Radioss Ideal time step
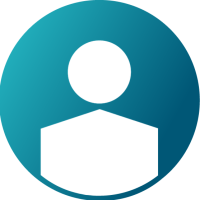

Dear All,
I am simulating the contact behaviour of gear with Radioss. I had given time step equal to 0.1 sec is it sufficient for this type of problem?? My stress level is exceeding my yield limit, also Its taking too much time to simulate the analysis may i get any tip to reduce my cycle time and suggestion on cycle time. Please refer attached file for same. I applied 80 Nm moment alongcentral axis and fixed the gear to simulate stress due to initial torque.
Answers
-
Time step size in explicit dynamics depends on the characteristic length 'L' of an element and the wave speed 'c' as follows: delta_t = L / c.
If you are imposing a time step, make sure that it will not add more mass into the model.
Solution time varies based on the time step of the analysis.
If the time step is reducing during the run :
check which object is responsible for the low time step (.out file). It can be an element, a node or an interface.
For an element, check the related material.There must not be an error in the units system that this data is given in. check the element size also
For a node, check the characteristics of connected elements. If the node is on the master side or the slave side of an interface, this interface must be verified.
For an interface, the gap of the interface must be verified if some failure happens on the master or the slave side of the interface
Please refer the video below for timestep in Radioss Explicit.
https://altair-2.wistia.com/medias/o0bfml9ah5
.0 -
HI,
i have observed that due to the interface the time step is reducing. How can i rectify it ? Please explain the line 'the gap of the interface must be verified if some failure happens on the master or the slave side of the interface'
0 -
Hi,
The time step computation for an interface prevents a slave node from crossing the master surface while ensuring the performances of searching the contacts through the interface.
While defining an interface it's always recommended to provide a Gapmin value. Use the recommended parameters for Type 7 interface.
After defining interface always check for any penetrations in the interface and remove them if you find any.
0 -
Hi,
Thanks for your reply.
what is the recommended Gapmin value for brick elements ?
0 -
Hi,
That depends on the case, suppose the distance between the components is 2 and in such case I'll provide a Gamin value of 0.5 so that when the distance reaches 0.5 the contact will be established and it will be stable.
0 -
ya now i can understand. In my model i think the components are so near like 0.1mm so i have applied 0.1mm as Gapmin and removed the penetrations. Is that will make sense ?
0 -
This seems fine, so that it will try to maintain 0.1mm gap.
0