Shell resultant stresses calculation flag - Shell element property
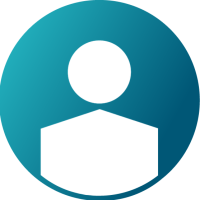

Hi everyone,
---------------------------------------------------------------------------------------------------------------------------------------------
There are 3 options in I_thick parameter (Shell resultant stresses calculation flag) in card Shell element property.
= 0: default set to value defined with /DEF_SHELL
= 1: thickness change is taken into account
= 2: thickness is constant
How should I choice this parameter?
--------------------------------------------------------------------------------------------------------------------------------------------
Base on tensile test experiment data (Force - Extension), I converted the data to Plastic strain - Stress for using MAT36. The Stress - strain in simulation and enter data is the same. But the result has a problem. The Force - extension curves are the same until maximum force. The simulation extension is shorter than experiment extension. I think there are some problems in the rupture phase. Which one should I check?
---------------------------------------------------------------------------------------------------------------------------------------------
Thank you very much!
Answers
-
Hi,
i recently did some simulations on tensile tests and expierienced that the ithick value has an inlfuence on the localization behaviour (i. e. what happens after the specimen force reaches its max value).
Since ithick=1 is the more accurate/higher cost option i would recommend to use this value. Furthermore to get better accuracy in your model use Iplas=1 (newton iterations for yield-surface projection)
0 -
Hi,
do you have used 'true' or 'effective' stress / strain curves (and of course starting with plastic strain, e.g. strain=0, stress=400) ?
The material laws always using this type of curves. So after the point of necking, engineering and true/effective values are very different...
I'm using the ithick equivalence in LSDyna, if thickness changes are significant and i have e.g. contacts in this area...
Regards,
Mario
0 -
Altair Forum User said:
Hi,
do you have used 'true' or 'effective' stress / strain curves (and of course starting with plastic strain, e.g. strain=0, stress=400) ?
The material laws always using this type of curves. So after the point of necking, engineering and true/effective values are very different...
I'm using the ithick equivalence in LSDyna, if thickness changes are significant and i have e.g. contacts in this area...
Regards,
Mario
Hi Mario,
I converted force - Extension --> true stress/strain --> True stress - Plastic strain (By shift the true stress - strain curve to the left hand side. Of course the starting plastic strain = 0).
I don't known, which parameters effect the behavior of sample after maximum stress value (in the rupture phase)?
0 -
Altair Forum User said:
Hi Mario,
I converted force - Extension --> true stress/strain --> True stress - Plastic strain (By shift the true stress - strain curve to the left hand side. Of course the starting plastic strain = 0).
I don't known, which parameters effect the behavior of sample after maximum stress value (in the rupture phase)?
Generally, Stress-Strain behaviour after reaching ultimate tensile strength is specific to the shape of the sample. That means, the values you get from the test after uts are generally not usable for describing a material's behaviour.
Another significant effect on localization/necking is mesh-dependancy. If it is of interest for you, try out several tension tests with different mesh size and look at the post-uts-values.
0 -
Altair Forum User said:
Generally, Stress-Strain behaviour after reaching ultimate tensile strength is specific to the shape of the sample. That means, the values you get from the test after uts are generally not usable for describing a material's behaviour.
Another significant effect on localization/necking is mesh-dependancy. If it is of interest for you, try out several tension tests with different mesh size and look at the post-uts-values.
Thank you Florian_lm!
I simulated tensile test with standard specimen - Standard specimen E8M - 09. Now the stress - plastic strain simulation and enter data match together. But the elongation is so short - The sample was failed after over the maximum force value a little bit. Would you give me some suggestions? I think there are some thing wrong in fracture phase - I used the formulations in Example 11 - HyperWorks turtorial to get the Stress - Plastic strain curve.
Thank!
0