What's the possible reason for the large energy error
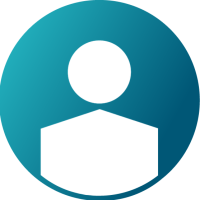

Hi all,
A drop simulation was solved by radioss. The energy error was negative at initial, but it increased slowly and became positive. At time 19.97s, the energy error increased suddenly to 99.9%, and the energy increased several times. The .out file was attached below.
Looking at .out file, the Interface 29 controlled the time step. In the model, the Interface 29 was self contact of foam material.
/INTER/TYPE7/29
DiPao_SelfContact
156 157
0.01
000
/GRNOD/PART/156
GrnodPartForInterfaceId_29
86
/SURF/PART/EXT/157
SurfPartForInterfaceId_29
86
What's the possible reason for this energy error problem (I think the energy error should be negative and the absolute value should be less than 5%)? How to solve it?
Best Wishes
Roy
Answers
-
Hi Roy,
The possible reasons for high energy error are:
>. Incompatible Kinematic Conditions
>. Timestep too low because of mesh size or high interface penetrations/distortions in the structure.
0 -
Altair Forum User said:
Hi Roy,
The possible reasons for high energy error are:
>. Incompatible Kinematic Conditions
>. Timestep too low because of mesh size or high interface penetrations/distortions in the structure.
Hi George P,
So how to solve it? As I mentioned before, the time step was controlled by interface 29 which was a self contact for foam package. The interface parameter also showed in first floor.
Best Wishes
Roy
0 -
Hi Roy,
For an interface responsible for low time step, these are some possible workarounds.
>.First check the gap that is used for this interface.The value must be physically realistic and based on shell thicknesses in case of contact between shells. In case of constant gap (Igap =0) with no input gap (Gapmin=0), RADIOSS determines a default value for Gapmin and you can check this value in the starter out file.
>.If some elements fail on the master side or on the slave side of the interface, it is important to set Idel =2 (or Idel =1) for this interface. This will prevent nodes connected to deleted elements whose stresses are released to impact with a possible high velocity.
>. Check stiffness defined (Istf). Try with Istf = 2. (Review Help Menu about Istf for /INTER/TYPE7)
0 -
Hi George P,
Thank you for the reply.
1. The contact type 29 was about solid self contact of foam (The foam was discretized with HEPE solid). So I used Gapmin=0.01mm with other parameters default. The card I used was listed in first floor.
2. None failure parameter was used in my simulation.
3. I will try different Istf value and feedback the results.
Best Wishes
Roy
0