ERROR: Zero or negative volume for 3D-Element
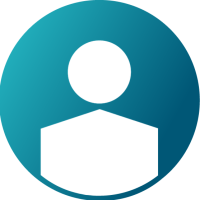

Hi,
I am trying to simulate a honeycomb impact, with a honeycomb structure, in Radios. I am following the tutorial of a HoneyComb in Altair University, but in the start of the simulation running, this error appear: Zero or negative volume for 3D-Element.
I attach you the file.
Thank you in advance.
Answers
-
Hi,
The NEGATIVE VOLUME error happens when solid elements are very deformed and their characteristic length goes to 0. For large strain formulation the time step of an element goes to 0 when the element is compressed. In RADIOSS Starter input file (Runname_0000.rad), use Ismstr =2 in the solid property and in RADIOSS Engine file (Runname_0001.rad) use the option/DT/BRICK/CST which will set the time step value tmin at which the solid elements will switch to small strain.This means that the solid elements using Ismstr =2 will use large strain formulation while their time step remains greater than tmin, and will then switch to small strain formulation.
I recommend you to remodel the honeycomb impact attenuator model. Please find the tutorial and model files from: http://www.altairuniversity.com/learning-library/modeling-and-analysis-of-honeycomb-impact-attenuator/
0 -
hello
I am also simulating a foam impact attenuation, i was able to run the file but it completes job in 3 seconds and does not generate a h3d file.
it says WARNING ZERO OR NEGATIVE VOLUME : 3D-ELEMENT ID : 653
ELEMENT IS SWITCHED TO SMALL STRAIN OPTIONive uploaded the 0000.rad files
Please someone help! it is extremely important for me to finish this simulation in 2 days!!
0 -
Hi,
Reviewed your model and please make these changes:
1). Remove the tied interface between the rigid surface and foam material, create an Type 7 interface between them.2). Create a self interface (Type 7) for the foam material.
3). While creating the initial velocity select all the rigid surface nodes including the rigid master node.
4). Finally review the foam material loading curve, The material loading behavior will be based on this curve.
I just changed the material parameters and made these changes and was able to run it.
0 -
Altair Forum User said:
Hi,
Reviewed your model and please make these changes:
1). Remove the tied interface between the rigid surface and foam material, create an Type 7 interface between them.2). Create a self interface (Type 7) for the foam material.
3). While creating the initial velocity select all the rigid surface nodes including the rigid master node.
4). Finally review the foam material loading curve, The material loading behavior will be based on this curve.
I just changed the material parameters and made these changes and was able to run it.
This is excellent work.
0