element deformation contour plot visulazation
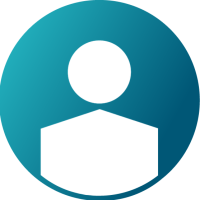

Answers
-
Since the information available is very less to judge,
Can you refine the mesh at contact surface and check if that helps?
0 -
Dear Prakash, this is the previous analysis results of same type of analysis.
here, I havent used R body element for pressing plate.
but in above case, i used. all other things are same.
0 -
Hi
How did you model you rigid element? I mean which nodes you selected for rigids?
0 -
Grey part, pressing plate
mater node= pressing plate arc center
slave nodes= all pressing plate nodes
0 -
I think having a rigid will change the stiffness on contact and this is what makes the difference.
What is the Istiff on contact card with and without Rigid?
0 -
ring and housing are elastic
type 24
p14_solid
but time step is different
0.1 sec= 20mm disp
0.01sec= 10mm
0 -
What energy plot says?
0 -
I kept it default
0 -
Altair Forum User said:
What energy plot says?
I mean what is behaviour of energies? Kinetic internal and hourglass?
0 -
Altair Forum User said:
ring and housing are elastic
type 24
p14_solid
but time step is different
0.1 sec= 20mm disp
0.01sec= 10mm
Didnt get it? Time step?? or the end time you want to say??
0 -
0
-
Altair Forum User said:
ring and housing are elastic
type 24
p14_solid
but time step is different
0.1 sec= 20mm disp
0.01sec= 10mm
Clearly you are loading with rapid velocity in second case, In second case you are getting this element distortion?
0 -
sure i'll try it out.
there are two cases
1. with rigid
2. with out rigid.
geometry is different in both cases but phenomenon is same.
for first case
disp curve is
X Y
0sec 0mm
0.1 sec 20 mm
for second case
X Y
0sec 0mm
0.01 sec 10 mm
my question is will time step result into such elemental behaviour?
0 -
Altair Forum User said:
sure i'll try it out.
there are two cases
1. with rigid
2. with out rigid.
geometry is different in both cases but phenomenon is same.
for first case
disp curve is
X Y
0sec 0mm
0.1 sec 20 mm
for second case
X Y
0sec 0mm
0.01 sec 10 mm
my question is will time step result into such elemental behaviour?
are you doing an impact analysis or an quasi-static analysis? I think it sholud be a case of quasi static analysis. Surely what you are giving as loading time is too rapid. I suggest you take default value of 0.3 for your loading and check the results.
0 -
Altair Forum User said:
are you doing an impact analysis or an quasi-static analysis? I think it sholud be a case of quasi static analysis. Surely what you are giving as loading time is too rapid. I suggest you take default value of 0.3 for your loading and check the results.
what is the energy error you are getting for the simulation?
0 -
I'll revert on energy plot,
having licencing error, server is down.
Thanks guys for the support.
0 -
0
-
Altair Forum User said:
1.Make changes in property and try using QEPH formulation to aviod hourglass energy.
2. Give your loading gradual to avoid sudden impacts you may consider to give the end time as 0.3.
Apply these changes and check the results. You please go through the previous content for Radioss regarding energy error and troubleshooting techniques.
0 -
@Nachiket Kadu @Prakash Pagadala @George P Johnson
I want to check pressing force required to insert ring into hub,
I have simulated 1/4th geometry.
and got x N of force.
and suppose, i have full geometry, what will be the pressing force?
will it be 4 times of first case or same?
0 -
Altair Forum User said:
@Nachiket Kadu @Prakash Pagadala @George P Johnson
I want to check pressing force required to insert ring into hub,
I have simulated 1/4th geometry.
and got x N of force.
and suppose, i have full geometry, what will be the pressing force?
will it be 4 times of first case or same?
Yes, we can sat that reaction forces are proportional to size of the component.
0 -
you mean it will be 4 times, Right.
0 -
Hi,
Try these workarounds:
Hourglass seems to very high in the model.
For solid elements use Isolid-24 and if any shell elements are there use ishell-24 and N-5.
For the contact keep Istf to 4, so that minimum of master and slave will be calculated. Also give a minimum stiffness (Stmin-1000N/m). Plot the global contact energy also.
Ramp the load in 300 milliseconds so that the solution will be stable.
Once these changes are done, run the simulation and plot the hourglass energy for each part so that we can see which part is contributing more.
And finally make sure correct material type and parameters are used.
Which material is used for this?.
0 -
Thanks for the suggestions,
Bearing steel is used for ring, and aluminium is for housing.
0 -
what if I have tetra elements?, will Isolid -24 work?
0 -
Hello,
Isolid is to choose hex element formulation, whereas I_tetra option is used to select the tetra element formulation. Isolid will not be considered if you choose for Tet elements
0 -
will it be fine for hex?
0 -
Yes, seems fine, but disable Icpre option.
0 -
Hi Ganesh,
Yes, Isolid 24 with physical stabilization will take care of hourglass issue.
Initially try the problem with out FRICTION and look for energy plots. check for the internal, K.E, hour glass& contact energy
Check with the material properties
0 -
-
Altair Forum User said:
You can see that houglass energy is still high. This model is going into hourglassing mode. What element formulation you are using? If you are using underintergrated elements, your hourglass energy should be as minimum as less than 5-10% of total energy.
0