Multi Material FEA and Topology Optimisation
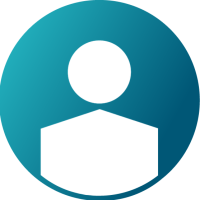

I am trying to topology optimize a multi-material part.
I imported an assembly iges file and defined properties for 2 different parts, how do i give the contact between the 2 parts. How to perform a basic FEA and topology optimize these kinds of parts.
Answers
-
0
-
Hello Prakash,
The previous file had 2 parts in one IGES file.
The assembly has 2 parts bushing and truck
I am attaching another file which has 2 iges files in it. I am looking for ways to connect these 2 parts, mesh them and topology optimize them.Assembly description:
1. There is a cylindrical part (bushing) which would concentrically align to the curved surface of the pin and inner curved surface of the truck.
2. The base of the bushing would align to two different bases on the truck.
Attached is an image for clear understanding
0 -
Not sure what your end objective is and not sure why you have both the parts in a single component.
What exactly you want to optimize among the two?
Make different components for different parts and this makes life easy with modelling and understanding.
You can connect either with nodal equivalence or using RBE2s or using Tie contact.
0 -
I made the model into 2 components independently meshed the components. Then i used TIE contact to connect them along 4 surfaces. The final aim of the optimization is to reduce the weight of the truck. The truck is made of Aluminium and bushing is a flexible rubber like material which remains as it is throughout the optimization.
I ran a basic FEA analysis and got the following errors:
There were 4 error messages during input processing.
The first message is repeated below:
*** See next message about line 2033 from file:
C:/Users/Student/Desktop/HM/FEA/truck.fem
'TIE 1'*** ERROR # 1000 *** in the input data:
Incorrect data in field # 4.0 -
Hi Dinesh,
Pin_Curv_out does not have any master and slave entities. Please check and update.
0 -
Hello Prakash,
thank you the problem is resolved0 -
Hello Prakash,
I ran an FEA Analysis for the model with two material materials for the truck, Aluminium and Nylon.
I got the same displacement and stress results for both the materials, even tough the Young's modulus for the materials is different.
Is this some how related to the pressure given on the surface. Are the units of Pressure N/mm^2.0 -
HyperMesh is unit neutral, You need to maintain a unit consistency.
If your input units are in SI units then the results will be in same unit system.
0 -
Hi,
Is it a linear static analysis? Are the loads and boundary conditions and other parameters exactly same? If everything is same and only material is changed, stress will be same as it is independent of material in linear static case but the displacement will be different, higher the young's modulus lesser it will be.
0 -
Thank you Gopal,
Yes the analysis was linear static, and the boundary conditions and other parameters are exactly the same. The results like you say are very comparable for materials as different as Titanium and Nylon! If not linear static, can you suggest what other analysis I can use?
Also, for the topology optimization i am trying to minimize the volume, and gave the Yield Strength of the material as the constraint for stress, volume upper bound as 0.7 and 0.3 as lower bound. The objective is to minimize compliance. I am getting an Error 14 - Missing RANDPS, which is the loading.Are the constraints and objective correct?
Please look for the attached HM File.0 -
Hi Dinesh,
I used your models and displacement results are different.
Altair Forum User said:, volume upper bound as 0.7 and 0.3 as lower bound.
Is it volume you are using or volume fraction?
0