brittle rupture
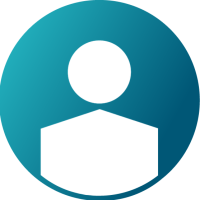

Hello Altair team,
I should simulate the impact of an hammer drill bit on a concrete brick. I followed the radioss tutorial on your youtube channell but I can't manage to have my model working properly. The problem is that the bit go through the brick without breaking it. Should I define a contact between the bit and the brick? In addition, the model checker tells me that the P14 property is incompatible with the material law 10, the one that I used for the brick, how can I fix this?
Thank you very much,
Luca
Answers
-
Hi,
You have to define a contact between the drill bit and concrete block. And for modelling rupture you need to define a failure card. Please go through failure models in RADIOSS Help and check the compatibility with the material. /MAT/LAW10 is compatible only with solid elements and I feel it should not be a compatibility problem with Type14 property.
0 -
ok, thank you. Which contact Type should I use?
The Help you are talking about is the manual posted on this forum?
0 -
Hi,
You can try with a Type 7 interface, which is general purpose interface used in RADIOSS. If there are edge to edge cases you can model with Type 11 interface.
Please go through https://www.youtube.com/watch?v=mLGwVwYSmt4&list=PLQ7KUGFuVz4u5y3SvIEIU07427-gATaG6&index=4 which is a video series of RADIOSS training and Chapter 4 shows defining contacts.
I was referring you to the online RADIOSS Help. From your HyperMesh press H in your keyboard so that Help will open and you can search for required parameters.
0 -
Thank you!
Type 7 contact seems not working on my model, I have both the bit and the block meshed with a tetra mesh, which contact for solid elements can I try?
0 -
Hi,
For solid -solid contact you can try with Type 7 or Type 11 contact. Provide a small gap in between and also in Type 7 provide a Gapmin value.
Please share a snapshot of the model so that we can understand the model setup also.
0 -
Hi,
The run has been terminated due to high mass error and this is because of the imposed time step. If the imposed time step value is high more mass will added into the model which leads to run termination. Ideally the mass added should be less than 5% ie.05. The mass error you can observe in the _0001.out file which is listed under DM/M.
Try with a lower time step value in /DT/NODA/CST keyword.
Also for Type 7 interface input these recommended parameters:
Istf=4
Igap=2
Fscale_Gap=0.8
INACTI=6
Gap_min=
Fric = 0.1
Iform=2.
0 -
Hi George,
thanks to your advice I had my model partially working. However, it runs only if I use the material law 2 for both components.
But when I select material law 10 for the block I get this error:
NC= 0 T= 0.0000E+00 DT= 1.6642E-08 ERR= 0.0% DM/M= 2.1392E+03
ANIMATION FILE: modelloA001 WRITTEN
MESSAGE ID : 207
** RUN KILLED : TOTAL MASS ERROR LIMIT REACHED
NC= 44 T= 8.0157E-06 DT= 2.1917E-08 ERR= 99.9% DM/M= 2.1286E+22
ELAPSED TIME= 7.27 s REMAINING TIME= 446.03 s
ANIMATION FILE: modelloA002 WRITTENIs it due to the absence of a failure card for the concrete block?
0 -
Hi,
Ensure the material parameters are correct for /MAT/LAW10. Can you please share the engine out file (_0001.out).
0 -
Hi,
Thank you for your help. I used the parameters for concrete as in the example for material law 10 in the reference guide. I just changed the units of measure from kg/dm3 to ton/mm3. The run termination with those errors occurs as soon as the bit touches the block, or few timesteps later. It seems that the energy limit is reached in the bit and not in the block but I can't explain why.
I'm attaching the output file and the model, so that you can see which component the errors are related with.
Thank you very much
0 -
Hi,
It seems I managed to solve the problem , apparently the BC on the brick were incompatible and now the simulation works.
Can you advice me which failure card I could use to simulate the fracture?
thank you very much,
Luca
0 -
Hi Luca,
Please go through the Help on failure models. Only 3 failure models are compatible with Law10 (/FAIL/TENSSTRAIN, /FAIL/TBUTCHER, /FAIL/ and /FAIL/ENERGY).
You can try with /FAIL/ENERGY or /FAIL/TENSSTRAIN which fails based on specific energy and strain respectively.
