Failure /FAIL/JOHNSON and /FAIL/TAB1
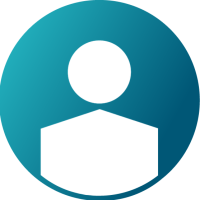

Hello,
I have a solid model and I want to simulate it with a johnson failure model. Can someone tell me how to use /fail/johnson and /fail/tab1 together? I allready read the user manuel but I dont know how to combine them. Do I have to creat /fail/tab1 and /fail/johnson in my model? What is the correct format for table 1 in this case?
Best regards
Henner
Answers
-
Hi Henner,
You can use both failure cards for the same material. You have to create two separate failure cards and has to recall the material.
The Johnson-Cook failure model is often used to describe the ductile failure. Stress triaxiality has great influence in ductile material failure.In /FAIL/TAB1 tabulated functions can be used to describe the stress triaxiality. /FAIL/TAB1 is based on damage accumulation. But if you have all the parameters required for /FAIL/TAB1 I would recommend you to use /FAIL/TAB1 only.
0 -
Hello Geroge,
the johnson failure model gets the triaxility from the simulation/geometry, right? In fail/tab1 I have to define triaxility? But how does that work in combination with /fail/johnson card?
Another question:
Do radioss has a special failure card for brittle materials?
Thank you, Henner
0 -
Hi Henner,
Yes,in Johnson Cook also triaxiality can be described. In the Johnson-Cook failure model, there are three parts of material tests:
In a simple case, only the first part, triaxiality influence is considered. Then failure strain is:
/FAIL/TAB1 is an advanced card. /FAIL/TAB1 is based on damage accumulation. Beside stress triaxiality, Lode angle is another important character to describe the material failure, and can also be defined in /FAIL/TAB1 with tabulated function. Please go through the Help on /FAIL/TAB1 where an example card is shown with inputs.
We don't have a specific failure card for brittle materials. But for brittle materials like glass you can use /FAIL/FLD card.
0 -
Hello,
but in /fail/johnson you only set the parameters D1,D2,D3,.. The triaxility is calculated by the simulation. So if I combine fail/johnson and fail/tab1, in the johnson card the triaxility will be calculate by the simulation and in tab1 card I have to set it? That doesnt make sense.
I dont understand in this example how they calculate the fail strain? Maybe you have an example where /fail/johnson and /fail/tab1 is combined?!
/fail/fld is only for shells. What kind of failure model would you prefer for brittle materials simulate with solids?
0 -
Hi,
/FAIL/JOHNSON and /FAIL/TAB1 are very similar and work on the same basic idea where a plastic failure strain versus stress triaxility curve has to be defined. In /FAIL/JOHNSON the plastic failure strain versus stress triaxility is created by defining the D1, D2 , D3 parameters which are used in the Johnson-Cook equation.
In /FAIL/TAB1, the user defines a /FUNCT which represents the plastic failure strain versus stress triaxility curves. In /FAIL/TAB1 you can define different /FUNCT which represent different plastic failure strain versus stress triaxility curves at different strain rates. In /FAIL/JOHNSON the strain rate affect is defined via the D4 parameter input.
So you should not need to use both /FAIL/TAB1 and /FAIL/JOHNSON in the same model since they do the same thing. If you have a plastic strain at failure for compresion (trixaility= -1/3) shear ((trixaility= 0) and tension (trixaility= 1/3) then you can do a curve fit to calculate the D1, D2, and D3 paramters. You could also look at /FAIL/BIQUAD which uses two quadratic equations to define the plastic failure strain versus stress triaxility curves and has some built in starting values for some different materials.
Thanks,
Andy
0 -
Hello,
If I use only /fail/johnson card with D1,D2,D3 I will make a mistake because I have solid elements.
hyperworks help: ' In /FAIL/JOHNSON, D1, D2 and D3 describe the failure of shell element, but for solid element, Johnson-Cook failure is not enough. It only describes cases of plane strain, where Lode Angle parameter ξ describes the ductile fracture in a solid.'
So I have to use /fail/johnson and fail/tab1 together to get the effect of the lode angle. But I dont know how to combine them correctly. In fail/johnson I have to set D1,D2,D3 and then in /fail/tab1?
Thank you, Henner
0 -
Hi,
No, you do not need to use /fail/johnson and fail/tab1 together to get the effect of the lode angle. The /FAIL/TAB1 includes the effect of stress triaxiality and lode angle. This is Card 3 in /FAIL/TAB1 from the manual and there is an example for solids in the /FAIL/TAB1 manual.
To use /FAIL/TAB1 with lode angle you need test data showing the plastic failure strain at different triaxiality values and different lode angles. Do you have this kind of test data? If you only have plastic failure strain versus triaxiality data and no lode angle then you can still use /FAIL/TAB1 with only defining of plastic strain versus triaxiality. The /FAIL/TAB1 manual has an example for shells without lode angle which could also still be used for solids.
It really depends on what failure data you have available. For years engineers got reasonable results by just entering one plastic strain at failure in a material law and it didn't matter the stress triaxality or lode angle (for solids).
Now there are more advanced methods with the /FAIL options. Going from most basic to more complex, I would rank the failure models like this:
- Enter 1 plastic strain at failure value in a material law like /MAT/LAW2 or /MAT/LAW36
- /FAIL/JOHNSON
- /FAIL/BIQUAD (nice balance of easy with advanced features)
- /FAIL/TAB1
To use more advanced failure models you need to have data to use with them. Even so I would start basic and make sure your simulation is reasonable and then move to a more complex model if you have data for that model.
Thanks,
Andy
0 -
hi all,
I have tried FAIL/JHONSON HOOK but i did not able capture the necking behavior !! after the starting of element deletion. it is behaving like brittle failure !! my load is 500mm/s
0 -
Hi,
Please check the material properties.
If everything is fine with the material, can you remove the EPS max and check if that helps.
0 -
Ya i did not include the EPS max. Please find the attached RADIOSS file.
0 -
thank you for sharing the file
I will check and update you soon,
0 -
same question. thanks for sharing
0 -
Hi,
Can you plot IE and KE and share the same?
0 -
Hi @jsk459
Sorry for a late reply.
I think the problem is coming from the rupture of the elements. That is why you see a sudden slump in reaction force.
I have modified some parameters and will let you know my findings,
0 -
Hi sir good morning, why should we use failure entity card in crash application. Is there necessary to use every time sir.
0