RADIOSS AMS
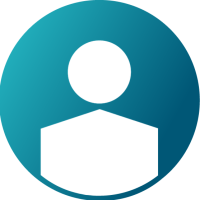

Hello all, I am running the quasi static simulation for 60ms the run time took around 4 hrs with 2k elements solid 17 formulation. How to reduce the run time with out much changing the results. I heard AMS will help to reduce time. If i use AMS what are the things need to be take care like energy,error %,mass error , etc.
Answers
-
Hi Arun,
We can control the time step using /DT/NODA/CST method and AMS (Advanced Mass Scaling) method.
When you are imposing a time step using /DT/NODA/CST, always check the mass error generating in the engine out (_0001.out) file. For a fair imposed time step, the mass error will be less than 5%. This method will add mass to the model.
The format of input for this method is: /DT/NODA/CST in engine file.
Tsca Tmin
Tsca=0.9 and Tmin=user imposing time step.
Another approach is AMS. This is similar to traditional mass scaling, except that the added mass does not increase the translational kinetic energy of the system. This allows the time step to be increased to significantly higher values as compared to traditional mass scaling without significantly affecting the results quality. /AMS must be present in the starter file and
/DT/AMS in RADIOSS engine file.
The input format is /DT/AMS. Tsca is .67 and Tmin is the target time step ideally 10 to 20 times higher than traditional mass scaling (/DT/NODA/CST).
Please review our Example 44 - Blow Molding with AMS in our Help Menu where AMS is employed.
Moreover, please review this video: http://www.altairuniversity.com/learning-library/considerations-about-time-step/ which is a webinar on time step and time step controlling methods
0 -
Hi George,
Thank you for the reply. how to find the target time step for AMS.I am not sure If i use AMS there will be mass added to the model. How to find how much mass added to the model.
0 -
Hi Arun,
To find the target time step you should run the model with /DT/NODA/CST with various time steps and should select a fair time from the trials. Ideally 10 to 20 times higher than /DT/NODA/CST you can select a time step for AMS.
A non-diagonal mass matrix is used to increase the time step on each line of the mass matrix and the total mass will remain constant
Mass added can be found from the mass error available in the engine out file.
Please check the AMS guidelines in our Help Menu also where all the theoretical aspects are described.
0 -
Hi George,
Thanks for the reply is it possible to find the energy and mass added for each parts in the model.
0 -
Hi Arun,
You can add /ANIM/NODA/DMAS and /ANIM/MASS.to find the mass variation and animation file for nodal masses.
Also,check energies of parts critical to your analysis by specifying parts critical in the output block (/TH/PART).
0 -
Hi george,
Thank you for all replies
1) I run the simulation with self contact. How to find the force between components at the contact locations. Is it possible with self contact.
2) I run the simulation with AMS. I have seen drastic reduction in time. Had a 2 runs with different Tmin (1.5E-5 & 1.5E-6) AMS approach for same model. I seen 3% diff. in stress result. Is it normal in difference?.
0 -
Hi Arun,
Create an output block for the contact (/TH/INTER) created. Since you varied the time step, you got a difference in results. Always select an optimal time step for the run.
0 -
Hi George,
no. of cpus makes differences in results?
0 -
Hi Arun,
They won't affect the result. Those parameters are for performance of the solver.
Please search for Engine Command Line Argument in Help Menu where all the options are explained.
0 -
Hi George,
Thank you for the reply. AMS working fine and i have a model with lot of penetration. But it is not my interest of area .Is it possible to exclude those elements from the contact.
0 -
Hi Arun,
You can use /DT/INTER/DEL for suppressing a slave node from the the interface if the time step is lower than the value given.
But I recommend you to use the depenetration tool available in HyperMesh (Tool>Penetration). You will get many options, including automatic depenetration, to fix this.
0 -
Hi George,
Thank you for the answer. Is it any other way is available,For example sofware like abaqus create a set with penetrating elements and remove those elements from contact by creating *contact exclusion keyword.
0 -
Hi Arun,
We have the option to remove the impacted node which fixes the time step from the interface, which is /DT/INTER/DEL.
0 -
Hi George,
I am doing a roll over crash Analysis.
Using type7 for global contact.
In Simulation, while using
'6 for Inacti ' in Typer 7 , the simulation runs good.While setting '0 for Inacti' , the mass increases steeply and so the error.P.S.: I am defining the time step using/DT/NODA/CST/00.9 0.0004Any Tip pls. Thanks in Advance.0 -
Hi Subhu,
When Inacti is set to 6 for any penetrations in solver interface the node is slightly depenetrated, thereby it takes care of penetrations in the model.Whereas for 0 it is default and works as per the values in the contact card. There could be some penetrations in the interface and since Inacti=0 it works as per the default values and this could be the reason resulting in large mass error in the model.
You can continue your run with Inacti=6 in the model.
The recommended contact parameters are as below for interface Type 7:
Istf=4
Igap=2
Fscale_Gap=0.8
INACTI=6
Gap_min=
Fric = 0.1
Iform=2
0