Questions on Radioss NLGEOM Solver
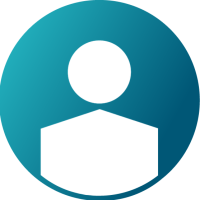

Hello,
I have a few questions on the Radioss NLGEOM solution. The model file is attached (please rename from jpg to hm):
1) When there are multiple subcases e.g. loading and unloading of a structure, it happens that I can not choose the second subcase in HyperGraph Postprocessing. An error message occurs. Is there a way to prevent this error message?
2) The process to define the loading / unloading sequence of a structure is described in Radioss Tutorial RD-2100. It is described to uncheck the LOAD entry for the second (unloading) subcase. However if I do this for my model, there is no connection between the loading and unloading sequence in the Hypergraph stress-strain curve. How do I need to define the unloading sequence correctly?
3) When using MATS1 with Hardening Modell 3 (70% isotropic und 30% kinematic Hardening), Material curve via TABLES1, Total Strain Curve, I see a good correlation to the tested prove for the loading sequence of my model. However the unloading sequence does not have a good correlation. Do you have any hints and tipps, e.g. to define a different Material Law or to change my loadcases, in order to reach a better correlation to the test curve (blue is the test and red the simulation curve)?
Answers
-
-
I can give some hints for question 1 & 2:
1) If you fail to read the curves from the H3D file, please try to write and read a Time History File instead. To do so, define the XHIST entry (see the help on XHIST, how to do so). The XHIST can be found in HyperMesh under setup -> create -> output block. The output must be referenced in the subcase and its output sequence must be defined in the DTTH option of the NLPARMX card.
The TH files are usually smaller than the H3D and can be usually handled better by HyperGraph than the H3D(as there is no model data but pure result data included)
2) The sequence in the Radioss Tutorial describes a quasi - static loadcase. In your case, you do have a Non-linear geometry subcase, which always needs a NLOAD or LOAD entry, even for the unloading sequence.
For question 3), I hope that my colleagues can give an appropriate answer.
0 -
About question 1, which version are you using? this model works fine in my 12.0 version
If it is 11.0 it might need the latest update,
see Forum » Modeling (Preprocessing) » HyperMesh » To identify the software update/patch that has been installed in your machine
Looks like perhaps the unloading sequence missing the load card is the reason for question 3 as well
0 -
Hi,
to simulate an unloading condition using NLGEOM, create another loadstep without any load checked (no LOAD or no NLOAD active) continue the simulation from previous NL case. to do this:
Edit the unloading loadstep (or card edit from load step in model browser), and check CNTNLSUB toggle to SCID and select SCID (sub case ID) as the previous load case.
0 -
Hello,
the difference in the pressure loading might stem from the material model. You can use the Material MATX36 to define a separate stress / strain curve for pressure load cases. The needed parameter in the material law is TPID. Help says:
TPID is used to distinguish the behavior in tension and compression for certain materials (i.e. pressure dependent yield). This is available for both shell and solid elements. The effective yield stress is then obtained by multiplying the nominal yield stress by the yield factor PSCA corresponding to the actual pressure.You might need to adapt the hardening parameter ICH as well, as the type of hardening is influencing the pressure behaviour of the material a lot (Bauschinger effect).
Kind Regards
Jan0