster but always mind to keep the mass error less in the model.
Please go through https://altairuniversity.com/learning-library/considerations-about-time-step/ which is a webinar on time step imposing in RADIOSS.
0 -
Altair Forum User said:
Hi,
You can try running with an imposed time step using /DT/NODA/CST keyword. WIth this option you can make the run faster but always mind to keep the mass error less in the model.
Please go through https://altairuniversity.com/learning-library/considerations-about-time-step/ which is a webinar on time step imposing in RADIOSS.
Thank you! I will go through the webinar and I'll let you know about the results.
Have a nice day!
0 -
Hi,
I'm still waiting for the simulation to end, but in the meantime I just made another model with a sphere instead of the cylinder. The sphere contains the gas and the objective is to accelerate it at high accelerations (just as the cylinder) and to gather informations about the pressure field generated because of the inertia of the gas within the sphere that pushes on the lower face. (It is the same concept of the cylinder).
This time the simulation runs surprisingly fast but the problem is that, like you can see in the h3d attached, the gas modelled with sph doesn't move with te sphere as expected. What am I doing wrong?
Also, how can I get the results that I need?
Thanks for your help!
0 -
hI,
The issue with the current model seems to be with the contact created. Recreate the contact, and for slave select all the nodes of SPH and for master select the sphere.
I prefer to apply initial velocity to these components in the required direction and choose nodes selector and select all nodes (SPH and sphere components) and apply the load.
I just tried the same and the final h3d obtained is attached for your reference.
0 -
Altair Forum User said:
hI,
The issue with the current model seems to be with the contact created. Recreate the contact, and for slave select all the nodes of SPH and for master select the sphere.
I prefer to apply initial velocity to these components in the required direction and choose nodes selector and select all nodes (SPH and sphere components) and apply the load.
I just tried the same and the final h3d obtained is attached for your reference.
All right, now the gas moves with the sphere but I still can't have useful informations about pressure field and VM stress. How do I get them? I need the pressure exerted on the lower face of the sphere due to the inertia of the gas. Tell me if my question is not clear.
0 -
Hi,
With the current model setup you will not get any of these results, as the model is continuously moving.
Suppose if you are dropping the sphere on to a rigid surface/rigid wall you will get the pressure exerted by the SPH particles on the sphere.
0 -
Altair Forum User said:
Hi,
With the current model setup you will not get any of these results, as the model is continuously moving.
Suppose if you are dropping the sphere on to a rigid surface/rigid wall you will get the pressure exerted by the SPH particles on the sphere.
yeah but in order to have the right pressure I should apply a gravity of 20000g's, and this would break any shell!
0 -
Hi,
You can try making the shell rigid in such a case.
0 -
Altair Forum User said:
Hi,
You can try making the shell rigid in such a case.
Hi,
all right I tried to model the shell as a rigid body but I get a normal termination after one cycle, no apparent errors or warnings.
Can you check the model attached?
Thanks.
0 -
Hi,
When we are trying to impact a rigid to rigid there is no physics happening in the simulation. RADIOSS takes the rigid body time step to run the simulation which is very high and the run terminates in one cycle. And I think the same is happening in your model.
We have similar tutorial/webinar which is a tank drop simulation in which fuel is modeled with SPH. I recommend you to go through the same and follow the same steps for your simulation.
You can access the tutorial at https://altairuniversity.com/conceptual-design-of-a-3-wheeler-motorbike/conceptual-design-of-a-3-wheeler-motorbike-tank-drop-simulation/
0 -
Hello,
I want to consider suitable values for constant parameters coefficients (c1,c2,...) in LAW6 in hypermesh (Radioss) for fuel. where can I find the best values or how can I consider the best values which simulate the fuel in the best way.
Best,
sara
0 -
Hi,
Please go through the theory manual of RADIOSS on material laws.
Law6 is covered in this with the basic aspects also shown.
0 -
thank you so much George.
But I need some information about how can I select C1,C2,C3,.... in fluid such as fuel. At this theory manual just explain about gases.
I want to know based on what I have to define the pressure equation in law 6.
would you please give me another source?
Best,
sara
0 -
Hi,
The recommended parameters for input to LAW6 is as below:
C0 = C2 = C3 = C4 = C5 = 0 C1 = density*(speed of sound)^2Also,set a small Pmin value such as -0.1Mpa.
These are inputs I got regarding this material law. Unfortunately no other documents are available on this but will update you if I get more information on this.
0 -
Altair Forum User said:
Hi,
The recommended parameters for input to LAW6 is as below:
C0 = C2 = C3 = C4 = C5 = 0 C1 = density*(speed of sound)^2Also,set a small Pmin value such as -0.1Mpa.
These are inputs I got regarding this material law. Unfortunately no other documents are available on this but will update you if I get more information on this.
Thank you so much.
Please let me know if you get any new information.
I appreciate your help, always .
0