Please go through the Help Menu on these failure models.
0 -
Hi George,
As you can see in the picture, I think I managed to obtain a very accurate simulation of the brittle rupture. Now I'm wondering about how to quantify the effect of the percussion. I think a simple way to do it is to count the elements removed due to the total failure strain. Is there a way to count all the elements removed?
0 -
Hi,
I don't think we have a direct way to count the failed elements.
As a workaround, you can try this: Export the deformed model from HyperView to RADIOSS solver deck format and import in HyperMesh and you can check the element count in HyperMesh. Check the difference in both the cases for the concrete part.
0 -
Hello,
I'm still struggling with this model but i'm seeing many improvements....
I'm now facing a problem with Hourglass energy. It seems that in the brick, at the end of the simulation, Hourglass energy reaches the 20% of the internal energy. So, following the advice in the radioss ebook, I tried to assign many kind of Isolid flags for its solid property. With Isolid 17 and 24 the model loses the brittle behaviour.......why does it happens? which flag should I use to reduce the HG energy?
Thank you very much,
Luca
0 -
Hi @luclore
unfortunately, @George P Johnson is inactive since May.
To avoid hourglass use full integration (Isolid=14,17) or reduced integration with physical stabilization (24). Try this combination: Isolid=14, Inpts=222 and Icpre=1.
Also try different combinations with Ismstr (it does not affect hourglass but might influence failure mode). What failure model is used?
0 -
Thank you for the advice.
I'm using the failure in tensile and compression stress defined in MAT24 (concrete) and it seems to be pretty accurate in terms of size independent fracture energy.
I'm just doubtful about the D parameter that defines the young's module in tensile strength... I'm using D=0.2 since that the module in tensile is defined as E_c(1-D).
Could that interact with the Isolid flag?
I'm not using any additional failure card.
0 -
I'm not sure what you mean by D parameter: Dsup is Concrete maximum damage.
ft/fc is Concrete tensile strength which is defined as the ratio of tensile divided by compressive strength and is 0.1 by default.
You should get data for LAW24 from the following physical tests:
- Get density by weighing a specimen
- Get Young modulus with a cylinder compression test
- Poisson coefficient (usually assumed to be near 0.2)
- Get ‘fc’ from Compression strength (using cube compression test)
With the following additional tests, material LAW24 will be more accurate (in fact, providing data fits the failure envelope):- Get ‘ft’ from tensile test:
‘ft’ is direct tensile strength. This test provides ‘ft/fc’ value for LAW24.
- Get couple of (ft,Ht) from Splitting tensile test:
Get couple of (ft,Ht) from Splitting tensile test:
‘Fst’ is splitting tensile strength in Splitting tensile test. We assume that Fst=ft. Then you need to model this test to fit limit strength (ft) by validating ‘Ht’ value. This test should be with very slow velocity, so use HA8 solid property for in Splitting tensile test.
- Get ‘fb’ from Biaxial test and get (f2,s0) from confined test.
Tutorial RD-E: 4700 Concrete Validation and attached document might be useful.
From my understanding, the Isolid formulation does not interact with a material definition.
0 -
Yeah I mean Dsup.....
From what I see on the reference guide it is needed to reduce the young module in tension , but, if so, why is set to default to 0.999 ? This means that E in tension is reduced to the 1% of the original. I think that its appropriate value should be around 0.3 so that E in tension would be around 70% of E in compression.
Am I misunderstanding its physical meaning?
0 -
My interpretation of tensile damage graph from Radioss help:
-the young's modulus in tension is the same as in compression until ‘ft’ (direct tensile strength)
-then Concrete tensile tangent modulus or Ht (-Ec by default) is applied
-until it bisects with modulus given by equation (1-Dsup)Ec which is actually 0.0001% of Ec by default-effectively no stiffness at large strains
-until εmax or Concrete data total failure strain is reached and elements are deleted
0 -
Altair Forum User said:
Hi George,
As you can see in the picture, I think I managed to obtain a very accurate simulation of the brittle rupture. Now I'm wondering about how to quantify the effect of the percussion. I think a simple way to do it is to count the elements removed due to the total failure strain. Is there a way to count all the elements removed?
Hi luclore which failure model did u use? thx
0