fuel sloshing
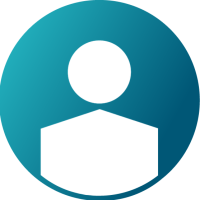

Answers
-
Good morning. If i understand correctly, i would suggest using the imposed acceleration or imposed velocity which can be founded in Tools -> BCs Manager. Under direction, XX, YY and ZZ correspond to rotations over the x,y and z axis. You can define a curve there and apply it to the tank i suppose. All of the above refer to RADIOSS BLOCK 120. Tell me if you need anything else.
0 -
Thanks...One more thing I would like to know that how the connections will be modeled in composite parts.
0 -
By connections you mean adhesives? Are you using shells, solids? You need to be a bit more specific friend
/emoticons/default_wink.png' alt=';)' srcset='/emoticons/wink@2x.png 2x' width='20' height='20'>.
0 -
Please find detail as below;
This is sandwich structure, both foam core and face sheets are modeled with shell. thinking to model core as solid.
Adhesive between face sheets and foam core. need to understand about the modeling of Adhesive. as well as interested to see Delamination (between plies) and or debonding (between skin and core). Is there any option to configure cohesive elements in Radioss block ?.
0 -
If you want delamination and cohesive elements it is highly likely that you are in the wrong place
/emoticons/default_wink.png' alt=';)' srcset='/emoticons/wink@2x.png 2x' width='20' height='20'>. By that i mean that sadly RADIOSS is not doing a good job helping us (i want that too). There are a couple of things you can try though.
Adhesives:
First of all take a look at MAT59 (http://www.altairhyperworks.com/hwhelp/Altair/hw12.0/help/hwsolvers/mat_law59_connect.aspx). It is used to model glues and spot-welds, etc. You can also link it to failure keywords such as the /FAIL/CONNECT (http://www.altairhyperworks.com/hwhelp/Altair/hw12.0/help/hwsolvers/fail_connect.aspx).
Laminates:
What material law are you using for your plies, MAT25? If yes there is the GAMA_INI and GAMA_MAX values which dictate delamination which is also plottable through DAMAGE 3 (http://www.altairhyperworks.com/hwhelp/Altair/hw12.0/help/hwsolvers/anim_eltype_restype.aspx). You got a lot of reading to do, so i am going to leave you to it.
There is no easy way around.
0 -
Altair Forum User said:
Good morning. If i understand correctly, i would suggest using the imposed acceleration or imposed velocity which can be founded in Tools -> BCs Manager. Under direction, XX, YY and ZZ correspond to rotations over the x,y and z axis. You can define a curve there and apply it to the tank i suppose. All of the above refer to RADIOSS BLOCK 120. Tell me if you need anything else.
Good morning..Since I have roll rate in terms of angular acceleration in rad/ms2 ( here X axis is rolling axis of aircraft), when I impose rotational acceleration about xx to the tank (created local system at the CG of the aircraft and assigned all the nodes to this local ) with defining curve over time and ISKEW asf local axis and fixing bulk head of the tank in all dof except rotational XX free, I can see fuel sloshing, but not rolling of fuel inside the closed tank which is of courses partially filled (50% air and 50% o fuel). Here I am trying to keep tank in static condition and only fuel should roll inside the tank as aircraft takes turn. It seems something wrong I am doing while defining boundary condition and loading. if someone worked on this area, please your suggestions would help me to overcome this problem.
0